The Role of Technology and Innovations in Polymer and Chemical Manufacturing
Chemical manufacturing is a cornerstone of modern industry, influencing everything from agriculture and healthcare to construction and energy. As the industry grows in complexity and scale, the role of technology in streamlining operations, optimizing resources, and driving innovation has become increasingly critical. From enterprise planning tools such as SAP and ERP systems to advanced analytical instruments like HPLC, GPC, IR, and mass spectroscopy, technology is transforming how chemical manufacturers operate, compete, and deliver value.
In the chemical manufacturing world, efficiency is everything. From sourcing raw materials to delivering finished products, the entire value chain must operate like a well-oiled machine. This is where enterprise resource planning (ERP) systems, such as SAP, come into play. These systems provide manufacturers with an integrated platform to manage and optimize every aspect of their operations.
ERP systems allow chemical manufacturers to forecast demand, schedule production runs, and allocate resources with precision. For instance, SAP's advanced planning capabilities can help manufacturers create data-driven production schedules that reduce waste and improve output. By analyzing historical data and real-time market trends, manufacturers can make informed decisions about inventory levels, raw material procurement, and workforce deployment.
The impact of these tools extends beyond production efficiency. With features like automated reporting and compliance tracking, ERP systems help manufacturers adhere to regulatory standards and minimize the risk of costly errors. Additionally, their ability to integrate with other systems ensures a seamless flow of information across departments, enabling more effective collaboration and decision-making.
The AI Angle: Transforming Chemical Manufacturing
Artificial intelligence is rapidly changing the landscape of chemical manufacturing. AI-powered tools and algorithms are enabling manufacturers to identify inefficiencies, predict equipment failures, and even discover new chemical formulations.
Predictive maintenance is a standout application of AI in this field. By analyzing data from sensors embedded in production equipment, AI can detect patterns that indicate potential issues. This allows manufacturers to perform maintenance before a breakdown occurs, minimizing downtime and reducing maintenance costs. For example, an AI system monitoring a reactor can identify subtle changes in temperature or pressure that may indicate a problem, prompting preemptive action.
AI is also driving advancements in process optimization. Machine learning algorithms can analyze vast amounts of production data to uncover insights that humans might miss. These insights can help manufacturers fine-tune their processes to maximize yield, reduce energy consumption, and lower production costs. Moreover, AI-driven simulations allow manufacturers to test different scenarios virtually, enabling them to optimize their processes without disrupting operations.
Perhaps most excitingly, AI is revolutionizing research and development in chemical manufacturing. Algorithms can analyze millions of chemical combinations to identify promising candidates for new products. This accelerates the innovation process and helps manufacturers stay ahead in a competitive market.
Leveraging Advanced Analytical Instruments for Product Development
Product development is at the heart of chemical manufacturing, and advanced analytical instruments like high-performance liquid chromatography (HPLC) and gel permeation chromatography (GPC) are essential tools in this area. These instruments allow manufacturers to understand the composition, structure, and properties of their products at a molecular level.
HPLC is widely used for separating, identifying, and quantifying components in a chemical mixture. For example, in the production of pharmaceuticals, HPLC can be used to ensure that a drug contains the correct amount of active ingredients and meets stringent quality standards. By providing precise data about a product's chemical composition, HPLC enables manufacturers to maintain consistency and compliance with regulatory requirements.
GPC, on the other hand, is a powerful tool for analyzing polymers. It measures the molecular weight distribution of a polymer sample, which is critical for determining its physical properties and performance. For example, in the production of plastics, GPC can help manufacturers optimize formulations to achieve the desired strength, flexibility, and durability. This ensures that the final product meets both customer expectations and industry standards.
The real value of these instruments lies in their ability to support innovation. By providing detailed insights into chemical properties, HPLC and GPC enable researchers to develop new products with enhanced performance and functionality. Whether it is creating more efficient water treatment chemicals, developing bio-based polymers, or designing specialty adhesives, these tools are indispensable for pushing the boundaries of what is possible in chemical manufacturing.
The Synergy of Technology in Chemical Manufacturing
The true power of technology in chemical manufacturing lies in its ability to bring together disparate processes and systems into a cohesive whole. For example, integrating ERP systems with AI tools and advanced analytical instruments can create a powerful feedback loop. Production data captured by HPLC or GPC can be fed into AI algorithms to identify trends and suggest process improvements. These insights can then be incorporated into ERP systems to refine production schedules and resource allocation.
This synergy not only enhances operational efficiency but also supports strategic decision-making. By providing a holistic view of operations, technology empowers manufacturers to identify growth opportunities, respond to market changes, and deliver better value to their customers.
While the benefits of technology in chemical manufacturing are undeniable, implementing these tools comes with its challenges. High upfront costs, the need for skilled personnel, and the complexity of integrating new technologies with existing systems can be significant barriers. However, these challenges also present opportunities for forward-thinking manufacturers to differentiate themselves.
Investing in training programs can ensure that employees are equipped to work with advanced technologies. Partnering with technology providers can help manufacturers navigate the complexities of implementation and maximize the return on investment. Most importantly, a culture of innovation can enable organizations to embrace change and stay ahead in an increasingly competitive landscape.
The role of technology in chemical manufacturing is more vital than ever. Tools like SAP and ERP systems are streamlining production planning and resource optimization, while AI and advanced analytical instruments are driving innovation and enhancing product development. By embracing these technologies, chemical manufacturers can improve efficiency, reduce costs, and deliver high-quality products that meet the evolving needs of their customers.
As the industry continues to evolve, the companies that leverage technology effectively will be the ones that thrive. By staying ahead of the curve and harnessing the power of innovation, chemical manufacturers can build a sustainable and successful future.
Venkata Manikya Kumar Ajjarapu is a seasoned professional with nearly 30 years of experience in production, quality assurance, research and development, and process improvement within the chemical industry. He has led major initiatives to optimize manufacturing processes, develop innovative products, and enhance operational efficiency, consistently delivering measurable results in cost savings and productivity. Kumar stays informed about the latest technological advancements in the manufacturing industry to enhance process efficiency and drive cost savings.
Comments (0)
This post does not have any comments. Be the first to leave a comment below.
Featured Product
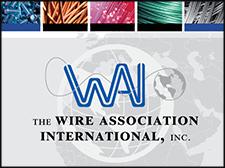