The Role of PLCs in the Modern Industrial Revolution
Programmable Logic Controllers or PLCs have come a long way since their original invention, and their use at companies like General Motors in the 1960s.
New kinds of PLCs are contributing to new approaches to manufacturing and industrial systems. Many people are referring to the more general trend as a ‘new industrial revolution’ or ‘industry 4.0.’
Let's look at how PLCs work, and what role they play in modern architectures.
What are Programmable Logic Controllers?
A Programmable Logic Controller is a ruggedized component that will help run industry and manufacturing systems and processes.
One of the best ways to talk about PLCs is to describe the hardware they are replacing. These involve mechanical and analog relay switches, as well as things like cam-based timers or other physical equipment that is not digital and programmable.
PLCs, by contrast, are receptive to changes in programming, and their use factors into modern automation.
Programmable Logic Controllers and Sensors
Engineers often talk about the process of using PLCs for ‘feedback loops’ that help them to control manufacturing or industrial equipment. In some cases, forms of computer vision or sensing are essential to the capabilities of robotic systems managed by PLCs.
Using components like sensors and actuators, engineers can build environments where the PLCs can figure out what's happening in their immediate surroundings, and control outputs to regulate things like liquid flow, building, or processes like capping or sealing containers.
Or, in environmental administration, the PLCSs with their related monitoring capabilities can be important for things like hazard monitoring.
You could say that Programmable Logic Controllers can ‘feel’ their environments, in some senses, and control their application variables accordingly. The sophistication of PLCs and related hardware grows as AI/ML advances, and data science expands what automation can do in an industrial scenario.
PLCs and Control Levels
Some experts talk about five ‘levels’ of industrial planning with new hardware systems:
- Management level
- Planning level
- Supervisory level
- Control level
- Field level
Here, the PLCs would be part of the control level category, working with components like sensors and actuators that would be part of the field level.
At a higher level, centralized software ties everything together.
Programmable Logic Controllers and Enterprise Resource Planning
Up at the top at the management level, Programmable Logic Controllers can be tied into Enterprise Resource Planning or ERP software.
The scope of the ERP software is broader than just a set of manufacturing tasks; in addition to providing comprehensive decision support, it builds in other aspects like evaluation of processed volumes, and oversight of process standards.
In general, integration means that those PLCs that are playing their role in systems are tied into something greater than themselves.
You can contrast these centralized systems to an earlier approach called machine to machine (M2M) where individual manufacturing hardware pieces would ‘talk’ to one another through software. The ERP system is, in general, a more global model.
So what do PLCs do? Well, they can help monitor applications, they can execute tasks, and they can perform functions. For example, some monitoring PLCs may have sensors that will show them if a pipe or conduit is compromised or leaking. Then they can send an alert to human operators, or even take automated steps to control of the problem. Businesses are seeing the powerful utility of these kinds of automation, and installing new next-gen systems with these sorts of functions.
PLCs and the Internet of Things
Many different types of PLCs in industrial systems contribute to the idea of the Internet of things or IoT.
The Internet of Things generally describes a phenomenon where different types of hardware components become connected wirelessly, often through the Internet. It involves combining local area networks with the Internet as a whole, to get data from a local point to some other destination. For example, consumer appliances and devices will often be part of the IoT where they can send different types of field-captured data to a vendor or other remote party for evaluation.
Other PLCs, though, may be more localized in terms of their role. Some are connected through ethernet in cabled systems that are largely focused toward controlling the local environment.
The PLC and New Architectures
In any case, PLCs are a key component of many of these modern industrial systems. They’re helping to replace a lot of the human monitoring, calibration and management that have traditionally been needed for industrial processes. In other words, people can sit back and let the machines do more of the work for them. In general, proponents of the fourth Industrial Revolution often suggest that there should be a ‘human in the loop’ or human role involved in the process. However, PLCs and other components are making it much less important for humans to be physically present and always watching a given hardware system directly.
Comments (0)
This post does not have any comments. Be the first to leave a comment below.
Featured Product
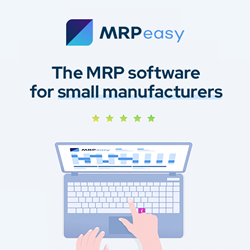