Decoding the Magic of KPIs: Beyond Metrics, Towards Operational Excellence
Harnessing the power of Key Performance Indicators (KPIs) is pivotal for evaluating and elevating organizational effectiveness. It’s one of the easiest ways to measure progress toward objectives, yet choosing which KPIs to monitor can be challenging: Of the hundreds of KPIs to choose from, which would you choose? Is monitoring just 5 enough? And of those 5, which would provide the best data?
In this article, you will find why KPIs are important, how to choose a useful KPI and why to use KPIs dashboards for easy tracking of KPIs for your packaging company.
What is a KPI?
A manufacturing Key Performance Indicator is a measurable value that shows how well an organization is achieving its business objectives. KPIs are based on data collected from production and business processes within an organization that are used to monitor, analyze and optimize operations. Often KPIs are used to compare efficiencies to those of competitors.
In other words, KPIs are success metrics gleaned from data from throughout the packaging manufacturing landscape and can give management accurate real time status of production processes, efficiency, and overall performance.
Keeping track of KPIs provides manufacturers with valuable insights that can drive informed decision-making and lead to improvements in various areas. Digging deep into these KPIs gives management the data to make adjustments for peak performance.
Examples of KPIs for packaging manufacturing:
Production Efficiency KPIs:
- Overall Equipment Efficiency (OEE) machines
- Production per hour
- Downtime due to machine issues
- Set-up time
- Rework
- Downtime due to machine issues
Quality Management KPIs:
- Defect Rate per job
- Customer Returns due to quality issues
- Conformance to specifications
- Accuracy of printing registration
- Box crush resistance and stacking strength
Inventory and Supply Chain KPIs:
- Raw material inventory turnover
- Supplier lead time for packaging materials
- Cycle Count Accuracy
- On-time delivery of packaging materials
- Stock-Out Rate for critical materials
Cost Management KPIs:
- Cost per product Produced
- Scrap and Waste Costs
- Manufacturing Cost as a Percentage of Revenue
- Return on Investment (ROI) for new equipment or technology
Downtime and Maintenance KPIs:
- Machine Downtime Percentage
- Planned Maintenance Compliance
- Mean Time Between Maintenance (MTBM)
- Emergency Maintenance Costs as a Percentage of Total Maintenance Costs
Workforce and Labor KPIs:
- Labor Productivity per shift
- Employee Training Hours related to safety and machine operation
- Absenteeism Rate
- Employee Turnover Rate
Customer Satisfaction KPIs:
- On-Time Delivery of finished cartons
- Order Fill Rate
- Customer Complaints related to packaging quality or delivery issues
- Net Promoter Score (NPS)
Environmental and Sustainability KPIs:
- Fossil Fuel Reliance
- Total Material usage
- End-of-Life treatment
- Carbon Footprint
- Material Circularity
Compliance KPIs:
- Mean time to issue discovery
- Mean time to issue resolution
- Compliance expense per issue
- Average cost of compliance-related lawsuits
- Total regulatory compliance expense
- Post Audit Issues Outstanding
Choosing the Right KPIs
In the dynamic world of packaging, there's a multitude of KPI choices at your disposal. Start by clearly defining the objectives your manufacturing business --both short and long term—that your company aspires to achieve. Once your objectives are crystal clear, break them down into smaller actionable goals. These objectives could include increasing production efficiency, reducing waste, improving quality control, or expanding your customer base.
Additional resources for choosing KPIs:
- https://nicolasboucher.online/category/kpis/
- https://flevy.com/kpi-library
- https://www.industrialpackaging.com/blog/top-10-packaging-line-kpis
- https://www.brightgauge.com/blog/quick-guide-to-11-types-of-kpis
- https://www.cfoselections.com/perspective/manufacturing-kpis-to-track-operational-excellence
Will these KPIs genuinely propel you towards your goals?
It’s not enough to list the KPI and your collection of data for 3 months. The best KPI choices are directly connected to organizational goals. For example, if your goal is to increase production efficiency over three months, your key results could be reducing setup time by 20% or improving equipment uptime by 10% and you would be monitoring the KPI of set up time and equipment uptime amount.
The second important aspect of this question is whether you own the tools to accurately collect the data for KPI. An MIS/ERP streamlines the process of collecting and managing data for KPIs by centralizing information, automating data collection and facilitating real-time access. In addition to the data portion of an MIS/ERP, it provides configurable dashboards that allow visual representation of data at the user’s fingertips.
The KPI dashboard
One way to communicate those insights visually is through a KPI dashboard.
A well-designed KPI dashboard serves as a central hub for monitoring and managing organizational performance, promoting data-driven decision-making, and fostering transparency across different levels of the organization. It provides a visual and easily digestible representation of complex data, enabling stakeholders to quickly grasp the status of key metrics and take timely actions.
Types of Dashboards
Strategic dashboards
- Provides a view of the entire business
- Gives an overview of current state, opportunities and weaknesses
Operational dashboards
- Divides the business into departments
- Provides day-to-day operations snapshot in real time
- Large amounts of data available for analyis
Analytic dashboards
- KPI reports
- Offers insights into trends
- Compares past and present performance using historical data
The dashboards in an ERP/MIS system allow users to organize, filter, drill down, analyze and visualize their most important key targets. The alternative? Wading through Excel sheets of data and other non-curated, unfiltered datasets.
The data is sourced from multiple modules within the ERP/MIS system, from sales, to production to warehouse to quality control. ERPs break down silos by collecting cross-functional data. This is crucial for generating comprehensive KPIs that reflect the overall performance of the organization. ERPs capture data as part of the natural workflow, capturing critical information automatically as transactions occur. ERPs can generate exception reports, highlighting instances where KPIs deviate from expected values. This helps users focus on areas that require attention. ERPs facilitate the comparison of current KPIs with historical benchmarks or industry standards, providing context for performance evaluations.
Conclusion
Finally, ERPs integrate with Business Intelligence tools, enhancing the capabilities for advanced analytics and reporting. This integration supports in-depth analysis of KPIs for strategic decision-making.
Presenting KPIs in dashboards that can be immediately actionable and aligned with the operational pulse of your company can ensure that your packaging manufacturing business stays on track, identify areas that need improvement and drive changes. The consequences of failing to monitor KPIs can be impactful on a business.
Embark on the KPI journey and pursue strategic objectives with the nimbleness of a sophisticated MIS/ERP – the magic awaits.
Comments (0)
This post does not have any comments. Be the first to leave a comment below.
Featured Product
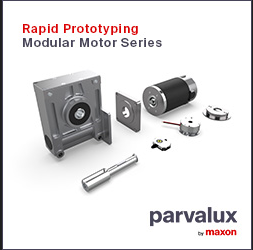