What Is MES & Why Should Manufacturers Invest In It?
A manufacturing execution system, often referred to as MES, has quickly become a staple within many businesses around the globe. Offering manufacturers a dynamic software solution that is capable of monitoring, tracking, controlling and documenting manufactured products throughout production; MES provides key decision-makers with all of the information they require to implement efficiency driven changes to their operations.
Whilst MES has established itself with some of the major manufacturers, there’s still a large number of businesses that could stand to benefit from the solution but simply don’t have enough understanding about the tangible benefits it can bring to their operation.
Mike Bradford, Strategic Business Development Director at DELMIA, part of the Dassault Systèmes Group, gives us an in depth review of what MES is, why it’s essential for manufacturers and the key differences between manufacturing operations management (MOM) and MES.
What is the difference between MOM & MES?
First, it’s important to differentiate between MES and MOM, as a lot of people within the industry use the terms interchangeably despite them not being the same thing. In fact, MES is actually a component of a wider MOM system, and they work hand in hand to give manufacturers capabilities that cross their entire operation
MES is primarily focused on production, so it will integrate into your equipment and give you visibility into machine status, highlight the operator work instructions whilst also tracking time for production. It also provides businesses with a full report on production and can identify any errors with the machine and workflow, essentially giving your business all of the information that is required to make quicker fixes to issues that arise.
In terms of a wider MOM solution, this will look at the work instructions, link to machinery and the top equipment on the shop floor production. But the main differentiator comes where a MOM solution will also provide capabilities and visibility in other key functionality like quality, maintenance and materials / warehouse. You can integrate quality control, material synchronization and maintenance planning & execution into your overall manufacturing process, so that your line side quality, material supply and maintenance activities are part of your production process within your MOM solution. It doesn't require separate systems, separate reporting, or separate tracking.
Why Invest in MES?
Whilst there is plenty of awareness about the benefits of MOM for manufacturers, the same can’t be said of MES as there are still many within the sector who aren’t totally sure what it brings to the table. When it comes to investing in MES, the most important thing to note is just how much value it can bring to your business, especially when helping reduce lead times.
It also plays a role in reducing the overall inventory required, as businesses won’t need any ‘just-in-case’ inventory as a MES will ensure accurate inventory records are maintained. This will ensure manufacturers are able to stock as much as they require, with no surplus. DELMIA implemented a MES solution for Cummins, a farm equipment manufacturer and were able to reduce their inventories by $36 million by simply having an effective MES inventory solution in place to reduce waste. Alongside this, throughput was increased by 25% due to real-time reporting and the greater visibility afforded to the company by the Apriso production MES that was provided. In a separate case study, DELMIA’s MES managed to save an aerospace company $4 million each year by reducing overall scrap waste.
Many manufacturers will see quality and throughput improvements simultaneously when MES is in place, which can remove huge bottlenecks in the production process. Most businesses will add quality gates during the manufacturing process to ensure the quality of each product is as high as possible, this inevitably slows overall throughput. With MES integrated as part of the process, the quality control aspects of production can be streamlined and, in some cases, removed, further enhancing the overall efficiency and profitability of the business.
It's also worth noting that you can improve reporting because quite often in environments which are still utilising manual inputs they end up adding the production and scrap counts at a later date. In the manufacturing industry, it is widely accepted – and proven in detailed studies – that when inputting data on production statistics, there is anywhere between 85% - 90% data accuracy. The 10% - 15% variable on this can throw overall production, inventory and scrap figures out by a long way, which inevitably leads to more costs in the long run. Incorporating MES into production is a sure way to improve overall reporting and remove outdated and time-consuming manual data input, which is sure to save any manufacturing business money over time.
In summary, there’s real value at every step of that process by rolling out an all-encompassing MOM solution. When pairing your MES solution with true MOM, you’re likely to see even more benefits and a vast reduction in inventory, waste, and overall inefficiencies. So, when it comes to the question “why invest?”, the simple answer is because there's real value in incorporating MES whether that be into an existing MOM solution or as a standalone product.
There is a value found typically in improvement, improved productivity, improved quality, including getting right first time through robust MES solutions, and all manufacturing firms should seriously consider the improved efficiencies and cost savings they can bring. Over time manufacturers can stand to save incredibly large sums through simply removing inefficiencies and ensuring that no surplus products are made. MES simply doesn’t get as much attention as the far more established MOM solutions do, but in time professionals within the sector certainly will see the tangible benefits that MES brings.
Comments (0)
This post does not have any comments. Be the first to leave a comment below.
Featured Product
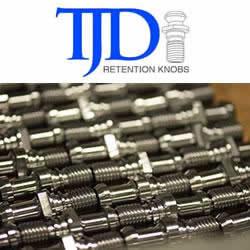