Automating Risk Management to Improve Employee Safety in Warehouses
Automating warehouse facilities has many recognised operational benefits – from increasing efficiency, improving productivity and becoming less reliant on the manual workforce. Yet, a common misconception of automation is that it can negatively impact employees' safety. Indeed, in Guidance Automation’s 2022 research, 64% of respondents said that safety concerns around physical accidents caused by automated systems were preventing them from implementing warehouse or manufacturing plant automation.
Such findings demonstrate a lack of education around automation – as rather than being a barrier to deployment, businesses should consider automation’s capability to minimise health and safety risks a positive. Dr Paul Rivers, Managing Director of Guidance Automation dispels existing perceptions around the risks of automation and argues that by embracing automated solutions, warehouse managers will be able to better manage existing hazards, and in turn, improve employee safety.
Health and Safety in Logistics
Warehouses are acknowledged high-risk environments, with people, forklifts and other equipment moving continuously around. According to HSE’s March 2022 RIDDOR (Reporting of Injuries Diseases and Dangerous Occurrences Regulations) data, the number of employees who suffered fatal injuries in the manufacturing and transportation & storage sectors increased in 2021/22 compared to the previous five-year average. Something must be done to reduce these worrying statistics and give employees the reassurance that the environment they are working in is safe.
Risk management is a vital part of logistics businesses’ health and safety strategies to manage and mitigate any potential risks. When assessing a warehouse space, there are a number of factors to consider for the health and safety of staff, including; the use of hazardous substances, risk of fire and flooding, or falling from high buildings. Disruptions cannot always be planned for – and common hazards may appear – but having a comprehensive risk management plan in place will enable businesses to make warehouses safer. So where does automation come in?
Automation as a Solution – Not a Problem
By taking an automated approach to risk management, warehouse managers can better manage the threats that the warehouse poses. For example, warehouse automation reduces the human workforce’s exposure to forklifts and other heavy equipment as AGVs (automated guided vehicles) and AMRs (autonomous mobile robots) can instead be deployed. With forklift accidents rising – with around 1,300 UK employees hospitalised each year with serious injuries following forklift accidents - mitigating reliance on forklifts is a crucial factor to improve safety in the warehouse.
Automation can also improve existing processes in the warehouse, such as using picking robots to reach products that are high above the ground – removing the need for workers to climb ladders. Additionally, AMRs, for example, don’t tire or require breaks, unless they need charging, and are aware of their own limitations. Therefore, deploying automation technologies for manual operations, including packaging and moving boxes, can not only enhance productivity, but also help to prevent injuries that perhaps are caused by worker fatigue or repetitive motion.
Embracing automation to take over some manual tasks, not only lessens the risk of injury to the workforce, but also offers additional opportunities for value-added tasks to be undertaken, as well as upskilling. Humans can instead be deployed to carry out more complex analytical tasks or decision-making operations – leaving the automated technologies to take on any potentially dangerous or repetitive roles.
The Role of the Vendor
A number of companies in Guidance Automation’s research also raised concerns about staff safety when working alongside robotics. However, safety is an absolute priority for all robotics vendors. This is of utmost importance considering the senior management of these companies are personally liable for any health and safety breaches under UK law. Therefore, logistics businesses can work with an automation specialist to identify areas where automation can specifically be used to mitigate health and safety risks, as well as bettering existing risk management processes.
An automation vendor can approach implementation in a way that can mitigate any risks that automation could also potentially introduce. By undergoing a free trial with an automation provider, logistics businesses can not only gain insight into the productivity and efficiency benefits of automation – but also find out how it can improve safety and reduce potential hazards. This will help to ensure that when working alongside AMRs, employees are equipped to do so safely.
For example, vendors can ensure that their automated robots will function based on specific programming, following an optimised pathway and moving at a certain speed in a warehouse – using sensors to detect and avoid obstacles and/or humans – reducing the risk of injuries. With built-in safety features, such as these sensors, and an emergency stop, self-driven vehicles become much safer compared to human drivers.
Conclusion
There are many health and safety risks involved when working in a warehouse environment, and even with adequate safety measures in place – accidents can still happen. Automation, although misconceived at times to increase those risks, can actually prevent accidents from happening in the warehouse by reducing reliance on manual labour and deploying innovative technologies to improve existing processes. As such, improving worker safety is just another compelling reason to incorporate automation into warehouse and risk management practices.
Comments (0)
This post does not have any comments. Be the first to leave a comment below.
Featured Product
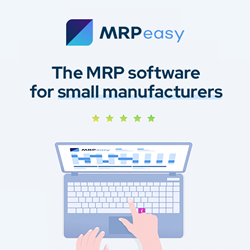