5 Emerging Pain Points in the Manufacturing Supply Chain and How to Preempt Them in 2025
The manufacturing industry has grappled with repeated supply chain disruptions in recent years. While some of the worst effects have subsided, the storm is far from over. Some long-standing pain points will persist or grow throughout 2025, and the year will bring new challenges as well.
Leaders in the industry must recognize these incoming obstacles to prepare for them appropriately. With that in mind, here are five new or evolving threats that will affect manufacturing supply chains in 2025.
1. Tariff Uncertainty
Tariffs, both from the U.S. and against it, are among the most prominent pain points for supply chains this year. Early in 2025, President Trump enacted a 25% tariff on Canadian and Mexican imports and a 10% levy on Chinese imports. While the administration has since delayed the Canadian and Mexican trade penalties, such developments create uncertainty for international shipping.
U.S.-enacted tariffs would raise the cost of importing goods and materials from other nations. Retaliatory actions from foreign countries could limit growth in international markets and raise shipping expenses.
How to Address It
Given the uncertainty around global trade in 2025, manufacturers should prioritize flexibility. Re-shoring may be necessary to minimize the impact of any future import fees. Likewise, diversifying suppliers can offer alternative strategies should some nations become too expensive to source from.
Increasing safety stocks of foreign goods may provide some short-term relief. Supply chain leaders should stay abreast of global policy changes to know when such action may be necessary to increase inventories before tariffs take effect.
2. Cybersecurity Threats
Cybercrime is another significant threat to manufacturing supply chains in 2025. While the industry has encountered difficulty in this area before, cyberattacks against manufacturing facilities and supply chain organizations will likely rise this year.
The manufacturing and industrial sector experienced a staggering 41% of all cyberattacks in the first half of 2024 — more than double its share the year prior. Rising geopolitical tensions may exacerbate this trend by introducing heightened risks from nation-state-backed attackers.
How to Address It
Cybersecurity in 2025 must go beyond internal controls. Manufacturers must also verify the security of their supply chain partners, including all vendors and logistics providers. Ensuring all third parties comply with applicable data privacy regulations — which are becoming increasingly common — should be part of that process.
Large, complex networks are inherently risky and difficult to keep track of, raising the need for zero-trust architecture. Implementing a zero-trust strategy will take time and investment, but it’s a critical step to minimize vulnerabilities and catch potential breaches before they cause much damage.
Automated network monitoring and incident response may also be necessary. Such technologies enable $2.22 million in savings in data breach costs through response times that would be near impossible to achieve manually.
3. Worsening Labor Shortages
As in previous years, labor shortages continue to plague the industry in 2025. While fewer manufacturers cite talent gaps as their largest challenge today than in previous years, it’s still a prominent issue. Increasing reliance on digital technologies may lead to new shortfalls in tech roles.
Proposed tariffs may worsen the state of the supply chain workforce. Although some leaders believe such action can promote domestic job growth, tariffs in prior years led to a 1.4% reduction in manufacturing employment. Tighter immigration controls may also limit the available workforce.
How to Address It
Automation is the industry’s conventional answer to labor shortages. However, not every role is easily automatable. Using a third-party logistics provider (3PL) can help, as 3PLs can provide on-site support to manage staffing so the manufacturer does not need to hire additional workers itself.
Upskilling and reskilling can help in situations where physical roles see less demand but technical ones rise. Equipping current workers with in-demand technological skills helps supply chains capitalize on new technologies without struggling in a highly competitive IT labor market.
4. Extreme Weather Events
Climate change will also prove an issue for manufacturing supply chains. Extreme weather is becoming increasingly common, and such events can disrupt global supply networks in several ways.
In 2023, a drought in Taiwan contributed to semiconductor shortages by restricting the supply of water for cleaning. The past few months have already seen harsh winter weather and wildfires, which can delay shipments, damage factories or reduce the supply of resources stemming mainly from an affected area.
How to Address It
While extreme weather can happen virtually anywhere, some regions are more prone to it than others. Consequently, manufacturers must assess their suppliers to see if any reside in areas of high climate risk and consider finding alternate sources.
Preparing for disruption ahead of time can help mitigate weather-related delays when disasters do occur. Keeping larger safety stocks and diversifying suppliers to avoid single dependencies will help. Long-term sustainability projects are also important to protect future supply chains but will not produce immediate benefits.
5. Material and Component Shortages
Manufacturers should also be aware that demand for limited or region-constrained resources will rise. Electronics are the most heavily affected product category, as minerals like lithium and cobalt can be challenging to source and semiconductor production occurs mostly in East Asia.
Pharmaceuticals and textiles face similar obstacles. Roughly 17% of active pharmaceutical ingredient imports come from China, and for some vitamins, the portion is as high as 75%. Most textiles stem from South Asian nations like Bangladesh. Such proliferation of regional dependencies means heightened demand for any one of these resources will lead to stiff competition and, likely, delays and high costs.
How to Address It
In the long term, manufacturers must invest in alternate sources for high-demand resources, ideally near-shored supplies. However, this is not always possible, and such shifts take time.
A few strategies can mitigate material and component shortages in the near term. The first is to abandon lean strategies in favor of larger safety stocks for items with volatile supply factors. Another is to consider product redesigns to require a lesser amount of supply-constrained resources.
Artificial intelligence (AI) is a helpful tool in this process. AI can help manufacturers pinpoint sources that may increase supply chain risks, highlighting opportunities for restructuring. Alternatively, AI design tools can identify paths to use less of a sensitive material in a given product.
Manufacturing Supply Chains Must Evolve in 2025
The global manufacturing industry is more connected than ever before. While that’s beneficial in many ways, it has also led to risky trends of geographic dependence and vulnerability to geopolitical disruptions. Manufacturers must become aware of these dangers and how they might evolve in the coming years to avoid the worst effects.
These five pain points will likely be among the most significant in 2025. Learning about them and preparing to manage them today will alleviate substantial complications in the future.
Comments (0)
This post does not have any comments. Be the first to leave a comment below.
Featured Product
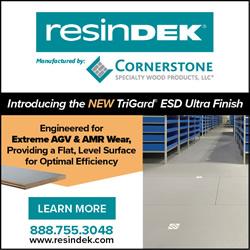