MICRO MOLDING – PLACE THE FOCUS ON OUTCOMES
For customers looking to embrace the possibilities that exist through the micro molding of parts or components, there is a given. They need to understand what micro molding can do in terms of stimulation of innovation, what it can deliver in terms of manufacturing efficiency, and what — above all — it can do to achieve increased functionality in parts that are often required to be smaller and smaller.
As such, the requirement is not for lectures at conferences and articles in learned journals explaining how the micro molding process works. Interesting as this may be for those with a penchant for “serious science”, when you team with a qualified micro molder, you can leave that side of things to us. We have spent decades refining the art and science of micro molding, we understand the complexities of molding at the micro scale, and so this allows you and the molder to focus on the outcomes. How can you work together with your chosen molder to achieve your product goals, and how can you do this cost-effectively, and ultimately scale up to reliable and repeatable volume production.
So in this article, the focus will be on what influences the ability of micro molders to mass manufacture successfully, and what influences the process of developing micro parts and components. What is it that makes the partnership between you and your chosen micro molder tick, and therefore achieve your goals.
MICRO MOLDING
Micro molding often necessitates the accomplishment of exacting, and sometimes seemingly impossible, tolerances. Clients may require minuscule parts, smaller than a grain of salt or with sub-micron feature sizes. When such micron tolerances are significant, the customer and micro molding provider must form a special, more intimate partnership for product development. Consequently, the micro molder must take charge and innovate within all aspects of the supply chain.
Manufacturers not used to such exacting tolerances may think it impossible to mass produce parts with such minuscule dimensions and levels of accuracy, yet micro molders do this every day. It's especially challenging when dealing with parts as light as 0.001 grams that are needed for safety critical applications, where zero failure rates must be observed.
Not only do micro molders need to make tiny parts with tiny features in a repeatable manner and achieve micron tolerances, they need to do so in a cost-effective and timely manner as well. Hence, it is imperative that we avoid having to go back to the drawing board with our designs, reviewing and changing manufacturing processes, and re-cutting already expensive and time-consuming micro-tools. "Get it right the first time" is the headline over every activity.
A successful micro molder must understand CTQs (Critical to Quality characteristics) to manufacture parts, and these characteristics encompass molding, assembly, and packaging as well as the functionality of the product in terms of the end-user experience.
Value-stream thinking — from concept to order fulfilment — drives customer value. Vertical integration reduces silos and suboptimal processes by reducing the length of the value stream. Essentially, the longer the value stream, the more disconnected it becomes, and the more variables that can cause customer problems will be introduced.
ATTAINING VOLUME
Customers demand the best products at a competitive cost. Voice of the Customer data allows micro molders to identify essential characteristics which need to be monitored at production. Setting cost also includes factors such as timetables, eliminating defects and maintaining consistent supply. Micro molders should seek to provide top quality products via validated processes with quick turnaround times. This can only be accomplished by having vertically integrated processes and validating them thoroughly.
So, when shortlisting potential micro molding suppliers, from a production standpoint, there are some key questions that need to be asked to ensure that the micro molder is equipped to achieve often exacting objectives. First, do you design, build, and maintain your molds? Second, what measurement capabilities do you have on site? Third, what are the methods of validation you use? Last but not least, what resins have you experience of using in production?
VOCs play a significant role in the success of micro-molded products. However, the end user isn’t just the customer. There are customers throughout the entire value chain. Concerns can be raised and resolved quicker when the value stream is shorter and more centrally located.
ASSEMBLING
When dealing with miniaturized plastic parts and components, it is crucial that assembly is brought up early in the design process. This calls for an effective collaboration between OEM and micro molder. The manual assembly of micro components is usually too expensive and very precise sub-micron tolerances can't be achieved by human hands – thus automated assembly is necessary. This also means that OEMs have to pick a micro molding provider that is capable of recognizing the principles of micro assembly as well as achieving extreme exactitude.
A laser-like focus on design for micro manufacturing (DfMM) is essential for the success of any product development process, including assembly. Micro molding projects present a unique challenge in that they involve more variables and require more precision than typical projects. It can be difficult to feed, inspect and manipulate these parts without causing damage, as well as capturing and orientating them after molding. Capturing parts at the mold ejection stage coupled with immediate assembly is often the most effective way to assemble micro molded parts with minimal waste.
In order to maintain margins and provide a product to the market at an affordable price, such considerations should all be bottomed-out at the design stage.
WHAT THIS MEANS
Before embarking on a micro molding project, customers should focus on the mold design, mold build, and quality measuring capabilities of the vendor they are engaging to mold their parts. If molders lack the ability to design, build, and measure high quality molds to extremely tight tolerances they will struggle to produce consistently high-quality parts to tight tolerances. Producing products to specifications that only allow microns of variations to a specification is much more challenging than producing a product with significantly larger variation allowances. A poorly designed and built tool can eat up your entire variation before you even mold a part, essentially killing the project.
So, focus on your chosen supplier’s capabilities in these areas rather than worrying about the way the micro molding process works per se. It should be a given that a micro molder can micro mold, and therefore take away the headache of you needing to understand the process. It is not a given, however, that a micro molder can work with you and have the capabilities beyond molding to guarantee product success and volume production.
Aaron Johnson is the VP of Marketing and Customer Strategy at Accumold. The company has grown to a 130,000 square foot fortified facility designed for assurance of supply, employs over 350 staff, and is a net exporter shipping all over the world every day from its Ankeny, IA, USA facility which runs 24 hours a day, 7 days a week.
Comments (0)
This post does not have any comments. Be the first to leave a comment below.
Featured Product
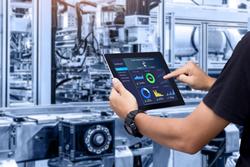