3 Ways Digital Transformation Is Changing the Industrial Sector for the Better
Digital transformation in industry is continuing at a rapid pace, even in an uncertain market. These solutions and Industry 4.0 technology enable businesses to take full advantage of the data they collect by streamlining work, reducing the risk of error and enabling new manufacturing strategies.
New digital initiatives are helping manufacturers transform their businesses in a few different ways. Here are three points to consider as industry digital transformation makes its mark on the industrial sector.
1. Streamlining Monitoring, Testing and Management With Digital Twins
Internet of Things technology allows manufacturers to capture vast amounts of real-time data on everything from factory operations to the performance of individual machines.
However, making this information accessible and human-readable can be a significant challenge, especially as IoT data-gathering solutions scale. A single manufacturer may manage hundreds of thousands of individual IoT sensors that regularly generate new, potentially important data points.
Digital twins help provide essential context to the information that businesses are gathering.
A digital twin is a high-fidelity model of a facility, machine, component or other object that aims to represent its real-world equivalent in as much detail as possible. It comes as close to a digital copy of the original as it can.
Creating a digital twin of an existing object makes organizing data on that object much easier. Suppose a certain characteristic varies significantly throughout the facility. In that case, the air quality is much better in one spot than another or there are significant temperature variations near specific kinds of equipment — patterns will be much easier to spot.
A digital twin can also make it easier to track daily operations. A warehouse or similar facility’s twin is fully searchable, enabling managers to quickly navigate the model, isolate particular elements or identify problem areas.
A digital twin can also help businesses test and simulate a product, facility or machine before it even exists.
Design data can create a digital twin that can be tested using various simulation tools. For example, a team can use a twin to model the traffic flow in a potential warehouse layout or heat tolerance in a proposed piece of foundry equipment.
Information from these simulations can help designers catch oversights or missed opportunities before construction, production or development begins — reducing the chance that errors make it past the design phase.
2. Improving Data Availability and Mitigating Silos With Integration in Industry Digital Transformation
Thanks to digital transformation in industry, data and analytics are some of the most valuable resources businesses have at their disposal. Today, leaders are able to gather insights across multiple data source and they can use this information to grow and expand their business.
However, this information is only useful if the right employees can access it. Important data trapped in silos available to only certain departments or employees becomes less valuable to the entire organization.
For example, data produced within or captured by a CRM platform, supply chain management tool, IoT platform, product report or similar resource may remain trapped there and be meaningless to many employees.
Industry digital transformation often comes with data integration — tools, platforms and practices that help improve visibility and accessibility across a company.
Data integration means connecting various physical and digital systems so they can easily exchange information. In many cases, this integration will be the first time certain things are connected to the web and digital networks, allowing data to be accessed remotely.
Information captured by a supply chain management system or IoT monitoring platform will be made available to a businesswide system like an ERP, allowing these high-level systems to take full advantage of data captured throughout the organization and its facilities.
Integrating data management solutions like an ERP, MES, CRM and similar tools can also help a business ensure critical information is available to as many employees and stakeholders as possible. This means anyone who may want to use the data will have it available.
3. Reducing Downtime and Cutting Maintenance Costs With Artificial Intelligence and Predictive Maintenance
The large datasets businesses create can be unwieldy and difficult to analyze, even with powerful data visualization tools. As a result, these businesses may not be getting the full value out of the information they collect, and valuable insights may be left behind.
Big data analytics, coupled with technology like artificial intelligence (AI), can help analyze datasets that are too large for human analysts to handle on their own. These solutions can uncover subtle patterns and correlations in vast datasets, assisting businesses in extracting more value.
One emerging use case for AI and real-time analytics is predictive maintenance — algorithms that can use data from monitors to predict when equipment will need upkeep or risk failure. A predictive algorithm can alert technicians the instant it detects signs of future problems or potential maintenance issues by continuously analyzing current data from machine sensors.
The technicians can respond immediately, potentially allowing them to prevent downtime or fix issues that may have been passed over if they relied on a preventive maintenance schedule.
The specific benefits of predictive maintenance vary among businesses and use-cases. According to the U.S. Department of Energy, the average company that adopts predictive over preventive care will save 8%-12% on energy costs and reduce downtime by as much as 35%-45%.
Other use-cases for AI and big data analytics include demand forecasting and production management optimization.
These algorithmic systems can provide benefits similar to a predictive maintenance system — optimizing existing workflows and ensuring businesses aren’t caught off-guard by future work or market conditions.
Digital Transformation in Industry Helps Streamline Critical Work
Digital transformation in industry is making mission-critical work much easier in various industries. This change will likely transform the industrial sector for many years to come.
Data integration, digital twins and AI analytics are three examples of solutions driving change in industry right now. These technologies help make information more accessible, improve analysis and increase the value businesses can extract from the data they collect.
Data will likely become more important to many sectors over the next few years. Industry digital transformation is likely to increase in relevance by helping businesses take full advantage of the information they collect and generate.
Comments (1)
Featured Product
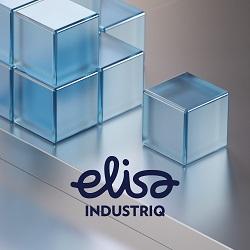