How 3D Printing Can Dramatically Reduce Carbon Emissions in the Manufacturing Industry
Additive manufacturing, or 3D printing, has been making waves in the manufacturing world for years, promising to churn out products better, faster, and cheaper—and with a fraction of the carbon footprint that encumbers traditional manufacturing methods. Now, a paper from Delft University of Technology researchers has put a number on that promise. It estimates that additive manufacturing can lead to a 5–27% reduction in global energy use by 2050.
At the heart of this potential revolution is 3D printing’s capacity to manufacture products in a much more eco-friendly way. Specifically, the technology can cut carbon emissions in the four areas where traditional manufacturing cranks out carbon by the metric ton: materials, manufacturing, warehousing, and transportation.
Let’s start with transportation. Perhaps the most significant atmospheric benefit of 3D printing is that it dramatically reduces the need to move finished products great distances and thus greatly diminishes the overall carbon footprint of those products. In essence, any location with a 3D printer can be a “virtual factory” that makes products, from shoes to phone cases, onsite and on-demand.
The reality is that the transportation of finished products from one place to another currently accounts for approximately 30% of that product’s carbon footprint. But when 3D printing is used, this number drops drastically because, with 3D printing, manufacturing can be onshored and products made closer to their core market rather than manufactured in far-flung countries, then shipped to their destination.
The eco-advantages of 3D printing extend to other areas as well, including materials and the manufacturing process itself. For instance, traditional manufacturing methods generate significant waste in the form of scrap material that can’t be reused. With 3D printing, material waste can be reduced by up to 90%. How is this possible? Well, most traditional manufacturing methods start with a block of raw material and remove excess material to create the final product. This process inevitably leaves behind a large amount of scrap material—and this material is often difficult and expensive to recycle, so it ends up in landfills and incinerators and produces a great deal of pollution and greenhouse gases.
3D printing, on the other hand, builds objects layer by layer and uses only the material necessary to create the finished product. It does not generate any significant amount of scrap. Furthermore, 3D printing can be used to repair parts or change the part design while using fewer raw materials, resulting in greater savings.
3D cuts CO2 in many ways
In terms of the manufacturing process itself, 3D printing makes use of complex geometries that are impossible with traditional methods. This means that engineers can design parts that are lighter, stronger, and more efficient than their traditional counterparts. Better still, the 3D printing process typically consumes much less energy than an injection-molding machine. This makes 3D printing more environmentally friendly—especially for small production runs of 50 parts or less and for custom-made parts. However, without any design optimization, if a part is transitioned to 3D printing from traditional manufacturing, the energy needed for production will remain the same of even increase sometimes. So, it is important to optimize the part design for 3D printing to realize production energy reductions.
Still, another benefit is in the warehousing sector. Because 3D printing enables on-demand production of parts and products, it can help reduce inventory loads. In traditional manufacturing, large quantities of parts and products are made in advance and stored in warehouses to meet future demand. This results in high inventory and warehousing costs.
In contrast, 3D printing enables the production of parts on demand, eliminating excess inventory and reducing the need for storage space. That means a manufacturer can seriously cut costs because it is no longer using all that energy once required to control temperature and humidity and light large warehouses. This leads to a lower overall carbon footprint considering warehousing significant contributor, as much as 13% of carbon emissions of logistics.
Shoes 3D printed in the U.S. kick carbon to the curb
Let’s look at a real-world example: shoes made in China with traditional manufacturing methods versus shoes made in the U.S. with additive manufacturing. The shoes made in China produce volumes of carbon from start to finish. The raw materials needed produce 20%-25% of total emissions, the manufacturing process 15%-20%, transportation 30%-35%, and end-of-use another 20%-25%.
When the shoes are 3D printed locally instead of overseas, transportation emissions drop from 30%-35% to just 5%. Because less raw materials are needed for 3D printing, those emissions drop from 20%-25% to just 10%. Because 3D printing produces less scrap, emissions associated with waste disposal drop to 5%-10%. 3D-printed shoes produce 40% less carbon emissions and, if energy-efficient practices are added in, potentially as much as 60%.
And it’s not just in consumer goods where 3D printing has an impact. Additive manufacturing is helping other industries like aerospace and defense reduce their carbon footprint. For example, many of the components used in aerospace are made by primary contractors, and it’s a fraught process. If, say, a tiny part of a landing gear is damaged during operation, often the entire gear is rendered unusable. Traditional repair services won’t help due to the small size of the damaged part. If, on the other hand, the landing gear is repaired using 3D printed, the manufacturer/operator can simply print a replacement part and plug it in. This way, the average life span of parts is increased and the need to make new parts is drastically reduced. This is just one example of how 3D technology can reduce waste and positively impact the world.
Final takeaway
Imagine a future in which manufacturing is no longer a dirty, wasteful process that leaves heavy carbon footprints all over our home planet. 3D printing has the potential to make that future come true as long as 3D printing design efficiencies are used and a conscious effort is made to onshore production. It can revolutionize the manufacturing industry by enabling efficient production methods that reduce waste, cut energy consumption, and all but eliminate transportation emissions. That’s the exciting and sustainable vision of 3D printing.
Comments (0)
This post does not have any comments. Be the first to leave a comment below.
Featured Product
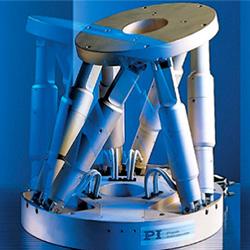