Beyond Noise: The 5 Benefits of Acoustic and Vibration Analysis
Introduction
Random vibrations and acoustic signals reverberate everywhere around us, and most of the time, we treat them as just noise. However, identifying and monitoring some of this “noise” can be beneficial. For example, the acoustic signals of mechanical machines driving critical processes such as industrial water pumps, huge compressors, large rotary equipment, turbines, and conveyor systems can provide clues to downtime. Some dynamic mechanical signals are measurable in the form of tensile, compression, and torsional forces that can have the potential signs of failure. They include the dynamic forces that occur on the main structures of a bridge, the warping changes on the wings of an airplane while flying through air turbulence, or the torsion stress of a suspension bar in a car while driving.
Measuring these signals can also provide insights into the signature behavior of a stationary random vibration. A stationary random vibration signal usually has stochastic properties that remain constant over time — for example, the frequency of ball bearings in a rotary machine. If we know the good behavior of a stationary random vibration, we can analyze and understand the random vibrations of a rotary machine that is wearing down over time and predict its failure.
Benefits of Acoustic and Vibration Analysis
Acoustic and vibration analysis is a measurement science that provides industries with a variety of benefits, including improved reliability and safety, cost savings, and enhanced overall operational efficiency. Here are five key benefits that acoustic and vibration analysis provide engineers and designers.
1. Early fault detection and diagnosis
Using acoustic and vibration analysis for early fault detection and diagnosis has advanced in recent years to incorporate artificial intelligence and machine learning (AI / ML) to predict industrial machinery failures. Hence, it prevents unplanned downtime and damage to expensive equipment. Figure 1 is a high-level model of an early fault detection and diagnostic system.[1]
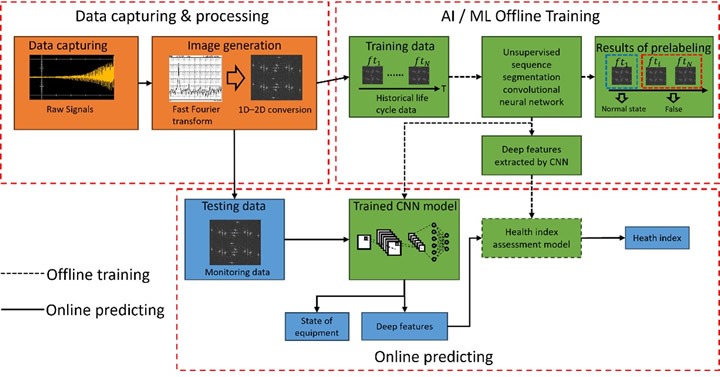
Figure 1. AI / ML approach to training and predicting early fault detection system
2. Reliability and safety
When product design cycles incorporate acoustic and vibration analysis, design and development engineers gain a wealth of physical dynamic parameters. This information helps them make decisions that affect product reliability and safety, such as validating the dynamic stresses of turbine blades, predicting wear and tear of ball bearings, mechanical shaft coupling performance, and torsional rigidity of an automobile body.
3. Less system and operation downtime
Unplanned systems and operation downtime can be costly. For example, downtime at an automobile manufacturing plant can cost about $2 million per hour.[2] Studying the historical acoustic and vibration analysis trends of manufacturing plant machinery can help you determine a lifecycle breakdown of parts and create a preplanned maintenance cadence.
4. Efficiency and cost savings
Acoustic and vibration analysis of critical mechanical rotary or moving parts can provide cost savings through what is known as condition monitoring and predictive maintenance. This process avoids unplanned downtime, minimizes repair costs, and extends the lifespan of equipment. Acoustic and vibration analysis can also help identify weaknesses in mechanical machinery. Finding ways to fix machinery’s weak points can improve performance and efficiency.
5. Better quality products
Most automobile manufacturers conduct noise, vibration, and harshness (NVH) tests. The less NVH transmitted into the passenger cabin, the better the driving experience. Drivers and passengers usually perceive cars with lower NVH as better designed and of higher quality.
NVH also finds end-user applications in the aerospace and defense industries. The areas of interest are recording flight structural dynamics and cabin and jet engine acoustic noise analysis.[3] For example, when a fighter plane makes an extreme maneuver, the pilot and plane experience high g-forces. Jet engines are extremely loud and can be unbearable to pilots if jet noise is not reduced during the design phase.[4]
How to Monitor, Capture, and Analyze Dynamic Signals
The increased need for acoustic noise and vibration analysis is leading to the development of data acquisition (DAQ) systems that can serve as universal multichannel sensor monitoring and data logging devices. Such systems combine features like synchronous multichannel digitizers, frequency domain analyzers using fast Fourier transform, and low-level-bandwidth real-time oscilloscope capabilities. Figure 2 shows a 3D waterfall chart of a frequency domain vibration signature in a rotary system derived from a periodic sampling of vibration signals from the rotary system transformed into frequency domain data in real time.
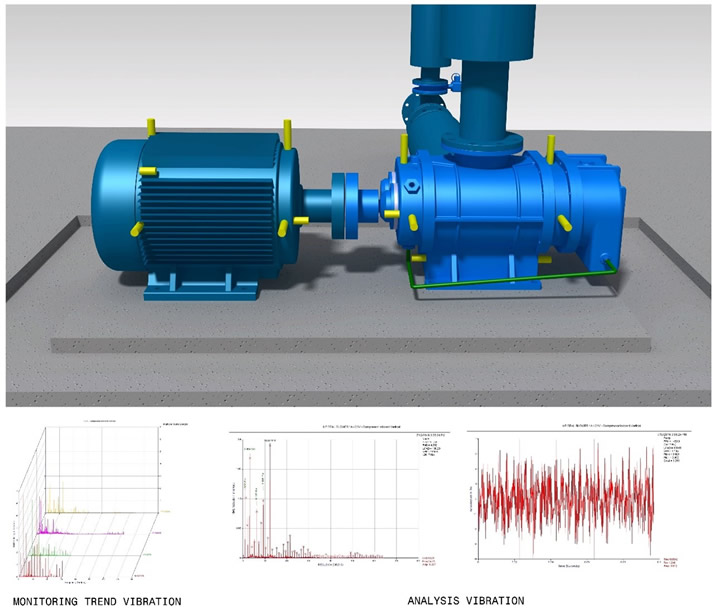
Figure 2. Condition monitoring of a rotary system
A variety of sensors are available to monitor, capture, and analyze dynamic signals of an acoustic nature. They range from simple and crude piezoelectric sensors to highly reliable and accurate industrial sensors that comply with Integrated Electronics Piezo-Electric (IEPE) standards. An IEPE-compliant sensor with a built-in preamplifier eliminates the need for a standalone preamplifier and its associated wiring and costs.
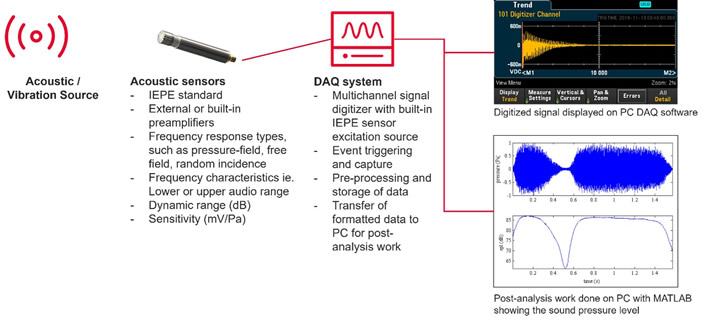
Figure 3. Acoustic and vibration measurement diagram
Figure 3 shows the basic requirements of an acoustic and vibration measurement setup, including a set of industrial-compliant sensors or multiple sets of sensors and a DAQ system that supports IEPE sensors. Such DAQ systems provide constant current power directly to the source.
DAQ systems can also provide event triggers for capturing dynamic data, preprocessing and storing data, and transferring formatted data to a PC for post-analysis work. Most modern DAQ systems come with DAQ PC application software that can control a single system or multiple DAQ systems with many sensors, depending on the capacity and scalability of the hardware. The software can configure all the sensors and DAQ systems directly from a PC. It can also monitor and capture all the sensor output signals and display them on graphical charts on a PC monitor. Formatting and exporting the captured data enables post-analysis work using MATLAB or any statistical data analysis software.
Summary
The benefits of obtaining insights through acoustic and vibration analysis are enormous. They include early fault detection to improve reliability and safety, the ability to avoid unplanned operational downtime, greater efficiency and cost savings, and better quality products.
Selecting the right sensors and DAQ systems is essential. Ensure your DAQ systems provide the flexibility, compatibility, and performance to meet the most demanding requirements.
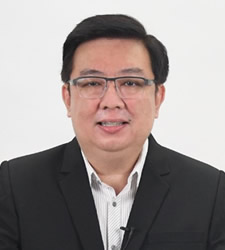
Bernard Ang
Product Marketing Manager
Keysight Technologies
Bernard Ang has been with Keysight Technologies (previously Hewlett Packard and Agilent Technologies) for more than 30 years. Bernard held roles in manufacturing test engineering, product engineering, product line management, product development management, product support management, and product marketing. He is currently a product marketer focusing on data acquisition systems, digital multimeters, and education product solutions. Bernard received his Bachelor of Electrical Engineering from Southern Illinois University, Carbondale, Illinois.
References:
[1] Song, Wenbin, Weiming Shen, Liang Gao, and Xinyu Li. “An Early Fault Detection Method of Rotating Machines Based on Unsupervised Sequence Segmentation Convolutional Neural Network.” IEEE Transactions on Instrumentation and Measurement 71 (2022), 1-12. doi:10.1109/tim.2021.3132989.
[2] “Cost of Downtime in Manufacturing: Insights & Implications.” Evocon. Last modified November 21, 2023. https://evocon.com/articles/cost-of-downtime-in-manufacturing-insights-implications/.
[3] Global Noise, Vibration and Harshness (NVH) Testing Market, Forecast to 2024. Frost & Sullivan, 2020. https://store.frost.com/global-noise-vibration-and-harshness-nvh-testing-market-forecast-to-2024.html.
[4] Bharath, Y.K., G. Chitralekha, S. Veena, H. Lokesha, K.V. Nagalakshmi, and U. Dilna. “Robust Active Noise Control System for Fighter Aircraft Pilot Helmet Application.” Procedia Computer Science 89 (2016), 690-699. doi:10.1016/j.procs.2016.06.037.
Comments (0)
This post does not have any comments. Be the first to leave a comment below.
Featured Product
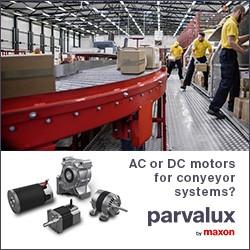
Parvalux by maxon - AC or DC electric motors for conveyor systems?
The material handling industry uses conveyors to ensure that products are distributed effectively, AC or DC motors are chosen depending on the weight it needs to carry and the speed at which it needs to work. Learn which type of conveyor motor might be best for your application and how Parvalux can help you select a geared motor from stock or create a fully custom design.