Integrating the loading process for 100% end-of-line automation
Despite acknowledging the need for end-of-line automation, many manufacturers are yet to unlock its full potential. Stubborn organisational silos – both within the company and in partnerships with third-party logistics (3PL) providers – can prevent the automation of important cross-functional processes, such as the loading and unloading of trailers. The challenge lies in creating a seamless operation that maximises the return on technology investments while leveraging the valuable (and scarce) specialist expertise of employees. Wouter Satijn, Sales Director, Joloda Hydraroll, says companies can overcome silos in the loading bay while ‘keeping their aces in the right places’.
Automation in the factory is no longer a futuristic concept. Automating processes such as picking, packing, and handling of raw materials has demonstrated sizeable gains in efficiency and accuracy, which companies are now looking to achieve at every stage of their supply chain as part of one seamless workflow. End-of-line is no exception. Automating end-of-line processes ensures finished products are delivered into the distribution channel efficiently and cost-effectively. Yet, one crucial stage of this is often overlooked: the loading process.
Efficiently loading and unloading goods from trailers can lead to faster, safer, and more reliable transportation between factories and warehouses or distribution centres. However, while a range of loading solutions exist to complete end-of-line automation, many companies have yet to implement them. Loading areas represent a convergence point between production, warehouse, and transportation: a greater focus on cross-functional collaboration would help companies – and their employees – identify and maximise the benefits of supply chain automation.
End-to-end automation
One of the main reasons for supply chain automation is to achieve a more interconnected operation. The warehouse must be connected to the factory, and this integrated system must extend to seamless loading of products onto the trailers. This requires not only physical automation but also the digitalisation of the entire factory and warehouse to ensure comprehensive monitoring. Extending automation to the loading process is an integral part of this, as it is the touch point between the factory, trailer, and warehouse.
Introducing automation to the loading and/ or unloading process significantly reduces loading times, allowing for quicker turnaround and increased throughput. Automated loading systems minimise human error, ensuring that products are loaded correctly and efficiently while improving overall workplace safety, all of which can translate into significant cost and resource savings.
However, realising these benefits requires multiple functions to collaborate on implementing shared processes and technologies. For example, production and warehouse teams must work together to integrate automated solutions throughout the supply chain. After all, a company undermines the benefits of an automated factory if a fleet of forklift trucks is still needed to load products onto trailers manually.
The trouble is that creating cross-functional teams can be met with resistance, perpetuating stubborn silos that can hinder growth.
Overcoming silos
Cross-functional collaboration can be difficult to achieve for several reasons. If not managed correctly, sharing knowledge among teams can lead to negative experiences, such as slow decision-making, which will discourage future discussion. Additionally, knowledge is a valuable asset for employees, and there may be concerns about diluting expertise or reallocating talent away from their best-performing areas. However, greater collaboration between functions doesn’t mean diminishing expertise. In fact, by working together to automate workflows between functions, teams should be able to re-focus more attention on their own functions and specialisms.
External silos between manufacturers and their 3PL providers can further complicate matters. 3PL partnerships are critical to uphold successful end-of-line processes. However, manufacturers often hesitate to suggest alternative solutions to their 3PL partner because they do not own the trailer fleet. The reality is that 3PLs are willing to invest in their long-term partners as it will result in greater efficiencies for both parties – even if it means modifying the trailer fleet. For instance, we’ve worked with several businesses that use their 3PL provider to source, modify and manage the logistics operation. An example of this is MM Packaging at its site in Deeside, UK, where the company has subcontracted Farrells Group to own, manage, run and maintain its logistics operation.
Another consideration is that, as companies look to reduce costs and minimise their carbon footprints, the need for interconnectivity among all logistics companies is set to increase. Working with specialist 3PLs who can help companies apply the right technologies to pool resources – for example, if two companies are making the same trip or if one trailer is only half-full – can add greater efficiencies and sustainability across multiple supply chain operations.
Common goal
An automated loading process is about more than efficiency gains and even ROI. For many companies, it is simply about ensuring high volumes can still leave the factory as quickly as possible. Factories often operate in older buildings, some of which have been in use for centuries. Over time, the production demands within these facilities have significantly increased. Where a factory might have once produced 30 pallets per hour fifty years ago, the same factory must now handle 200 pallets per hour. This increase in capacity is only made feasible through automation.
Given the persistent labour and skills shortage across the supply chain, automated processes can also help provide the existing workforce with the support they need to thrive and grow in their specialist areas. With automated loading, factories can unlock more space by reducing the need for large equipment like forklifts, while operating with fewer personnel. A more efficient process also reduces the number of trucks that are required to complete shuttle runs or deliveries to customer warehouses, as well as truck waiting times at the facility.
Conclusion
Complete end-of-line automation that includes the loading and/ or unloading process offers increased efficiency, cost and space savings, enhanced safety, scalability, and more. However, achieving these benefits means overcoming structural silos. Companies and their employees can unlock the full benefits of a fully automated supply chain by encouraging cross-functional collaboration that encompasses the factory, warehouse and distribution, including 3PL partnerships.
Joloda Hydraroll is a one-stop-shop provider of loading solutions for handling all types of freight, including pallets, air cargo and parcels. Our story has unfolded over 60 years and we are now regarded as the global leader in loading solutions.
We help businesses make loading and unloading processes more efficient and effective with manual, semi-automated, and fully automated solutions. All our systems are backed with ongoing maintenance support that includes reactive breakdown, Pre-Planned Maintenance (PPM), and complete asset management services to minimise downtime.
Our status is demonstrated by our proven and trusted technologies; we have in operation more than 1,000 automated loading systems and 500,000 manual loading systems, with a maintenance team of more than 100 engineers worldwide. We have offices on four continents and an unrivalled global network of over 35 local sales and support partners
Comments (0)
This post does not have any comments. Be the first to leave a comment below.
Featured Product
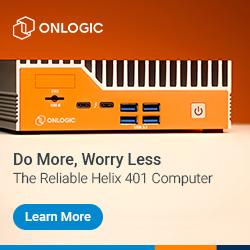