The affordable way to upgrade to a smart factory - Retrofitting legacy equipment
According to the Sprinting to Value in Industry 4.0 report, 53 percent of plant managers surveyed said adopting Industry 4.0 is a concern, with only one in four seeing financial opportunities from these advances. However, businesses must take advantage of Industry 4.0 and the Industrial Internet of Things (IIoT) technologies. Here, Claudia Jarrett, US country manager at industrial parts supplier EU Automation, offers three top tips for combining new technology with legacy equipment.
It is commonplace for decades-old industrial equipment to be at the heart of today’s operations on the factory floor. However, these machines lack the connectivity capability necessary to fully harness the potential of Industry 4.0 and the IIoT. For example, old equipment that communicates via proprietary protocols using serial cables is not suited to remote monitoring across the Internet Protocol Suite, commonly known as the TCP/IP.
Furthermore, SMEs also have lower spending power than multinationals, so creating a smart factory isn’t as simple as just replacing old machines with new ones. The dilemma facing plant managers is that if a machine is still in full working order and performs adequately, they cannot justify the cost of replacing large industrial machines with newer models.
Here's three top tips on how to overcome this dilemma.
Retrofitting the old with the new
Legacy equipment wasn’t designed for a smart factory, with mass machine-to-machine communication. But that doesn’t mean that it’s impossible to achieve that level of communication without replacing all your machines and equipment. Instead, the communication capability required can be added to your existing equipment by retrofitting it with compatible smart technology.
The ABB Ability Smart Sensor for Motors is just one example of smart technology that can be retrofitted to legacy equipment. The sensor monitors, and reports on, motor performance data. Furthermore, by using the web portal, users receive status updates and maintenance recommendations which enable engineers to plan maintenance schedules more efficiently.
Smart sensors retrofitted to legacy equipment in this way can be used to monitor machine parameters like temperature, pressure and vibrations, allowing the data to be recorded and transmitted across the factory network. This helps plant managers and engineers to implement a predictive maintenance strategy because, if a smart sensor detects a problem with a machine’s component, replacement parts can be ordered from a reliable parts supplier before any unplanned machine downtime occurs.
By combining tried and trusted legacy equipment with emerging smart technologies, SMEs can attain the goal of creating a smart factory without the financial burden of replacing all their machines and equipment. Not only that, but upgrading industrial machines, rather than replacing them, is often the more environmentally-friendly approach to upgrading a factory.
One at a time
However, manufacturers should automate one process at a time when adding new technology to machinery. When used in combination, many new manufacturing technologies can automate and streamline operations from top to bottom. There are several key technological options available for manufacturers, but these changes should be made incrementally, rather than all at once.
Simply put, trying to upgrade processes at once will likely be overwhelming and can therefore lead to severe problems. Unfortunately, there is no universal methodology for the introduction of IIoT. The implementation of factory automation requires valuable input from several departments, with the plant manager needing to consider the factors related to facilities and equipment.
For example, start by identifying tasks that take a considerable amount of time to perform, or involve parts that are too difficult to inspect or process without automation. Alternatively, plant managers can also automate tasks that often fail to meet quality standards or result in a high waste rate — and go from there.
Provide training
While implementing new manufacturing technologies is beneficial, it also involves a learning curve. This applies to the workers who will have to adjust to processes that use new technologies. Before adding or changing your technology, ensure you provide training to employees and explain the technology’s role and value. Here, employees will realize how the processes improve and change their responsibility.
From the training sessions created, a curriculum would also be beneficial. Many vendors offer standardized training, which is a good start. When receiving vendor training, ask questions and leverage their expertise. Likewise, record training sessions to create video and audio presentations and training documents, after all employees learn new technologies in many ways so it is imperative to cover all bases. Multiple training methods also help to ensure that each employee can learn how they find most useful, which in turn gets new employees on board quickly and more effectively.
Technology innovates rapidly, and manufacturers must embrace it to remain competitive. However, this does not require SMEs to break the bank. Instead, manufacturers can affordably take advantage of Industry 4.0 and the IIoT by training employees accordingly and combining new technology and legacy equipment — one machine at a time.
For additional resources to help streamline and integrate manufacturing technology, contact a reliable parts supplier, like EU Automation. Its industry-leading experts have valuable experience in offering affordable options to start your IIoT journey, including new parts for older processes across several industries.
To find out more about retrofitting legacy equipment with smart technology, and to order new, reconditioned or obsolete parts, visit www.euautomation.com.
Comments (0)
This post does not have any comments. Be the first to leave a comment below.
Featured Product
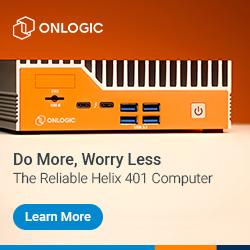