Making the case for Augmented Reality
The market size for Augmented Reality (AR) applications was estimated to be $15.2B in 2021 and growing to over $90B by 2028. This shows clearly that companies are investing heavily in this transformative technology but why is it such a key innovation and how can you make best use of it? Adrian Wood, Director of Strategic Business Development at DELMIA, takes a closer look at how augmented reality is on course to become a main part of manufacturing in the coming years.
Manufacturers today have many challenges related to the workforce. Firstly, the current workforce is aging and many of the critical skills and learnings are being lost as people exit the workplace. To replace them, manufacturers face a challenge of first enticing the workforce of the future onto the shop floor and then to onboard and train them to be productive as rapidly as possible without compromising safety or product quality.
The problem is compounded in industries with complex manufacturing and assembly and in highly regulated industries where exacting standards must be maintained consistently in operations. So, how can AR help with these challenges?
Imagine having a coach and assistant with you at all times as you are performing your daily tasks. Someone who is constantly offering guidance on what you are doing; how to do it safely; what risks could occur; and then evaluating what you have done. It sounds like an impossible luxury but this is essential what Augmented Reality delivers for workers. AR provides guidance and assistance for any operation in real-time by taking best practices and marrying them with visualization of the real world.
For example, digital assembly instructions developed directly from 3D digital mock-ups (DMUs) are materialized in the field by being projected directly onto the equipment or displayed on a screen. This shows the worker precisely what operation to perform and how.
In addition to assembly assistance, you can see AR applications across many different use cases such as …
- Quality Control of Assemblies: Controlling and identifying instances of non-compliance reliably and accurately at each stage of the manufacturing process
- Inspection of Supplier Equipment on Receipt: Ensuring parts are compliant before integrating them into the assembly lines
- Assistance with maintenance operations: Checking inspection control points and automating reports and documentation
One benefit of these use cases is the dramatic reduction in preparation time required for operators to start their tasks. It also reduces the possibility of error rates as operators are given precise guidance for each task. Overall, this means that production rates are increased and the operators themselves attain higher skill levels faster as they are continuously being “trained” as they work.
Across many different applications, AR has proven to be a valuable investment for many industries. Companies report immediate gains across key manufacturing metrics such as …
- Quality gains by reducing error risk by up to 90%
- Saving time by reducing cycle times from 20% to up to 80% in certain industries
In addition, there are other benefits around creating safer working environments for employees in hazardous or heavy manufacturing situations, which can dramatically reduce claims of worker injury and insurance costs.
AR represents a key tool for manufacturers to upgrade their shop floor and provide modern tools to attract the next generation of workers, capture existing best practices and then replicate them across the workforce.
Author Bio:
Adrian Wood has been the Director of Strategic Business Development for the DELMIA brand at Dassault Systèmes since 2019. He is responsible for developing new and innovative business markets and reinforcing the company position as an innovative leader in key industries.
Comments (0)
This post does not have any comments. Be the first to leave a comment below.
Featured Product
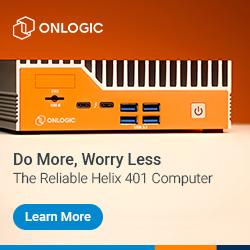