The Smart Move to More Efficient and Safer Maintenance Operations
Regardless of their size or the industry segment in which they operate, manufacturing companies are constantly striving to increase efficiencies within the various processes they employ. Arguably, maintenance is one of the primary areas in which companies are continually seeking ways to lower costs and cut the time taken to perform essential tasks. With many maintenance operations still planned and performed manually, often by experienced operators performing sometimes basic yet time-consuming tasks, it is easy to see how manufacturers are sometimes swimming against the tide when it comes to achieving efficiency goals.
In an effort to improve in this area, more and more companies are turning to innovative and disruptive technologies to streamline processes and reduce the time and costs involved within their maintenance operations.
One laborious yet highly important task is the need for maintenance engineers to manually check the torque level of every single bolt that might be in place within a particular piece of machinery, engine, or countless other structures or vehicles.
This has led to the emergence of certain solutions that are designed to eradicate the high level of time demanded in such instances. Examples of such solutions include those that use ultra-sonic waves to perform inspections. However, despite enabling accurate measurements, this method has plenty of critics, who point out certain fundamental limitations. Most notably, such devices require having physical access to the bolt, as the device needs to be plugged in on top of it. Ultra-sonic solutions also require information such as the length of the bolt, which might not be known or readily to hand.
A smarter approach to maintenance operations
From our own perspective, our ‘home ground’ of aerospace is one of the foremost vertical sectors in which maintenance, repair and operations (MRO) processes require efficient, as well as standardised, safe practices. So, as a go-to supplier and solutions provider solving key challenges for manufacturers within this space – as well as other industries, – we began looking at ways to address this fundamental issue a couple of years ago. For us, it was apparent that maintenance engineers needed something that would meet head-on the fundamental challenges within processes themselves, while also overcoming the shortcomings of existing solutions.
This has seen us develop a disruptive proof-of-concept solution called Smart Washer, a next generation sealing technology that enables touchless and wireless measurement of bolt axial load. Importantly, this means that instead of having to manually verify the torque level of every single traditional bolt, maintenance engineers are notified about those specific fasteners that are either too tight or too loose so they can attend to them accordingly in just a few seconds. This offers an added immediate benefit from a safety aspect as the device can reduce the eventuality of breakages in bolts caused by repeated over tightening during manual checks.
Designed to improve efficiencies within MRO, Smart Washer performs the fundamental role of a standard washer but uses intelligent connectivity to provide maintenance and service engineers with a clear picture of axial loads. This has been achieved by incorporating a proprietary strain gauge, as well as a transmission system into the washer, which via an accompanying reading device (Smart Reader), relays the information to maintenance engineers.
Quantifiable efficiency gains
Currently in beta testing across several customer sites, Smart Washer is already proving an invaluable asset. This is underscored by our customer, Airbus Helicopters, which has noticed quantifiable efficiency gains across helicopter engine maintenance. In this instance, a helicopter can require a periodic check that necessitates removal of its engines and interior trim even before maintenance engineers can gain access and check the bolts. Once checked, the engine needs to then be re-installed and a ground-run undertaken to ensure correct installation of the engines. Needless to say, this is a very labour-intensive process heavy maintenance operation that would typically take around two days and require two engineers to check about 12 bolts. Using Smart Washer, Airbus Helicopters has reported that they are able to perform the same task in about two hours and with one engineer.
Lifting off in other industries
Beyond aerospace and aeronautic industries, the disruptive Smart Washer technology could potentially address several other sectors that demand extremely high safety standards and efficient maintenance processes.
For example, we see opportunities in the energy and renewable resources markets. One such application scenario is with nuclear power, where nuclear energy companies could easily perform essential checks on radioactive waste tanks by using a drone from a safe distance. Similarly, manufacturers of wind engine turbines for power generation could leverage the benefits of Smart Washer in conjunction with a drone, saving time (and ultimately costs) as well as overcoming safety issues inherent with hard-to-access wind turbine blades. There are many other examples in which these fundamental issues can be addressed and overcome with this solution – including chair lifts and cable cars at ski resorts, or high-level rides at amusement parks.
Crunching data for predictive maintenance
When using such smart technology, there is a more far-reaching potential that has become evident. The amount and level of data provided by Smart Washer – that can be accessed, analysed and processed – could in due course enable accurate live monitoring and offer the opportunity to enjoy predictive maintenance. Parameters that could be registered include tension, date, location, temperature, to name a few.
This means that whether it’s an engine for an aircraft manufacturer, wind turbine, or amusement park ride, those companies could be alerted if there is a requirement to perform maintenance – be it for a sudden and immediate issue or just according to schedule.
Ultimately, most manufacturers or companies that are required to perform maintenance checks on machinery or other infrastructures set themselves clear goals when it comes to reducing time and cost across such processes. Thanks to innovative providers that commit to addressing and solving these fundamental challenges with smart technology solutions, such manufacturers will be well equipped in their constant quest to continually improve efficiencies.
JPB Système is a leading French manufacturer of efficiency-enhancing technology solutions for aerospace, aeronautic and other industries. The company serves some of the industry’s largest manufacturers with its industry 4.0-based process, including Safran, Pratt & Whitney, GE, Rolls-Royce and ITP Aero.
Comments (0)
This post does not have any comments. Be the first to leave a comment below.
Featured Product
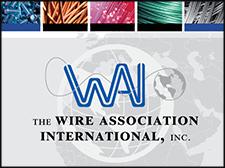