The Earth’s environment is in code-red status, but new digital solutions can meet the challenge.
By making industrial plants more adaptive, AI can help save the planet. Really.
You have heard the statistics again-and-again. Greenhouse gas concentrations are at their highest levels in 3 million years and continue to rise. The planet is now 1.2°C warmer than it was in the late 1800s. The last decade was the warmest on record. Conservation and renewable energy can help. But, no matter how green the Scandinavian countries and others go, they will not save the planet. Their efforts are just not going to be enough.
There is no silver bullet. New digital solutions can help us meet the challenge, though. With fossil fuel production to decline by roughly 6% per year between 2021 and 2030, for example, imagine if we could achieve a 6% reduction in emissions from every power, oil and gas, glass, chemical, cement and aluminum plant on the planet. AI can do this. How?
Plants are designed to operate within a certain range for optimal efficiency. They are supposed to minimize fuel burn and emissions release of NOx, SOx, methane, etc. Unfortunately, however, no battle plan survives the first contact with the enemy. The same is true in a plant. Plants run at a broad range of variabilities that typically are less than optimal.
Plant controller systems based on static models are not responsive enough to adapt to changes and prescribe actions to insure optimal outcomes. As a result, set points are adjusted every now and then by operators who hunt for good conditions. This routine opens up tremendous opportunities for improvement that only AI can bring through multivariate analysis of current operating conditions and constant open and closed loop triggers that keep plants running at maximum efficiency while using less energy and producing less pollutants.
By harnessing the huge amount of information coming from sensors in plants and equipment, AI-based optimizers sitting on top of plant controllers can turn tens of thousands of plants around the world into “adaptive” facilities that consistently produce high throughput, maximize yield, lower energy usage, lower emissions, and minimize waste of precious resources like water.
Ageing equipment also significantly impacts energy consumption and environmental performance. AI-driven predictive models can assess machine health over time, provide real-time monitoring and prescriptions, and recommend predictive maintenance for furnaces, compressors, pumps, and forming machines.
The opportunities for AI-based optimizers to keep plants running at their best – “as designed” – are many:
- Air is major amount of contribution of thermal NOx (78% of air is nitrogen); excess air leads to more NOx; lesser air (lean air) leads to CO and methane, which is more potent than CO2.
- Combustion control is important to lower emissions of NOx, CO2, methane, SOx. Beyond combustion control, pre-treatment of fuel (desulfurization to remove sulfur to reduce SOx) and post-treatment of flue-stack gas can have an enormous positive impact.
- Water conservation through optimal water usage, including water recycling, zero liquid discharge, and removing mercury, metal, arsenic and other pollutants.
- The list goes on and on.
We have seen the impact of AI-driven models that deliver sustainability wins across the board.
One recent example we can cite is from a large gold mine where we deployed an online AI model to complement the legacy advanced plant control systems at its grinding circuit. We optimized production, achieving net savings on a sustainable daily basis that included over a million liters of water – enough for a small town – and energy reduction of 4 million electricity units while increasing production throughput of more than 1% for $3 million of top-line growth on a yearly basis.
Another example is in ammonia production from the petrochemical industry. Ammonia making is a complex process involving high pressures and temperatures. Most times operations remain steady but can behave erratically, especially with changing upstream feedstock and unseen dynamics in the plant. In one of the plants where we had deployed our AI-based optimizers, frequent CO2 spike conditions would trip the plant to avoid damage to the expensive catalyst beds. Each downtime would cost $1 million a day in lost production.
AI-models solved the problem by running system-level prognostics that fed hundreds of measurements into multi-variate models to capture deviations early and nip problems in the bud. CO2 was kept below threshold limits with no downtime incurred.
Sustainability goals are not different or distinct from plant goals. They are both ways to run operations in an efficient manner, day in and day out.
I have no doubt that less than 1% of the plants and the world take advantage of the opportunities that AI-based real-time/near real-time adjustments in plant operations can bring. Is it the fault of the people sitting in the control rooms of these plants? Not at all. They are fighting fires every day and are just not armed with the technologies they need. In a recent global sustainability survey conducted by my company, 52% of respondents said that sustainability is a top corporate initiative but is in its early stages in their organizations. The top reasons why AI has not been utilized were a lack of knowledgeable staff to implement the technology (42%) and lack of good data (20%).
AI tools that can be easily integrated into plants and deliver actionable insights are now here, however. Let’s double-down on our priorities. Industrial CEOs, it’s time to save the planet.
Dominic Gallello is Chief Executive Officer of Symphony IndustrialAI.
Comments (0)
This post does not have any comments. Be the first to leave a comment below.
Featured Product
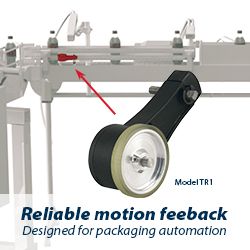