The New Wave of Energy-Saving Pneumatic Systems
Industrial companies are taking bold strides to make their operations greener. One critical element that has been traditionally overlooked in this endeavor is inefficient pneumatic systems. Conventional air compression setups are notorious for their energy-intensive nature, with significant air wastage leading to higher operational expenses and environmental impact.
The emergence of advanced energy-saving technologies is revolutionizing the industry by addressing these long-standing challenges and paving the way for a more sustainable future.
Cost and Carbon Footprint Considerations
Compressed air generation accounts for up to 30% of a facility’s electricity spending, considerably impacting operating costs and sustainability. Unless the plant has invested in renewables and carbon capture technologies, this energy likely comes from fossil fuel sources, increasing the overall carbon footprint.
Embracing energy-saving technologies is essential to lowering overheads and reducing the ecological impact of everyday industrial applications. It’s also crucial to meeting decarbonization goals.
The Rise of Efficient Air Compression Systems
Innovations in key pneumatics components drive significant improvements in energy consumption and operational efficiency.
Variable Speed Compressors
Conventional fixed-speed compressors are a huge energy drain because they deliver a constant supply of compressed air even when not needed. Variable-speed drive models directly address this inefficiency by automatically adjusting the compressor's operating speed to match demand in real time. This technology can reduce energy consumption by up to 35%, effectively lowering running costs.
Ultrasonic Leak Detectors
Compressed air lost through leaks can greatly impact energy efficiency, as the system has to work harder to compensate for the supply variance. It’s estimated that up to 30% of compressed air is lost due to leaks in older, inefficient systems, creating waste and using more electricity than necessary.
Ultrasonic leak detectors provide an effective and accurate way to identify seepages in a pneumatic system. They come in kits featuring directional microphones, amplifiers and audio filters to pick up the high-frequency signal from the leak, allowing operators to localize the source quickly. Modern air compression systems may soon feature integrated ultrasonic detectors as technology advances.
Exhausted Air Reuse
Recycling air expelled from compressors is showing great promise as an energy-saving method. Studies show it can increase efficiency by up to 54.1% under ideal conditions. Advanced valve systems are at the heart of this transformation, allowing for precise airflow control and reducing unnecessary energy consumption.
An earlier field test used bypass valves to connect the pneumatic system’s cylinder inlet and the exhaust chamber to capture compressed air for reuse. This approach resulted in 12%–28% energy savings. Building on that, another study integrated a pulse width modulation controller, which ramped up the energy saved to 30%. Future research may see even higher efficiency levels.
Boosting Energy Efficiency in Existing Pneumatic Systems
Industrial air compressors can cost thousands of dollars in capital investment, so replacing existing systems with energy-saving models is not always viable. Improving operational efficiency is the more practical option until funding allows replacement. Some of the best methods for boosting efficiency include:
- Optimized compressor operations: Optimization involves restricting artificial demand to ensure the pneumatic system only supplies pressurized air as needed.
- Pressure control: Matching pressure to the intended output is vital for minimizing air wastage — and system operating costs by extension. Conservative estimates show decreasing the pressure by 2 pounds per square inch gauge can save 1.6% in running overheads.
- Filter replacements: Clogged filters impede proper airflow, significantly impacting optimal supply and increasing the risk of system damage. Cleaning or replacing these items is a low-cost way to maximize efficiency and prolong the life expectancy of pneumatic devices.
- Denser air intake: As air density increases, so does its pressure — meaning less energy is required for compression. Cold air is denser than warm air, making it a more effective agent for energy-saving compression.
Achieve Enhanced Pneumatic System Efficiency
As industries look to adopt more environmentally friendly practices, addressing energy waste in inefficient air compression systems will be critical. With newer, power-saving technologies becoming more ubiquitous, the focus must be on seamlessly integrating them into existing operations to lower carbon emissions and working expenses.
Comments (0)
This post does not have any comments. Be the first to leave a comment below.
Featured Product
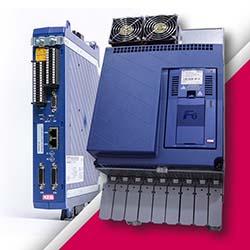