7 Improvements to Manufacturing Processes — and How They Affect the Bottom Line
Manufacturing is an increasingly competitive industry as new technologies unlock previously impossible standards. Investing in cutting-edge improvements to processes can lead to impressive results, but not every investment sees a significant or quick ROI in every case. Consequently, many manufacturers are hesitant to embrace new methods.
New technologies and processes must have a demonstrable impact on a company’s bottom line to make a convincing argument for adoption. In that spirit, here are seven recent manufacturing process improvements and how they affect profits.
Predictive Maintenance
Few technologies are growing as quickly among manufacturers today as the Internet of Things (IoT). These connected devices hold substantial potential, and one of their most helpful applications is predictive maintenance. In this practice, IoT devices monitor machine performance to predict when they’ll need upkeep.
As of 2018, 60% of surveyed manufacturers had concrete plans to implement continuous predictive maintenance monitoring. The same survey found that, on average, this method reduced upkeep costs by 12% and improved equipment uptime by 9%.
Other methods prevent costly breakdowns like predictive maintenance, but they may raise expenses through unnecessary repairs. This data-based approach ensures machines only receive the upkeep they need, so it reduces those costs. In a large facility, the resulting benefits will generate a positive ROI before long.
APS Software
Enterprise resource planning (ERP) and material requirement planning (MRP) software are staples of modern manufacturing. While these are helpful tools to employ, they also feature blindspots and weaknesses. Advanced planning and scheduling (APS) software provides a solution.
APS software takes information from ERP and MRP systems to produce long- and short-term insights to optimize production schedules. By consolidating data between these two systems, APS provides manufacturers the visibility to adjust their production to mitigate bottlenecks and adapt to changing demand. As a result, they can minimize waste and improve productivity.
The ROI for APS software will vary between different facilities, but it can be significant. Since many manufacturers already use ERP and MRP, they have the databases to maximize APS’s value. Adding one more software solution is a relatively low-cost way to capitalize on this information.
Additive Manufacturing
Many manufacturers struggle to eliminate waste because their methods produce it by design. Additive manufacturing, also called 3D printing, solves this issue by adding material instead of cutting it away. This technology wasn’t scalable to industrial production levels until relatively recently, but now it can substantially impact companies’ bottom lines.
3D printing is often faster than other manufacturing processes. A 2019 survey found that 70% of additive manufacturing users have seen a significant improvement in their lead times. Since it adds material instead of discarding it, the process can also eliminate waste-related expenses in its applications.
Additive manufacturing can also produce stronger products, leading to higher satisfaction and sales. For example, mil-spec buffer tubes, which are forged from a single aluminum piece instead of machined, have become an industry standard for their durability. Since additively manufactured parts are a cohesive unit, they’re stronger, which customers appreciate.
AI-Powered Demand Forecasting
Artificial intelligence (AI) is one of the most disruptive technologies available today. Manufacturers can implement it in multiple ways, with one of the most effective being AI-powered demand forecasting. Using predictive analytics to understand and react to incoming changes can help reduce waste and maximize sales.
Demand forecasting itself predates AI and is already standard practice for many manufacturers. However, introducing AI to this process yields significant improvements. According to McKinsey, AI-based approaches can reduce forecasting errors by 30%-50%, leading to a 65% reduction in lost sales.
It’s crucial to note here that, as with all machine learning applications, AI demand forecasting requires high-quality data. If manufacturers don’t have access to large pools of accurate, clean and contextualized information, their algorithms’ predictions won’t be correct.
Machine Vision Quality Control
Machine vision, another AI application, requires less data and can still produce substantial manufacturing process improvements. Perhaps the most cost-effective area to implement machine vision in manufacturing is quality control. Automating this step in the process can improve manufacturers’ bottom lines in a few key ways.
First, machine vision systems can spot defects faster than humans, eliminating bottlenecks that quality control typically creates. Second, they’re also typically more accurate than humans, letting fewer defects through. This reduces costs associated with returns and lost business. Over time, data from these systems reveals consistent quality issues, guiding manufacturers to remedy them and preventing waste from defects.
Heineken’s machine vision quality-control system exemplifies these benefits. The machine analyzes 22 bottles per second and produces data about common defects. These insights enabled the company to achieve a nearly 0% failure rate in this process.
Renewable Energy
Like additive manufacturing, renewable energy has been around for several years but has only recently become financially viable as a process improvement. While technologies such as wind and solar power typically come with higher upfront costs, they reduce expenses over time. Most of those savings arise from energy independence.
Renewables let manufacturers decrease their reliance on electrical grids, even becoming completely independent of them. Consequently, their energy bills decline or even disappear since they’re no longer reliant on another entity for power. As sustainability becomes increasingly important to consumers, renewables can further improve manufacturing bottom lines by increasing sales.
Customers today want to invest in sustainability. Take the Tesla Cybertruck, which saw more than 250,000 preorders within a month of its reveal. The uptick in sales from consumers who want to order from green manufacturers will push companies well beyond their bottom line.
5G Connectivity
The newest process improvement on this list, 5G connectivity, is still in its infancy but holds potential. These networks promise speeds up to 25 times faster than 4G LTE, near-zero lag and far more bandwidth. This means manufacturers can host more interconnected IoT devices on a network without fear of slowing down.
While 5G networks for consumers may take several years to fulfill their promises, manufacturers are already experiencing the benefits. Ericsson built a 5G-powered smart factory in Texas to impressive results. The facility has real-time location data on virtually every asset, decreasing loss through higher transparency.
In the U.K., Worcester Bosch used 5G to enable mobile edge computing in its facility. Not long after implementation, the manufacturer experienced a 2% boost in output through optimized machine performance. On a larger scale, those increases could total substantial savings.
Optimize Your Manufacturing Processes
Today’s technology has provided manufacturers with many possible routes to process improvement. These seven methods represent some of the most cutting-edge and cost-effective advancements, but they’re just a fraction of the existing options. Manufacturers can surge past their bottom line by capitalizing on modern technology and taking a slow, careful approach to implementation.
Comments (0)
This post does not have any comments. Be the first to leave a comment below.
Featured Product
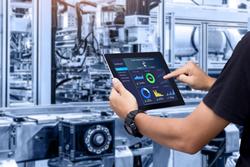