5 Steps to Meet the Growing Demand for Automated Warehouses in 2025
The shift to automated and connected warehouses has intensified as businesses prepare for 2025. Rising consumer expectations and supply chain complexities have placed a premium on efficiency, reliability, and safety. Here are five areas facility managers should prioritize to stay ahead of the curve.
1. Streamline Data Transfer & Visibility
Modern warehouses generate immense amounts of data—from inventory tracking to route optimization. To prevent bottlenecks, invest in high-speed, secure data transfer systems. Hardwired, data-over-power solutions ensure reliable communication even in busy environments, reducing issues like network dropouts and delays.
Data visibility is equally critical. Integrating systems that allow real-time monitoring of warehouse performance enables better decision-making and faster responses to challenges. With seamless data flow, you can improve warehouse accuracy in inventory management, optimize workflow, and enhance customer satisfaction. As more IoT devices become standard, it’s vital to establish a scalable architecture that grows with your needs.
2. Rethink Equipment Power Management
Automated guided vehicles (AGVs) and autonomous mobile robots (AMRs) are essential for modern warehouses but can face operational inefficiencies due to outdated – or inefficient – charging systems. Adopting flexible solutions like wireless or opportunity charging reduces downtime and boosts productivity. By integrating charging into workflow pauses, you maximize uptime without requiring manual intervention.
Consider long-term energy strategies as well. By combining efficient charging systems with renewable energy sources, facilities can reduce operational costs and minimize their environmental footprint.
Optimized power management not only supports your bottom line but also aligns with growing consumer and regulatory demand for sustainable operations.
3. Invest in Proactive Safety Measures
As automation increases, so do the risks associated with shared spaces between humans and machines. Implement proactive safety protocols that include integrated emergency shutdown systems. Conduct safety assessments to address layout risks and worker interactions, ensuring a seamless and safe environment for both humans and machinery.
Collaboration between your workforce and robots should be a central focus. Training employees to work alongside automated systems fosters a culture of safety and efficiency. Advanced safety technologies, such as real-time monitoring and AI-driven incident detection, can further enhance security by identifying and addressing risks before they lead to accidents. Proactive safety measures protect not only your workforce but also the longevity of your automation systems.
Effective cable management is another critical aspect of safety. Automated cable systems reduce hazards caused by tangled or damaged wiring and ensure that essential systems remain operational. Organized cables also simplify maintenance and prevent disruptions caused by unexpected failures, enhancing both safety and uptime.
4. Choose Scalable and Adaptable Solutions
Every warehouse has unique needs. Opt for solutions that can be tailored to your specific operations and scaled as your facility grows. From AGV charging setups to customizable data transfer systems, selecting adaptable technologies minimizes future retrofitting costs and enhances operational flexibility.
A scalable approach to automation allows businesses to start with core functionalities and expand as demand increases. For example, a phased integration of AGVs or AMRs gives you a gradual adoption without overwhelming existing operations. Similarly, investing in scalable software platforms ensures that your warehouse management system remains effective as operations evolve. Flexibility in planning and implementation is key to meeting both current and future demands.
5. Partner with Reliable Equipment Providers
Perhaps most importantly, selecting the right solution partner is essential for meeting the demands of a connected warehouse. Look for providers who offer reliable equipment designed for longevity and adaptability. Vendors with ongoing support services, including regular updates and maintenance, can help ensure that your systems remain operational and effective over time.
Partnerships with experienced providers simplify implementation and prepare your facility to adapt to future industry advancements. By choosing equipment suppliers with a proven track record, you’ll set your business up for success and avoid costly headaches down the line.
Looking Ahead
Facility managers who embrace these steps will position their warehouses to thrive in an era of increasing innovation and automation. By addressing data, power, safety, connectivity, and scalability now, you can confidently meet the rising demands of the modern supply chain. The warehouses that adopt these strategies today will not only meet consumer expectations but set the standard for the industry’s future.
Comments (0)
This post does not have any comments. Be the first to leave a comment below.
Featured Product
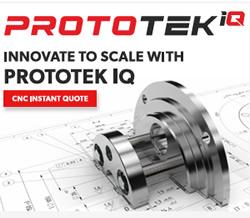