Why More Manufacturers Will Turn to No-Code Platforms in 2024
No-code and low-code platforms have transformed and democratized enterprise software-as-a-service. What used to be exclusively the domain of software developers, programmers and IT teams is now accessible to just about anyone who has some experience with if/then logic and drag-and-drop design tools like PowerPoint.
The manufacturing industry is no exception, though it presents a different set of challenges than software built for sales, customer service, marketing or design teams. Primarily that manufacturers produce physical outputs on the factory floor, not in offices with teams of developers. Successful no-code platforms for manufacturing will meet the end users where they are — on the frontline, at the workbench, in the plant.
Further, they’ll be accessible enough for those operators and engineers to build applications that solve their most pressing problems without any coding — as opposed to low-code platforms that do still require some programming background. And these platforms are purpose-built for manufacturing, designed to be deployed in the factory and supported by teams that understand the use cases.
So, why will 2024 be the tipping point for no-code platforms as the solution of choice for manufacturers?
1. The Market is Shifting
Successful manufacturers of all sizes already rely on no-code platforms and teams of internal citizen developers to execute mission-critical operations. Global organizations like Stanley Black & Decker lean on these platforms as a mechanism for worker empowerment, workflow continuity, machine integration, data collection, process efficiency, innovation, and continuous improvement. Biopharma companies leverage these tools to ensure quality, regulatory compliance, and eBR.
The tipping point is now behind us. Every organization looks to peers and competitors to understand which tools to trust. And any manufacturer examining platform options in today’s landscape will find no-code platforms as the tool of choice in any industry vertical.
2. No-code Tools Are Now Better Than Ever
The first and most critical aspect of manufacturers’ embrace of no-code tools is that they are mature, sophisticated, and reliable platforms. Modern SaaS tools are among the most complex and capable pieces of software in today’s tech world. Within that category, no-code platforms compromise very little compared to their low- or full-code counterparts in terms of feature fit and functionality, but more than make up for any perceived shortcomings by way of accessibility and user experience.
By empowering non-developer end users to build applications and solve for immediate needs fast, no-code tools gain higher rates of adoption and penetrate further into the organization than legacy platforms owned solely by full-time programmers and IT. And with platforms that also integrate low-code capabilities for more complex edge use cases, and connect to factory flow machinery, these platforms fill virtually any gap from IT to the C-suite to the frontline.
3. Manufacturing is Complex
Manufacturing has long been at the forefront of process technology, from interchangeable parts to the assembly line to AI and automation. No-code platforms are not a new concept, but have been slower to penetrate manufacturing simply because most software vendors have built their products for a different audience: not production facilities but office suites.
With purpose-built no-code platforms for manufacturing, these organizations now have another tool in their belt to streamline processes, elevate worker productivity, and deliver better quality at a greater scale and a lower cost. As manufacturers and industry change and grow, it’s critical that the platform of record has the flexibility to keep pace. No-code thrives in complex, shifting environments because the platform reflects the needs of the frontline at any given moment — it is built for change.
4. The cost makes sense
Given the realities laid out above, the ultimate takeaway for most manufacturers is: “Great, but what can we afford?” Cost factors into all decisions and software platforms often come with a high price tag.
But no-code app platforms deliver a competitive (or better outright) feature set for a lower per-seat cost compared to vertical SaaS counterparts. Even legacy platforms that do offer some additional features don’t do enough to make up the cost gap — no-code platforms can execute the processes manufacturers need them to execute, and are more likely to adapt well to AI and other future states.
No-code platforms are the natural, evolutionary progression of code-dependent SaaS solutions. Manufacturers are poised to transform operations and empower frontline workers in 2024 by harnessing these technologies.
Comments (0)
This post does not have any comments. Be the first to leave a comment below.
Featured Product
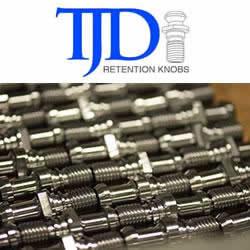