3 Ways to Improve Industry 4.0 OEE
Overall equipment effectiveness (OEE) has been a leading manufacturing performance metric for decades. As Industry 4.0 has taken off, manufacturers now have a range of new tools and techniques that can improve their OEE scores. As facilities rely more on high-tech equipment, this metric has also become increasingly crucial.
As of 2019, there were 97.7 million connected devices in use in the manufacturing industry. Experts predict that figure will surpass 150 million connections by 2025. With so many connections gathering such vast amounts of data, manufacturers have more resources than ever to use in their OEE calculations.
While Industry 4.0 provides the means to improve machine health monitoring, it also raises the need for it. Industry 4.0 has made manufacturing a faster, more flexible, and less wasteful sector, raising consumers’ expectations. As key industry players become faster and more resilient, they set a new standard that others must meet.
In Industry 4.0, manufacturers must deliver higher performance to meet rising demands. At the same time, this trend equips them with the tools they need to pursue those goals. With these factors in mind, here are three ways manufacturers can improve Industry 4.0 OEE.
1. Continuous Operational Monitoring
Machine health monitoring is a central part of calculating OEE, and Industry 4.0 provides new and improved monitoring methods. The days of periodic manual checks are now fading. The internet of things (IoT), Industry 4.0’s foundational technology, enables continuous remote monitoring.
By integrating “smart” or internet-connected sensors into machines, technicians can track a machine’s operational parameters remotely in real-time. This includes factors like temperature, vibration, noise, and even variables like motor lubrication. In the past, technicians would have had to pause operations to check some of these data points, but now they can do it without interfering with production.
This data improves OEE calculations by providing readily accessible, real-time insight into the underlying causes of a machine’s score. For example, a robotic welding arm may be running slower than normal, holding its OEE rating back. IoT sensors can reveal that the arm’s electrical insulation, the cause of 56% of electric motor failures, is damaged without workers stopping production to investigate.
Since manufacturers can access this data from the cloud in real-time, it leads them to the root of the issue faster. They can then address the problem and improve the machine’s health and performance sooner, leading to faster OEE improvements. Manufacturers can even use these systems to provide real-time alerts, helping them improve machine performance before a scheduled check.
2. Predictive Maintenance
Traditionally, most manufacturing operations either perform preventive maintenance according to a schedule or reactive maintenance, where they run machines to failure. Industry 4.0 enables manufacturers to adopt predictive maintenance. This practice, which builds on operational monitoring, provides the benefits of each alternative without their respective downsides.
Predictive maintenance uses big data or AI-powered analytics modules to analyze historical and current operational data. With this information, these analytics engines can then predict when a machine will fail or need maintenance. Manufacturers can then schedule a time to fix it and resolve the issue before it becomes a more pressing concern.
This approach minimizes unplanned downtime that would arise out of reactive maintenance since it prevents breakdowns. Considering how this downtime costs manufacturers $50 billion each year, predictive maintenance represents considerable savings potential. Improved uptime will also translate into higher OEE, as it raises a machine’s availability score.
Predictive maintenance also reduces costs associated with schedule-based preventive maintenance. While these maintenance strategies also prevent breakdowns, they may lead to unnecessary downtime and expenses due to unneeded repairs. Since predictive maintenance is data-based, not schedule-based, it only recommends due repairs, maximizing uptime.
These IoT-based machine health monitoring strategies also improve OEE by minimizing machine health-related quality issues. If a laser cutting machine, for example, were overheating or getting stuck in one position, it wouldn’t consistently produce quality products. Predictive maintenance would fix these machine health issues before they affect quality, preventing waste.
3. Targeted Notifications
Industry 4.0 technology can further improve OEE calculations by offering more granular, targeted insights and alerts. In addition to providing a continuous stream of remotely accessible data, IoT sensors in machines can offer more specific readings. This specificity lets manufacturers address any issues more effectively, enabling more in-depth OEE analysis and improvements.
Targeted notification systems can send alerts to only those who need them based on pre-set parameters. A smart, rule-based system analyzes the data at hand to determine which employees an update is most relevant to, then alerts them. For example, if it detects a machine is running at an abnormally high temperature, it could alert a technician who specializes in the overheating components.
This targeted approach to analysis and notifications improves overall productivity by not sending superfluous alerts to employees who don’t need them. It ensures that only the people most relevant to or most skilled in the task at hand see these updates. In turn, the most qualified workers to handle a given issue are the ones who address it, ensuring the most effective responses possible.
With machine learning algorithms, these systems can take note of how experts maintain a machine or what they do with given data. If an expert is unavailable when an alert arises, the system can then find the next most relevant worker and show them how the expert typically handles similar situations. As this process continues, manufacturers will foster a more highly skilled workforce.
Ongoing data collection and analysis will also reveal which changes have led to the most significant OEE improvements. These insights enable manufacturers to tweak their OEE calculations and future initiatives on a more granular, effective level. Facilities can embrace a spirit of continuous improvement by focusing on these small, ongoing changes.
OEE Is a Crucial Part of Industry 4.0
Industry 4.0 is inseparable from OEE metrics. Since it both raises the need for them and provides the means to improve them, manufacturers embracing Industry 4.0 can’t afford to overlook OEE calculations.
These steps will help manufacturers make the most of their Industry 4.0 investments. By capitalizing on these technologies, manufacturing facilities can push their OEE higher than ever before, helping them stay competitive in a rapidly advancing industry.
Comments (0)
This post does not have any comments. Be the first to leave a comment below.
Featured Product
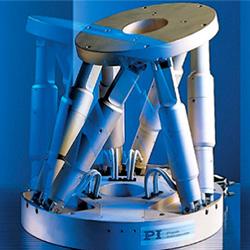