7 Critical Flaws in the Manufacturing Supply Chain and How to Correct Them
Supply chain issues have affected virtually every industry over the past few years. However, manufacturers have felt the impact of these challenges more than most. While just 38.8% of all small businesses have experienced supplier delays in a U.S. Census Bureau survey, 64.6% of manufacturers have.
The manufacturing sector seems to be experiencing delays and disruptions far more than other industries. Part of this is because of others’ reliance on it, and another reason is the commonality of critical flaws within supply chains. Here are seven of these issues and how manufacturers can correct them.
1.Organizational Complexity
A 2021 study found complexity to be the most significant driver of supply chain vulnerability. Manufacturing supply chains involve many steps where information, products and materials must pass through multiple hands. These complicated networks make it difficult to track and respond to disruptions quickly.
Product complexity plays a role in these delays, but process complexity is a more significant factor. Manufacturers should make their supply chain operations as streamlined as possible, which begins with data collection. Implementing Internet of Things (IoT) devices to gather data and create digital twins will help model various scenarios.
Manufacturers can simulate changes with a digital twin of their supply chain processes. They can then find which adjustments result in the most streamlining, reducing complexity. Companies can then apply these changes in the real world with minimal risk.
2.Fragmentation
A similar issue is supply chain fragmentation. Manufacturers have become increasingly reliant on third-party firms to produce specialized components. For example, the need for internal computer parts has risen as more automakers have pursued electrification. The recent semiconductor shortage reveals how this reliance can make it difficult to understand and adapt to changes.
Manufacturers should aim to become less fragmented long term, but that shift could take years. In the meantime, they can mitigate the impact of fragmentation by addressing individual firms’ inventory requirements. While it may seem counterintuitive, studies show that prescribing company-specific inventory sizes is more effective at mitigating risk than making requirements the same across all parties.
Manufacturers should also increase communication between third parties. They should take care of more processes internally as they gain the necessary funds and opportunities.
3.Lack of Inventory Visibility
Many manufacturers also lack visibility in their inventory levels. Only 6% of companies before the pandemic reported having full supply chain visibility, and 46% relied on manual methods for inventory tracking or didn’t track it at all. This lack of transparency leads to surpluses and shortages from over- and under-ordering amid demand shifts.
The key to improving inventory visibility is moving away from manual systems. Manufacturers must employ RFID tags or IoT trackers to provide real-time location data for all parts and products in their inventory. Feeding this information into a warehouse management system (WMS) will help stay on top of it.
WMS solutions can alert manufacturers about changing needs and reveal seasonal trends. They can then adapt their supply chain accordingly to avoid inventory-related wastes.
4.Lack of Transportation Visibility
Similarly, many manufacturing supply chains lack visibility into their transportation. Recent disruptions have highlighted this flaw, as companies left containers in the wrong locations and overly congested ports, which resulted in shipments taking 20% longer. Once again, the solution lies in real-time tracking technologies.
Telematics systems and IoT trackers in shipments can provide real-time information about shipment locations, quality and any influencing factors like traffic. Supply chains can then use this data to inform strategic changes, like shipping to another port to avoid congestion or taking another route for a safer delivery.
Telematics can also monitor driver performance metrics to help them become more efficient and lower insurance rates. Over time, this data can also reveal trends manufacturers can use to set benchmarks or future goals.
5.Dependence on Single Sources
Just-in-time manufacturing has been the dominant business model for years, but the pandemic quickly revealed its weaknesses. One of the most significant flaws of this model is its dependence on single suppliers. It reduces costs but creates massive disruptions when a supplier suddenly becomes unavailable or unreliable because of local or geopolitical issues.
Rising fuel costs from the U.S.’s dependence on Russian oil during the Ukraine crisis and early pandemic shutdowns in China highlight these risks. Manufacturers can prevent these disruptions by embracing distributed sourcing. Multiple smaller, geographically dispersed suppliers can ensure issues in one area won’t jeopardize the entire supply chain.
Of course, manufacturers can lean too heavily into distribution. Too many sources will increase complexity and raise costs too high. Manufacturers should aim to have a few suppliers but avoid a vast network.
6.International Dependency
Manufacturers should also look for sources closer to production when addressing their suppliers. Dependency on international companies and other third parties increases vulnerability to geopolitical and area-specific disruptions. For example, reliance on Chinese suppliers led to significant PPE supply shortages early in the pandemic.
Distributed sourcing helps, but manufacturers must also embrace domestic sourcing. Reshoring and near-shoring will make it easier to react to disruptions, as the trends that affect these suppliers will likely impact production, too. This even ground reveals incoming challenges faster.
Domestic sourcing also reduces transportation times and costs. As a result, manufacturers can adapt faster when a disruption arises. These savings will help offset the higher upfront costs of moving away from international dependencies.
7.Cyber Vulnerability
Manufacturers must address their cyber vulnerabilities. Supply chains are among the most vulnerable targets for cyberattacks due to increasing IoT connectivity. These attacks rose by 42% in the first quarter of 2021 alone, affecting 137 organizations and 7 million people.
The first step in addressing supply chain cyber vulnerabilities is securing IoT devices. Supply chains segment networks to keep items and data separate, so no one endpoint can grant access to the entire system. Manufacturers must also update these gadgets regularly and encrypt all their data transmissions.
Addressing third-party risks is also crucial. Manufacturers should only partner with companies that can prove they have robust security measures, such as meeting industry cybersecurity standards. Even then, manufacturers should limit third parties’ access privileges, not granting them anything more than they need to minimize potential damage in a breach.
Manufacturing Supply Chains Must Improve
Manufacturing fuels many other industries, and supply chains fuel manufacturing. The widespread disruptions of the past few years highlight how flawed these networks are, but companies can take this as an opportunity to improve. The industry should adapt to prevent similar situations in the future as it recovers from recent delays.
These seven flaws are among the most common and critical to address. Manufacturers that move past these vulnerabilities will emerge more efficient and resilient than ever.
Comments (0)
This post does not have any comments. Be the first to leave a comment below.
Featured Product
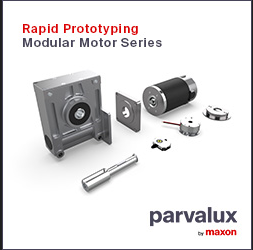