Keys to Building More Autonomous Systems Into Manufacturing
Autonomous manufacturing in its current form may be relatively new, but we’ve been using machines and systems to automate our work for decades. The idea is to create a more agile and effective network while reducing labor costs and operating expenses.
In today’s landscape, this is achieved through advanced technologies like the IoT, artificial intelligence, machine learning, and beyond. Both autonomous manufacturing and hybrid autonomous manufacturing introduce a level of automation never seen before. The system does all the work, with machines and technology as a strong foundation, and people are relegated to monitoring and support.
It doesn’t mean people are replaced – quite the opposite. Manual laborers are empowered thanks to autonomous manufacturing techniques, with most of the rote and repetitive tasks reserved for the system. This frees people to use their talents elsewhere.
Breaking Down Autonomous Manufacturing
At its simplest, autonomous manufacturing is a form of manufacturing and industrial operation that is fully supported by automated technologies. But when you dig a little deeper, the concept is much more complex.
Flexibility Through Agility
Agile or lean manufacturing is not new and is an incredibly lucrative paradigm in the field. By reducing waste, bottlenecks, and associated costs, you’re vastly improving output and boosting value.
More importantly, you gain critical flexibility that affords the system better adaptability. You and your team can better react to what’s happening in the market and with the supply chain. The latter is increasingly important these days, with the pandemic, supply problems, worker shortages, and more.
Safer Working Conditions
These days, there’s absolutely no reason why manual workers should be subjected to dangerous conditions, hazardous environments, and potentially harmful tasks. Advanced machines can take over to keep workers safe, healthy, and more satisfied.
New Opportunities
An autonomous manufacturing system is supported by intelligent, data-driven technologies. The data these systems collect on a regular basis can be fed back into the entire process after extracting practical insights to improve operations continually. It creates a persistent cycle of evolution as manufacturers look for newer and better ways to produce and deliver.
Mass Customization
For years, manufacturing has followed a more rigid timeline, with products designed and vetted before hitting the production line. After, the finished product is set in stone, so to speak, with only minor adjustments or revisions made. Thanks to a bevy of new technologies – primarily additive manufacturing – it’s now possible to deliver highly personalized products to consumers at scale.
Everything on Autopilot
Traditionally, only certain tasks or processes could be automated, and most were repetitive, easily replicable projects. Now, everything can be put on autopilot thanks to software-based automation. Everything from nuanced management down to the assembly line can be automated successfully. Importantly, it’s also getting more accessible than ever, regardless of budget and operation size.
Building an Autonomous System
This is not just about automating select processes and improving efficiency here and there. Autonomous manufacturing is transformative and revolutionary, stretching into an entirely new realm. One could even say it’s the next generation beyond Industry 4.0.
That said, building an autonomous manufacturing system is no small feat, and it’s not going to happen overnight. Foundationally, it involves updating and improving nearly every facet of an operation, starting with outdated equipment and processes and moving from there. If Industry 4.0 was about gaining more effective insights and understanding the operation better through smart technologies, then autonomous manufacturing is about putting that data to work.
First, you’ll need to document every project, process, or operation to better understand what can be automated, what can be supported with automated technologies, and what must be carried out manually.
From there, consider the equipment and hardware at your disposal. What needs to be replaced, or what can be upgraded? Advanced autonomy requires ongoing online access, which could include upgrading the hardware (opting for physically connected systems) or installing new IoT sensors to facilitate the data handoff.
Nothing is off-limits here. You should look into boosting steam boiler efficiency, if they’re used in your facilities, by adding insulation, balancing combustion air, and scheduling professional maintenance, itself powered by proactive maintenance through smart data solutions.
You might also consider upgrading machining tools, assembly hardware, conveyors, and just about everything used within your facility.
Artificial Intelligence Is the Key
Artificial intelligence and machine learning is the key to a truly autonomous system. Deep learning and neural networks have the capacity to ingest, process, and act upon various datasets, making intelligent decisions to support the entire operation.
For example, they can assess current inventories and order new supplies when running low or when availability drops below a certain threshold. They can also stop operations when a problem or event is detected, scale up or down assembly lines to meet shifting demands, send out alerts – like when machines need maintenance or performance drops – and much more.
It’s essentially like handing the reins over to an AI, except it’s not reckless or risky because the systems and data are there to support nearly every possibility. What’s more, there are still professionals at the ready to support and assist the technologies.
A 2020 MIT survey revealed that about 60% of manufacturers are already using AI to improve product quality, achieve greater speed and visibility across the supply chain, and optimize inventory management. The next logical step is introducing AI and machine learning into more of the operation – thereby empowering autonomous manufacturing.
Comments (0)
This post does not have any comments. Be the first to leave a comment below.
Featured Product
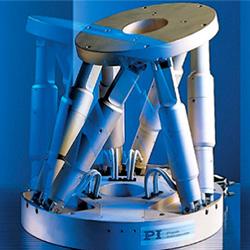