5 Strategies for the Long-Term Preservation of Heavy Machinery
Educating Employees
Heavy machinery can break independently due to manufacturer issues, glitches and accidents. However, humans are often the root cause of outages and downtime. Data from the Uptime Institute show people cause about two-thirds of outages, leading to unwanted downtime. Every hour of downtime can cost a company thousands of dollars, emphasizing the need for comprehensive employee education.
Supervisors should prioritize heavy machinery training for employee safety and the preservation of machines. These training sessions should teach workers the limits of each device so they don’t accelerate wear more than expected. Wisely using machines from the beginning teaches good habits and keeps equipment in solid shape. Additionally, it reduces costly and deadly incidents. OSHA reports that 75% of struck-by fatalities occur because of heavy equipment.
Equipment may wear over time, as will the employees’ knowledge of modern technology. Companies should upskill and retrain workers to keep them with the times. Employees appreciate upskilling because it gives them more confidence and professional development opportunities. Research shows upskilling leads to an $8,000 advantage over those who don’t.
Creating Maintenance Schedules
One of the best strategies for long-term preservation is creating maintenance schedules. This method ensures each machine gets regular attention and service as necessary. Identifying problems during maintenance is preferred because tiny issues can snowball if managers aren’t careful.
Maintenance schedules should be as comprehensive as possible so inspectors can account for every detail of the machine. Here are a few examples of duties for maintaining heavy machinery:
- Lubricants: The first part of the inspection should include the lubricants. These substances reduce friction and keep equipment running smoothly but can cause messes and clogs. Inspectors should ensure each machine has the proper amount of oil by checking the manufacturer’s recommendations. Too much lubricant leads to buildup and compromised performance.
- Tires: While they may be obvious, tires are an overlooked component of heavy machinery due to focus elsewhere. Supervisors should regularly inspect the tires visually while also checking the tread depth. Factory floor hazards, such as loose nails, can ruin a tire if they’re in the sidewall.
- Cleaning: Cleaning is another maintenance task some manufacturing professionals overlook. Dirt and other contaminants build up over time, especially if the company uses outdoor equipment. Supervisors should periodically clean their machines using acid baths and powerful pressure washers to ensure the equipment is clean.
Being Proactive
While maintenance schedules are commendable, manufacturing professionals can go the extra mile to proactively tackle problems before they appear.
For example, rust is an issue for manufacturers worldwide due to precipitation and humidity — especially in coastal areas. Mitigating rust means taking preventive measures, such as annual or biannual waxing for equipment. Heavy machinery could use a fresh coat of paint to ensure it lasts as long as it should. Otherwise, rust will compromise the infrastructure and be a safety issue.
Recording Maintenance Details
While maintenance is necessary, properly tracking such maintenance is almost as crucial. Technicians should know if the previous inspector replaced parts, rewired an electrical system or made other repairs. Knowing this information increases transparency for everyone involved and fosters an environment where workers hold each other accountable. Additionally, having records helps when filing claims with manufacturers and successfully navigating warranty policies.
Some companies manually record their maintenance records or use simple spreadsheets, but modern technology lets manufacturing professionals make this process more efficient. Preventive maintenance software takes some responsibility away from humans by using algorithms for optimization. These programs use data to manage inventory and increase transparency with costs and maintenance schedules.
Optimizing Storage Solutions
Some heavy machines don’t see use all year, prompting a need for storage solutions. Equipment is typically safe inside a unit but can become vulnerable to outside threats if supervisors don’t take the proper precautions. Here are a few ways manufacturing professionals can preserve their equipment if long-term storage is necessary.
Indoor Storage Facilities
Weather can significantly affect machines even if they’re inside a storage unit. Poorly insulated facilities allow hot and cold air to slip in, compromising heavy equipment. For example, southern manufacturing companies are more likely to face dangerous heat waves. Hot and dry weather leads to increased dust and contaminants entering the machine. Additionally, heat compromises the machine’s sealants and leads to equipment failure without preventive measures.
Hot and cold weather are predictable, but severe thunderstorms give manufacturers less time to prepare. Regardless of the weather, companies should have a reliable climate-controlled facility to store their heavy machinery. While storage may add costs for businesses, there are some advantages to using off-site storage. For example, utilizing storage costs less than building a facility and frees up room in the current building.
Anti-Theft Measures
Identifying and addressing theft risks is critical. The manufacturing facility and storage units must recognize the prospect of stolen parts and pieces or entire machines. Anti-theft measures are vital for deterring criminals and keeping equipment safe. Thieves could be unsuccessful in stealing but still manage to harm devices, so supervisors should take action beforehand.
Locking up machines is a simple first step. Investing in high-quality locks prevents criminals from entering the facility in the first place, so they should be a first line of defense. Companies should go a step further and invest in smart surveillance systems. These devices use Wi-Fi and enable owners to monitor their cameras remotely. Additionally, users benefit from night-vision cameras, two-way audio and movement detection on their devices.
Elevation
Another way to preserve machines inside storage units is to elevate them. Long-term storage negatively impacts heavy equipment, especially its chassis. The heavy weight rests on the tires for weeks or months, damaging the wheels and requiring extra attention and dollars. Manufacturers who plan to store equipment long-term should instead elevate their equipment to decrease stress on the tires and chassis.
Concrete blocks may be a temporary solution as long as there is even weight distribution on each side. Although, there may be better answers for the long term. For example, jack stands are suitable for heavy-duty equipment and pose less risk than blocks. These solutions preserve machines even when nobody uses them for months.
Preserving Heavy Machinery for the Long Run
While high-quality machines can be a steep investment for manufacturers, the investment pays dividends with increased productivity and concrete results. However, the benefits can be short-lived if manufacturing professionals don’t care for their equipment.
Breakdowns and downtime are the last thing businesses need, so following these five strategies for preservation is essential. Supervisors should put as much in their employees’ control as possible to mitigate wear and tear.
Comments (0)
This post does not have any comments. Be the first to leave a comment below.
Featured Product
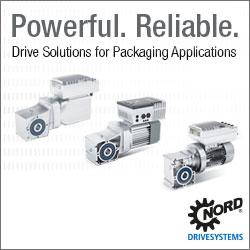