Sanitation Challenges Modern Manufacturers Face (and How to Fix Them)
The Abbott Labs formula contamination scandal has many manufacturers reassessing their sanitation practices. To clean up a manufacturing plant, it is important to go above and beyond the call of duty. That way, a manufacturer can identify and address sanitation issues in their early stages.
There are several common sanitation challenges that modern manufacturers face. These include:
1. Product Contamination
Dust and particles can contaminate a manufacturing plant. Contamination can affect manufacturing processes and systems. In these instances, a plant can inadvertently produce and shift contaminated products to customers.
Teach employees about contamination and the dangers associated with it. Workers must understand how to keep a manufacturing plant clean and protect against contamination. With proper training, workers are well-equipped to do just that.
2. Labor Shortage
The Great Resignation is making it difficult for manufacturers to find quality job candidates. It is forcing manufacturers to hire inexperienced workers in the hopes of quickly filling job vacancies. Yet these workers may lack sufficient sanitation training, resulting in a widening skills gap.
Bring new workers up to speed on sanitation best practices. New hires should receive training on these practices in their first days on the job. Also, they should receive ongoing training to stay up to date on best practices for sanitation.
3. Failure to Follow Sanitized Standard Operating Procedures (SSOPs)
SSOPs define how manufacturing employees should clean and sanitize equipment. They must be followed every day. Otherwise, failure to follow SSOPs can lead to contamination.
Create SSOPs and maintain them over time. An SSOP should be shared with employees. It can be reviewed and updated periodically.
4. Inconsistent Cleaning
A manufacturing plant requires consistent cleaning. When cleaning is performed, it must be done to the highest standards. If the cleaning is not completed regularly, sanitation issues can crop up. These issues can escalate if cleaning procedures are ineffective, too.
Allocate sufficient time and resources to cleaning processes and procedures. A manufacturer can employ a third party to clean its facility. Or, a manufacturer can take appropriate measures to clean its facility on its own.
5. Limited Budget
Manufacturing budgets can be restrictive. A manufacturer has only a finite amount of money it can commit to cleaning. Despite its best efforts, the manufacturer may struggle to make the most of its cleaning funds. As a result, the manufacturer may have sanitation issues and lack adequate funding to resolve them.
When faced with a limited cleaning budget, look at all available finances. Next, a manufacturer can search for ways to allocate more money to cleaning. It may also find opportunities to help its employees make their work environment a clean, safe, and productive space.
How to Fix Sanitation Issues
There is no one-size-fits-all approach to fixing sanitation issues in manufacturing plants. However, there are several tried-and-true practices a manufacturer can use to identify and mitigate such issues, such as:
1. Set Up Signage Across Your Workplace
Use signs to promote proper sanitation practices. Signs can be set up at different spots across a work environment. They can serve as frequent reminders for workers to follow best practices for sanitation.
Make sure any signage is clear and concise. Signs can include both images and text and should leave no room for misinterpretation.
2. Empower Your Workers
Show workers how to properly sanitize a manufacturing workplace. Develop and implement a sanitation education program for workers. The program can teach workers of all skill and experience levels how to keep a workspace clean.
Provide hands-on tutorials on how to complete various manufacturing cleaning tasks. For instance, a manufacturer can explain the ins and outs of a sanitizing “wet clean flushes” enclosed system for food conveyors to its workers. From here, workers can use the system to ensure food safety and speed up product changeovers.
3. Make the Right Investments
Audit a manufacturing plant to learn about any sanitation issues. The audit enables plant leaders to identify problems and correct them before they get out of hand.
Following an audit, make a sanitation plan. This allows a manufacturer to establish guidelines for sanitation. The manufacturer can choose the best cleaning processes and technologies in accordance with these guidelines.
4. Learn from Your Employees
Conduct surveys and questionnaires of manufacturing plant employees. This allows plant leaders to get insights into sanitation issues.
Encourage workers to come forward with any sanitation concerns or questions. Work in lockstep with employees to correct any sanitation issues.
5. Strive for Constant Improvement
Monitor the results of sanitation efforts. Keep an eye out for opportunities to improve sanitation every day.
Watch for new sanitation technologies as well. Technologies are already available that help manufacturers reduce changeover and cleaning times and minimize their operational costs. New technologies are in development that manufacturers may be able to use to optimize their sanitation efforts.
Don't Wait to Address Sanitation Challenges
Manufacturers must work diligently to sanitize their workplace. Be proactive, and a manufacturer can identify and mitigate sanitation issues and prevent them from recurring.
Comments (0)
This post does not have any comments. Be the first to leave a comment below.
Featured Product
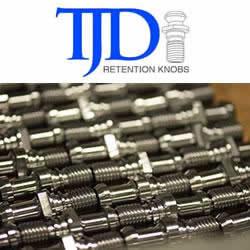