Gen Z and Robotics: Redefining Manufacturing for the Digital Age
Gen Z: The New Face of Manufacturing
The manufacturing world is evolving rapidly, moving beyond traditional automation and assembly lines. As experienced workers retire and labor shortages persist, a new generation -Gen Z- is stepping up to reshape the often-perceived static industry.
Modern factory floors are slowly starting to become high-tech environments where workers collaborate with advanced software and robotics. This integration of robotics and artificial intelligence (AI) represents an exciting convergence of digital skills and physical production, offering Gen Z the opportunity to work with cutting-edge technology while enjoying job security and competitive wages.
Attracting and retaining Gen Z talent
To attract and retain Gen Z talent, manufacturers must address several key generational preferences:
- Meaningful Work - Gen Z seeks roles where they can see the direct impact of their efforts. In manufacturing, the tangible nature of production naturally aligns with this desire.
- Workplace Flexibility - While manufacturing often requires on-site presence, some organizations are exploring ways to offer more flexible scheduling desired by younger generations and eliminate unnecessarily long shifts. With technology like remote monitoring, users are able to remotely operate and monitor industrial robots and react to events happening on factory floors in real-time.
- Career Development - The industry is investing in skills development programs combining hands-on experience with digital learning methods to equip Gen Z for long-term success.
- Collaborative Environment - Implementing advanced communications tools allows this next generation to have seamless interaction among all levels of the organization.
- Sustainability and Purpose-Driven Work - Gen Z is deeply concerned about environmental issues and seeks employers committed to sustainability. By addressing these preferences and emphasizing eco-friendly practices, manufacturers can create a dynamic and efficient workplace that appeals to all employees - especially younger generations.
Embracing AI and robotics
Gen Z’s enthusiasm for AI and robotics in manufacturing challenges the popular belief that these technologies deter young workers. Instead, they view these technologies as enhancing job security rather than threatening it. They see robots as collaborators that supplement their capabilities - not as replacements. This perspective is reshaping the narrative around manufacturing careers.
Challenges and opportunities
The integration of robotics and the influx of Gen Z workers present opportunities and challenges. Manufacturers must bridge the skills gap between traditional manufacturing processes and new technologies. They also need to address the expectations of young workers who might initially be unsure about long-term commitments to manufacturing roles. Another crucial consideration is balancing the need for experienced workers with the desire to bring in fresh talent. Successfully navigating these challenges can lead to significant gains.
The manufacturing industry’s embrace of robotics and advanced technologies aligns with Gen Z’s aspirations and skills. By offering high-tech environments, meaningful work, and growth opportunities, the industry is positioning itself as an attractive career destination for young professionals.
The transformation of manufacturing and the influx of Gen Z talent is creating a dynamic, innovative industry poised for significant growth and technological advancement. As more young workers discover the opportunities in modern manufacturing, the sector is set to overcome its labor challenges and lead the next wave of modernization.
Comments (0)
This post does not have any comments. Be the first to leave a comment below.
Featured Product
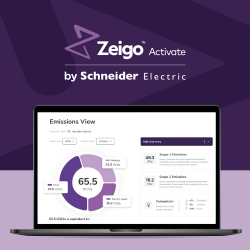