8 Causes of Lost Productivity in Manufacturing and How Managers Can Address Them in 2022
Maximizing productivity is a critical goal for every manufacturer. However, many companies may not realize this is an ongoing process, not a one-time adjustment, as there is always room to improve.
Addressing lost productivity is particularly critical in today’s climate. Despite technological advancements and economic growth, manufacturing productivity has declined since 2010, likely for the first period in American history. Manufacturers must find where they’re losing efficiency to reverse this trend.
Here are eight common causes of lost productivity in manufacturing and how managers can address them.
1. Equipment Failure
One of the most common productivity blocks in this industry is mechanical failure. Unplanned equipment downtime costs manufacturers $50 billion each year when factoring repair costs and lost production time. Regular maintenance schedules can help prevent these scenarios, but predictive maintenance is more effective.
Predictive maintenance uses Internet of Things (IoT) sensors to determine when equipment will need repair. While there may not be any outwardly noticeable warning signs of wear before failure, there are often internal signals. Predictive maintenance analyzes those conditions to produce a more accurate picture of equipment health.
Studies show that preventive maintenance can reduce unplanned downtime by up to 20% in some scenarios. It can also reduce maintenance costs by up to 10%, minimizing the overall impact of this downtime.
2. Planned Downtime
While unplanned equipment downtime is more costly, even planned breaks limits productivity. In many cases, manufacturers take more downtime than necessary, creating a gap where they could be more productive. Once again, predictive maintenance can help.
Traditional, schedule-based preventive maintenance prevents failure, often resulting in unnecessary repairs. Machines rarely degrade according to a consistent schedule, so schedule-based fixes are prone to create unwarranted stops.
With predictive maintenance, workers only repair equipment when needed, eliminating this downtime. Removing these stops results in savings of 8%-10% compared to preventive care.
3. Injuries and Illness
Employee injuries and illnesses also limit manufacturing productivity. In 2020 alone, the manufacturing industry experienced more than 135 injuries and illnesses that resulted in days away from work. Even if each of those only represented one missed workday, that’s still more than one-third of the work year.
The most effective way to prevent workplace injuries is to remove employees from the hazard entirely. Automating the most dangerous tasks will ensure workers maintain a safe distance from processes that could harm them. More thorough training can also help, especially on correct techniques to prevent repetitive strain injuries.
IoT trackers can help improve transparency and communication to mitigate injuries, too. Smart textiles can measure heart rates and other vitals to alert workers when they’re in danger of overexertion or similar conditions. They can then take a break to avoid an incident.
4. Burnout
Emotional factors also play a significant role in workers’ productivity. On-the-job stress costs the U.S. more than $500 billion and 550 million lost workdays every year. While factors in workers’ personal lives play into this, it’s largely an issue of workplace environments.
One of the best ways to reduce burnout is to create a less stressful workplace. Using automation to alleviate workloads, encouraging employees to use their vacation days, enabling a comfortable work-life balance and practicing open communication can all help. Being proactive about looking for and addressing social conflicts between workers is also important.
Employees are also less likely to feel burned out if managers recognize their hard work. Public recognition for high performance, competitive salaries, more paid time off, and other rewards can engage workers and prevent burnout.
5. Substance Abuse
Another factor in employees’ lives that could hinder productivity is substance abuse. This could lead to declining performance, tardiness and even workplace intoxication.
Manufacturers should watch for signs of substance abuse in their workforce. Histories of trauma can increase the risk of abuse, so managers may need to pay closer attention to employees after a traumatic event. If they notice someone struggling with these issues, they should gather evidence then confront them privately with HR.
It’s also important to create a positive environment to prevent and mitigate substance abuse. Providing mental health and addiction resources to employees could encourage them to seek help.
6. Product Defects
Some productivity blockers don’t seem substantial at first but can accumulate to have a considerable impact. While individual defects don’t appear to use much time, each one means manufacturers have to produce another product to replace it. Over time, that can result in a substantial time loss.
Defects can come from many areas, so manufacturers need to take several steps to prevent them. First, they should train their employees thoroughly and reduce repetitive tasks where possible to minimize human error. Keeping a close eye on machine maintenance will help prevent equipment-related defects.
Variation is another common cause of product defects. Manufacturers should simplify lines to limit the product types each one produces and use consistent machinery to minimize places where mistakes can arise.
7. Logistics Challenges
Some manufacturing productivity losses come from outside the manufacturing plant. Supply chain delays and disruptions can result in shortages, surpluses and late arrivals, throwing production out of balance. The key to resolving these issues is improving visibility.
Most companies have to respond to unexpected changes on a weekly or daily basis. Manufacturers that can see these issues arising earlier have more time to adjust appropriately. Technologies like IoT tracking and predictive analytics provide that transparency.
Real-time data from IoT trackers throughout the supply chain can reveal mounting challenges and potential delays. Predictive analytics can then interpret that information to produce insights for the future. Manufacturers should take advantage of these technologies to stay agile and respond to incoming changes, such as slowing production amid incoming delays.
8. Poor Organization
Poor organization can also hinder transparency within the manufacturing facility. Workers may spend more time finding what they need, and production lines may be needlessly long or complicated. These factors can be highly disruptive, but they’re easy to fix.
Once again, visibility is key. IoT trackers like RFID tags can provide real-time data about every product and part’s location, minimizing searching time. Feeding this information into a warehouse management system (WMS) can highlight high-traffic areas to inform workflow improvements.
Often-picked items should reside as close to their destination as possible to minimize transportation. Similarly, these should be easy to grab. Manufacturers can also use workflow data to create digital twins and model various workflow changes to find the most efficient alternative.
Minimizes Stops and Maximize Productivity in 2022
These eight factors are some of the most common and disruptive causes of lost productivity in manufacturing today. Manufacturers that know what they face and how to address it can move past industry wide roadblocks. They can then become as agile as possible, helping move ahead in this increasingly competitive industry.
Comments (0)
This post does not have any comments. Be the first to leave a comment below.
Featured Product
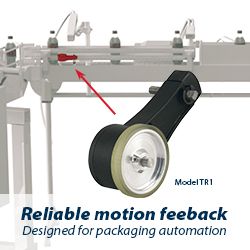