PHOTO CHEMICAL ETCHING: REVOLUTIONIZING ELECTRIC VEHICLE COMPONENT PRODUCTION FOR CLIMATE CHANGE MITIGATION
As the world grapples with the pressing issue of climate change, innovative technologies are playing a pivotal role in addressing environmental concerns. One such ground-breaking technology is photo chemical etching (PCE), which has emerged as a Here we delve into the application of PCE in the EV industry and explore how this innovative technology contributes to environmental targets by enabling the production of innovative products that promote sustainability.
PCE IN EV PRODUCTION
PCE, also known as chemical milling or photo etching, is a subtractive manufacturing process that utilizes a combination of light-sensitive photoresist, chemicals, and precision etching to produce intricate components with high accuracy and repeatability. This technique is extensively employed in the production of various components for EVS, ranging from battery contacts and connectors, bipolar plates for fuel cells, to intricate circuit boards and motor laminations.
One of the key advantages of PCE is its ability to produce components with exceptional precision and intricate designs. The process allows for the creation of complex geometries, intricate patterns, and fine details that are challenging to achieve using traditional manufacturing methods such as stamping or machining. This level of precision is critical for the efficient operation of EVs, as it enables the creation of optimized components that contribute to overall system efficiency and performance.
EVs require lightweight components to maximize their range and energy efficiency. PCE offers a unique advantage in this regard, as it allows manufacturers to produce thin, lightweight yet robust components. By using thinner materials without compromising strength, the weight of components can be significantly reduced, leading to improved energy efficiency and extended driving range.
Additionally, PCE provides cost-effective solutions for the production of EV components. Traditional manufacturing methods often involve costly tooling, which is not required in the PCE process. This eliminates the need for expensive dies or molds, reducing production costs and enabling the development of cost-effective EVs.
ENHANCED ENVIRONMENTAL SUSTAINABILITY
While PCE may not be inherently clean, its environmental benefits lie in its role in enabling industries to contribute to environmental targets by producing innovative products. By facilitating the production of intricate and efficient components for EVs, PCE plays a vital role in the transition to a greener transportation sector.
Energy Efficiency and Reduced Emissions. The lightweight and precise components manufactured through PCE contribute to the overall energy efficiency of electric vehicles. The reduction in weight improves vehicle aerodynamics, reduces power consumption, and extends battery life, resulting in lower emissions and a smaller carbon footprint. By enabling the production of energy-efficient EV components, PCE supports the achievement of environmental targets in the transportation sector.
Sustainable Material Usage. The PCE process allows for the efficient use of materials, minimizing waste and promoting sustainability. Unlike traditional manufacturing methods that generate significant material waste through machining or stamping processes, PCE is a highly material-efficient process. It allows manufacturers to optimize material usage by selectively etching away excess material, reducing scrap and minimizing environmental impact.
Facilitating the Adoption of Electric Vehicles. By producing high-quality components at lower costs, PCE contributes to the wider adoption of EVs. As the demand for EVs increases, economies of scale come into play, leading to more significant environmental benefits. Increased EV adoption helps reduce reliance on fossil fuels and decreases greenhouse gas emissions, ultimately mitigating climate change.
The widespread adoption of EVs is crucial for achieving ambitious environmental targets and combating climate change. PCE plays a vital role in accelerating the transition to electric mobility by enabling the production of components that enhance the performance and efficiency of electric vehicles. As the EV industry continues to grow, the demand for advanced components manufactured through PCE will rise, further driving innovation and sustainability in the transportation sector.
COLLABORATION AND KNOWLEDGE SHARING
The implementation of innovative technologies like PCE requires collaboration and knowledge sharing between different industry stakeholders. Companies like micrometal that specialize in PCE work closely with electric vehicle manufacturers, design engineers, and material suppliers to develop optimized component designs, select suitable materials, and ensure efficient production processes. This collaborative approach fosters innovation and helps create a sustainable ecosystem that contributes to environmental targets.
The adoption of PCE in EV component production is an ongoing process of continuous improvement and research. Manufacturers are investing in research and development to enhance the capabilities of PCE, improve process efficiency, reduce waste, and explore new applications. These efforts are vital for meeting evolving environmental standards, improving component performance, and further reducing the environmental impact of the EV industry.
CASE STUDY
Historically, CNC-machined graphite has been the material of choice for producing bipolar fuel cell plates. Unfortunately, it is rather expensive and suffers from excessive permeability, making it unsuitable for mass production. Metal alloys such as stainless steel and titanium are gaining popularity due to their cost-effectiveness and simple manufacturability. Moreover, stainless steel offers many great benefits for fuel cell applications, including remarkable strength, chemical stability, and durability.
Fuel cells are made up of intricately machined plates with grooves or channels to allow gas and liquid flow, but the scalability and ability of CNC-machining, hydroforming, and stamping techniques is questionable.
PCE provides manufacturers with a viable means of producing complex components, such as bipolar fuel cell plates, with noteworthy benefits.
Utilising digital tooling instead of hard tooling, PCE offers the significant benefit of being cost-effective and allows designs to be readily customised. This is hugely advantageous in terms of optimising without incurring excessive expenses.
The process facilitates quick scale up from a prototype to high volume production, with almost no limit on the complexity of components - ideal for fuel cell plates that must be free of imperfections in order to successfully bond the stack. It does not affect the temper or properties of metals, is suitable for all grades of steel, and accuracy is ensured at ±0.025 mm; all done in days instead of months.
PCE is a versatile technology which allows for the simultaneous removal of metal. This enables complex patterns and channels to be etched to an accuracy of 0.025mm on both sides of the plate, with features such as headers, collectors, or ports easily achievable at no extra cost.
At the micrometal Etching Group, such components can be produced in certain exotic and hard to machine metals, such as titanium, for lighter weight and superior protection from corrosion in high-temperature fuel cell applications.
SUMMARY
Innovative technologies, such as PCE, have proven instrumental in addressing climate change by enabling industries to produce innovative and sustainable products. In the context of EVs, PCE plays a crucial role in the production of precise, lightweight, and cost-effective components that contribute to environmental targets. By enhancing energy efficiency, reducing emissions, promoting sustainable material usage, and facilitating the wider adoption of electric vehicles, this revolutionary manufacturing process is helping reshape the transportation sector and mitigate the impacts of climate change.
As the demand for EVs continues to rise and environmental regulations become more stringent, the significance of PCE and other innovative manufacturing processes will only grow. Through collaboration, research, and continuous improvement, the EV industry can leverage these technologies to develop increasingly efficient, eco-friendly, and affordable vehicles. The convergence of innovative manufacturing techniques and sustainable transportation solutions holds the key to a greener future, where climate change is addressed through the production of innovative and environmentally conscious products.
micrometal Etching Group is proud to be at the vanguard of such innovations.
About micrometal
micrometal GmbH (incorporating HP Etch and Etchform) specialises in the industrial production of highly precise metal components. The 3 companies photo-chemically etch very large numbers of parts for a multitude of industries with an accuracy that is unique. The companies etch a huge range of metals, and deliver customer-specific, clean, complex components, free of stress and burrs. micrometal’s, HP Etch’s and combined processes and expertise offer the right solution for every challenge. The companies provide a one-stop-shop to customers looking to benefit from a world-class photo-chemical etching service.
Comments (0)
This post does not have any comments. Be the first to leave a comment below.
Featured Product
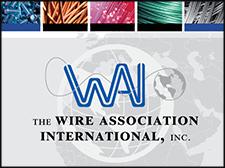