How XR is Accelerating Digital Twin Technology for Global Machine Hardware Manufacturers
Manufacturing has embraced digital and virtual tools to improve training, maintenance and remote support, and the benefits are evident. Emerging around 2002, digital twins quickly became indispensable for end-to-end digital processes in the industrial value chain.
Digital twins provide a virtual representation of a physical product or process, allowing for the understanding and prediction of the performance characteristics of their physical counterparts. Employed throughout the manufacturing lifecycle, digital twins simulate, anticipate, and optimize products and manufacturing systems before investments are made in physical prototypes and equipment.
When extended to design and manufacturing, digital twins facilitate smoother collaboration between teams, speeding up the design process and minimizing response times. They also help to bypass expensive infrastructure investments, making them a cost effective way to address the industry’s challenges around high-cost architecture.
How is XR Improving Digital Twins?
Extended Reality or ‘XR’ is an umbrella term for Virtual Reality (VR) and Augmented Reality (AR). While digital twin technology has always helped to bridge the gap between virtual and physical realms, XR extends its capabilities several steps further.
First, here’s a bit of background on the technologies. Both VR and AR are helpful in an industrial context. VR is ‘total immersion’ in a virtual environment, and with AR you can integrate virtual objects in physical surroundings.
With VR, companies can, for example, visualize the digital twin of a full shop floor, or do a virtual inspection.
With AR, companies can do things such as visualizing a machine or larger installations on site to check if it fits in the real environment. Using AR, engineers and industrial designers can visualize 3D CAD models in their original size as holograms via AR glasses, to merge these models with real components and to edit them in a real environment – at the target location. By bringing virtual content into reality, the software bridges the gap between virtual planning and what is ultimately real.
By providing true 3D perception via XR apps, engineers can see and interact with objects at their correct size and scale. Unlike traditional 2D screens, XR immerses users in a three-dimensional environment, enhancing spatial understanding and providing a realistic integration of virtual objects with physical surroundings.
The Challenges of Industrial 3D Data
While the benefits of digital twins and XR are evident, it’s important to remember that manufacturing and engineering place high demands on the visualization of digital twins due to the size and complexity of the data models used.
Digital twins must be comprehensive representations of their physical counterparts, which introduces several new demands on computing power. Visual quality is also paramount: when you have to visualize models, such as prototypes, you need to work with the original CAD files, and they need to be displayed at their actual size, with the same level of detail.
In looking at a hologram, engineers may want to extract individual components from the full-scale model, use x-ray mode and other features to gain greater insight, take measurements, and make annotations. In multi-user sessions, it’s likely that they’ll want to collaborate with others on the same model in real-time, at distributed locations globally.
These are big demands, and poor visual quality or delays to image rendering can introduce inefficiencies, inaccuracy, and risk across the entire manufacturing lifecycle.
It’s also a big time drain: visualizing large and complex machines in detail in 3D can involve time-consuming data preparation or conversion. The limited performance of XR mobile devices and the effort required to prepare data are significant challenges for XR developers and users. Manufacturers often struggle with the quality of content in XR and the security of sensitive data stored on the XR device.
This is where XR streaming technology comes in, offering the power to effectively visualize digital twins in real-time.
How is XR Streaming Helping Digital Twins?
As the demand for digital twins and XR applications increases in manufacturing, companies are looking to XR streaming to ensure high-fidelity visuals, high performance, and high security.
Using XR streaming, manufacturers can stream high quality XR experiences from local servers as well as cloud infrastructures to their XR devices. They can build XR apps which can be hosted in the cloud or on a local server. The advantage is that all the heavy processing is now done by a much more powerful computer, and companies can experience their XR applications at the highest quality.
Using XR streaming, augmented and virtual reality apps do not run on the devices themselves but on a local server or the cloud, ensuring high-quality data visualization. When streaming from a local server to an end device, companies can ensure data is protected by centrally managed security measures, reducing the risk of data theft or unauthorized access to sensitive information.
The Future is Here: Centralizing Apps and Streaming
The XR ecosystem is evolving, and XR streaming technology is only one component of the bigger picture. Most manufacturers want to use various XR apps and today, XR platforms are emerging that handle streaming and host apps. These offer manufactures a library of apps that address enterprise-level use cases such as design and engineering, training, remote assistance, and front-line worker support.
Companies can host all their XR applications on a single platform and stream them directly to all connected end users on XR devices. A centralized managed infrastructure also supports resource management, user management, security, and PLM connectors.
These platforms can also work across different XR devices, including both AR and VR hardware. This cross-device compatibility provides flexibility for enterprises and helps future-proof XR investments. Given the fragmented nature of the XR hardware market and uncertainty about the future of certain devices (like HoloLens), the ability to easily switch between different hardware options is seen as a significant advantage.
The platform approach means that as the use cases for the technology grows, companies can look to one platform to simplify the distribution and management of XR applications. In utitlizing a centralized infrastructure that supports innovation and collaboration, manufacturers are primed to make the most of digital twins, enhancing operational efficiency and also driving sustainable practices across the industry.
The synergy between digital twins and XR platforms will continue to improve and evolve over time, opening up new use cases in global machine hardware manufacturing. More and more, manufacturers are recognizing the power of XR streaming to address the demands of visualizing complex industrial data, ensuring high-fidelity visuals and robust data security by using powerful servers for processing. The combination of digital twins and XR will continue to optimize processes and foster sustainable practices, transforming the manufacturing landscape for the better.
Comments (0)
This post does not have any comments. Be the first to leave a comment below.
Featured Product
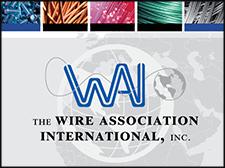