How Manufacturers Can Deal With Supply Chain Issues and Still Grow
Supply chains have been a pain point for manufacturers in the past few years. While many products face rising demand, supplier shortages, shipping delays, and similar disruptions have paused growth for many manufacturers.
New orders hit a 16-month low in October 2021, according to the Institute for Supply Management (ISM). Similarly, 26 commodities were in short supply, some for more than a year. However, despite these setbacks, manufacturers still have a chance to grow.
Here’s how manufacturers can overcome supply chain issues and drive growth.
Diversify Sources
The first step to growing amid supply chain issues is moving past the single-source model. While the lean practice of relying on a single supplier cuts costs, it leads to considerable ripple effects whenever a disruption occurs with that supplier. In contrast, if a facility has multiple sources they can pull from, delays and shortages won’t be as impactful.
This diversification should apply to shipping ports as well. Los Angeles and Long Beach alone account for more than 25% of North American ocean freight, so any delays there will create massive domino effects. However, if you have an alternative port you can use, heavy traffic and delays there won’t affect you as much.
While restructuring the supply chain, consider reshoring and near-shoring, as shorter travel distances will help further reduce delays. Keep in mind that these fixes may not deliver immediate results, but they will mitigate future disruptions.
Ensure Quick and Effective Communication
Manufacturers must also improve their communication to enable growth despite supply chain disruptions. As the past two years have proved, unexpected circumstances can quickly grow out of control. Organizations must be able to adapt to changing situations to prevent disruption, and that requires efficient communication.
Real-time contact with suppliers and shipping partners can reveal incoming challenges sooner, enabling faster, more effective reactions. Similarly, communication between departments improves products as manufacturers adapt to changing supply and demand. The faster and more clearly different teams can communicate, the more cohesive a manufacturer’s recovery and growth efforts will be.
Manage Customer Demand
As supply chain issues continue, manufacturers struggle to meet demand, limiting their growth. One way to move past this obstacle sooner is to reshape demand on your own. While it may seem strange, some strategies can help influence buyer behavior to suit your current situation.
The most straightforward way to do this is to adjust prices to reflect the current supply. If components of one item are delayed or in short supply while others are abundant, raise the prices of the former or lower the cost of the latter. Customers will naturally drift toward the lower-cost option, driving up revenue despite ongoing supply challenges.
Allocating supply according to urgency can also help. Auctioning and product dilution may also work, but these options can generate negative customer attitudes in some situations, so you should consider them carefully before embracing them.
Embrace Technology
Finally, manufacturers should implement new technologies to help optimize their resource use. For example, internet of things (IoT) sensors can maximize visibility throughout the supply chain and optimize facility resource consumption, informing faster, smarter responses. As a bonus, the resulting efficiency reduces costs and waste, raising profits.
Similarly, warehouse management systems and demand forecasting algorithms can help influence more effective adaptations. While these technologies may come with high upfront costs, they’ll let manufacturers understand developing situations and possible mitigation strategies. As a result, they can drive growth while challenges continue.
Manufacturing Growth Is Challenging but Not Impossible
While the manufacturing industry faces substantial obstacles, none are too large to overcome. These four steps can help manufacturers mitigate ongoing supply chain issues and grow in 2022 and beyond.
Every company has unique challenges and opportunities, but these mitigation strategies can apply to any situation. If manufacturers can implement these steps successfully, they can grow while the rest of the industry struggles.
Comments (0)
This post does not have any comments. Be the first to leave a comment below.
Featured Product
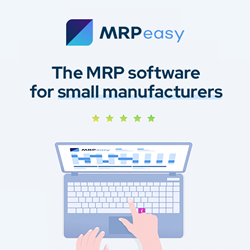