Equal Parts: Assessing the Viability of Large Format Additive Manufacturing
Large-Format Additive Manufacturing continues to demonstrate itself as a revolutionary technology, offering tangible advantages to manufacturers spanning aerospace to automotive, and from construction to design. With the technology by no means a one-size-fits-all solution for manufacturers, Giovanni Avalloneat, Chief Innovation Officer at Caracol looks at why LFAM’s success hinges on understanding where its deployment makes the most sense and which parts are best suited to LFAM.
The potential of Large Format Additive Manufacturing (LFAM) continues to attract the attention of manufacturing companies from a diverse array of sectors. Whether you’re a manufacturer already embracing the technology or still assessing what it could do for you, there a few things to consider when it comes to evaluating the suitability of the technology for specific parts production and which parts could be optimized with LFAM.
These considerations include intended production volumes, geometric complexity, materials, the technical requirements of the whole part, eventual technical advantages, and last but not least, the supply chain and logistics requirements pertaining to the specific part.
Looking at these in turn, when it comes to production volumes, it’s worth remembering that this is a technology that has been developed in order to produce on demand, just-in-time, with specific focus on very complex parts. If you’re looking at mass production with standardized parts, then that scenario is most likely not best-suited to this technology.
Conversely, if you're looking to produce parts on demand with slight changes in customization, in small to medium batches, where the impact cost of your mold on the production of the part is very high, then LFAM could be the solution to your needs. Also, LFAM, especially via robotics, allows you to free up several other axes and tackle parts that are very complex in geometry. When you're looking at parts that have organic shapes, specific geometries where mold making, for example, becomes very difficult, then LFAM might be more cost effective and suitable for that type of part.
Of course, a critical aspect is the need to analyze the specific material requirements for the part in question. This is where your vendor can really help; if they are as established and experienced as they should be, they will be able to work closely with you to assess specific needs and recommend qualified materials that meet the necessary criteria. The right material choice for the particular application needs is critical to ensuring the success of the implementation of LFAM technologies.
Additionally, it's important to understand the compatibility of the single printed material with the eventual post-processing required to complete the part. We know that this is vital, for example, in the marine industry as well as within aerospace, where LFAM is one step in a supply chain where post-processing and its integration with the right material becomes critical for the success of the application.
Obviously, when looking at your parts, one thing to do is an in-depth analysis of the parts’ technical requirements, which is fundamental to determining if a part is suitable for LFAM or not.
Naturally, dimensional tolerances, specific working temperatures of your materials, fire rating requirements, as well as UV and other types of testing, all need to be mapped out to establish whether the part is suitable for LFAM or perhaps an alternative process. This process has several technical advantages and would likely point to LFAM as an option if you’re looking to produce monolithic parts, eradicate assembly (and therefore the possible eventuality of human error as part of that), as well as reduce waste across the process.
When talking about large parts scale, this is a process that of course focuses on parts that are over half a meter, a meter and beyond 20-25 meters. In many cases, you have several parts that are assembled and produced with traditional technologies from which an integrated part is created. It might be that you have some critical requirements that you’re currently not addressing with your existing technical solutions, or at the very least not properly fulfilling or optimizing. Weight is a perfect example.
Last but not least, it's critical to understand the supply chain situation and the lead times required for your parts.
For instance, these parts produced with LFAM do not have very heavy logistics; the technology offers the opportunity to delocalize production close to the point of use and integrate this into a digital supply chain.
Generally speaking, LFAM has a huge potential and we have seen that and appreciate that in industries like aerospace, architecture and construction, automotive, design, marine and transportation. However, an in-depth analysis of the aforementioned elements is a good move to ensuring the most effective and efficient implementation of LFAM technologies within your production workflow. It is therefore worth taking the time to work with your supplier and ensure they guide you into selecting, developing and qualifying the right parts so that ultimately you can successfully internalize and scale your production.
Giovanni Avalloneat is Chief Innovation Officer at Caracol, a provider of an industrial robotic large-format 3D printing/additive manufacturing system that uses polymers and composites to produce advanced components for applications in key industry sectors.
Comments (0)
This post does not have any comments. Be the first to leave a comment below.
Featured Product
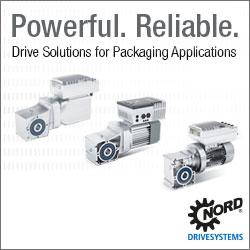