A Slow-Changing Industry in a Fast-Changing World: Manufacturing’s Path to Survival
As 2025 approaches, it’s clear that the old-school manufacturing playbook is dead weight. The industry’s slow adaptation to new tech and comfort in outdated practices isn’t cutting it anymore. Labor shortages, productivity problems, and a constantly shifting political climate are just the start. If manufacturers want to stay in the game, they can’t keep dragging their feet—they need to get serious about innovation, now.
2024 showed us how many manufacturers are still stuck in the past, relying on legacy solutions while missing out on the real power of automation and advanced tech. Sure, some of the latest tools are still in their infancy, but waiting to embrace them is a mistake. To stay relevant and meet future demands, manufacturers need to start adopting these tools yesterday, even if they’re just dipping their toes in.
Top Challenges in 2024
Productivity and quality control remained top issues in 2024, highlighted by high-profile cases like Boeing’s quality control mishaps. This reflects a broader challenge across the manufacturing sector, as many companies, regardless of size, lack systems to identify and address errors, defects, and mistakes as they happen on the assembly line. Without stronger government regulatory oversight, the manufacturing industry may continue to struggle with systemic quality control challenges. This is all the more reason to embrace digital adoption. The longer they hold off implementing basic tools, the more they risk wasting time and money—or civilian lives.
Labor shortages also plagued manufacturing the past year, threatening productivity and profitability. While manufacturing jobs have reportedly rebounded to pre-pandemic levels, skilled labor remains difficult to attract and retain. Gen Z employees, the emerging majority workforce demographic, are looking for roles that offer digitally centered, engaging, and modern work environments that provide opportunities for growth. A 2023 Deloitte survey found that 60 percent of Gen Z want to work for companies with progressive, digital-first cultures. The manufacturing sector, still stuck in its analog past, faces an existential crisis now that its pinnacle Baby Boomer workforce begins to retire and Gen Zs lack interest in a career in manufacturing.
To fix this, manufacturers need to overhaul their workspaces, embrace digital tools, and rethink their training programs. Traditional, paper-based operations aren’t going to cut it anymore—Gen Z expects digital, interactive training that mirrors their everyday experiences with technology. To be successful, training initiatives must integrate user-friendly, digital technologies such as videos, touch screens, and real-time task guidance. These tools not only enhance learning but align with the digital tools Gen Z uses daily. If manufacturers don’t get this right, they’ll be stuck with an aging workforce, or, eventually, no workforce.
Looking Ahead to 2025
Several emerging trends are set to shape the manufacturing landscape in 2025, with recent political developments in the U.S. likely to play a big role. President-elect Trump’s second term could mean more tax breaks, deregulation, and strategic trade agreements, which might help U.S. manufacturing in the short term. In his first term, the Tax Cuts and Jobs Act lowered the corporate tax rate to 21 percent and allowed immediate expensing for capital investments, fueling industry growth and optimism. Additionally, the Trump administration's efforts to reduce regulatory burdens and finalize the United States-Mexico-Canada Agreement provided manufacturers with more stable and favorable conditions. While these political shifts may either support or challenge manufacturing growth in the coming years, it’s clear that businesses shouldn’t wait around for government action to save them.
However, one government initiative to watch closely is the upcoming EU Digital Product Passport (DPP) legislation. By 2026, every product sold in the EU will be required to have a digital record that details everything from its origin to its environmental impact. The DPP is all about value chain transparency and traceability, allowing consumers, investors, and stakeholders to track a product’s every move through the supply chain. While the DPP is still only a potential consideration in the U.S., the case for adopting a similar system is undeniable: better traceability means holding everyone accountable, improving product quality, and building customer trust. Streamlined supply chains will slash costs and fight counterfeiting, and consolidating product data will give U.S. manufacturers a much-needed competitive edge globally. Proactively adopting it doesn’t just prepare manufacturing leaders for future regulations—it helps build trust, impress investors, and set businesses up for long-term success.
Millennials and Gen Z not only expect modern, tech-driven work environments but also prioritize sustainability, seeking to work for companies that demonstrate strong environmental and social commitments. This shift in priorities aligns perfectly with the values of millennials and Gen Zs, who are increasingly stepping into leadership roles. They’re digital natives, and they’ll drive faster adoption of new tools. The speed of change might not be predictable, but it’s coming. Manufacturers who don’t keep up will get left behind.
The manufacturing sector’s success depends on its ability to evolve. As costs of outdated practices rise, competitors in other industries leverage digital innovations to boost efficiency and profitability. To stay competitive globally, manufacturing must adopt modern tools, enhance work environments, and provide effective training to build a skilled, resilient workforce.
As 2025 approaches, it’s time for manufacturers to recognize that the industry’s traditionally cautious pace is no longer an option. If the sector wants to thrive in an increasingly digital world, it must prioritize change now. By fostering a culture of innovation, improving quality control, and addressing labor challenges with modern solutions, manufacturers can secure their place in a fast-moving global economy. The pace of change may be influenced by political and generational shifts, but one truth remains: the future of manufacturing depends on the industry’s willingness to evolve.
Comments (0)
This post does not have any comments. Be the first to leave a comment below.
Featured Product
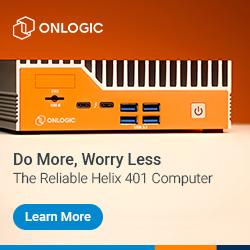