Optimizing Your IT Ecosystem: Is It Time for a Tech Stack Audit?
Summary:
Technology is supposed to make your business run smoother, not create more headaches. But if your systems are slowing you down, creating data chaos, or draining your budget, it’s time for a tech stack audit.
A tech audit can serve as a diagnostic tool, flagging vulnerabilities within your packaging company’s IT infrastructure before they impact the health of your business. Taking a close look at the tech ecosystem can determine whether or not you are ready for the technological revolution in manufacturing led by AI.
Whether you're looking to expand your tech stack to enhance functionality or streamline it to minimize complexity, your decision should be guided by a clear understanding of business priorities. A well-structured technology ecosystem can accelerate time-to-market, strengthen compliance, and align operations with broader strategic goals. ERP systems are the backbone of tech stack consolidation, acting as a single source of truth for essential business data.
What is a tech stack?
A tech stack, also known as a technology stack or solutions stack, is the combination of software, tools, and platforms that a business uses to manage its operations. In packaging manufacturing, a tech stack is essential for streamlining production, optimizing logistics, tracking machine performance, and ensuring quality control. Each layer of a manufacturing tech stack plays a role in efficiently managing raw materials, production workflows, cost tracking, and customer orders.
At its core, a manufacturing tech stack is structured in layers:
Logistics & Supply Chain Management – This foundational layer controls the flow of raw materials, assembly parts, finished products, and storage. Key systems here include Warehouse Management Systems (WMS), Manufacturing Execution Systems (MES), and Industrial IoT (IIoT) solutions that help monitor material movement and optimize supply chain operations.
Production & Machine Monitoring – The next layer focuses on converting raw materials into finished products with the help of automation and real-time monitoring. This includes Incident Management Systems for troubleshooting, Machine Monitoring Data Platforms for performance tracking, and ERP solutions that connect production inputs with managerial decision-making.
Costing & Manufacturing Analytics – The final layer deals with production costs, customer orders, and overall manufacturing intelligence. It involves ERP systems for financial tracking, predictive maintenance software to prevent costly machine failures, and AI-driven analytics to enhance efficiency.
A fully optimized manufacturing tech stack integrates multiple key technologies, including:
✅ ERP (Enterprise Resource Planning) – Centralized control of inventory, orders, financials, and production data.
✅ MES (Manufacturing Execution System) – Real-time monitoring of production lines, work orders, and machine performance.
✅ Industrial IoT Sensors – Tracks production speed, machine downtime, and material usage for predictive maintenance.
✅ SCADA Systems – Supervises and manages data from multiple machines across a factory.
✅ Quality Control Systems – Uses vision systems and barcode/RFID scanning to detect defects and maintain product accuracy.
✅ Supply Chain Visibility Tools – Includes Warehouse Management Systems and cloud-based platforms for real-time tracking and coordination.
Why do a tech stack audit?
Think of it like this—your business is a machine, and your tech stack is the engine. If that engine isn’t optimized, you’re burning fuel inefficiently, losing power, and risking a breakdown.
Here’s how to know when it’s time to lift the hood and take a hard look at your tech stack.
1. Your Systems Don’t Talk to Each Other—And It’s Costing You
If running a report means flipping between multiple disconnected tools, pulling numbers manually, or waiting on different departments to confirm data, your tech stack is working against you.
Ask yourself:
- Do your ERP, MES, and supply chain software sync seamlessly, or are you constantly piecing together fragmented data?
- When comparing reports from different teams, do the numbers match, or does every department tell a different version of the truth?
- Does it take hours instead of minutes to pull critical business insights?
If your tech isn’t integrated, you’re running blind. A well-optimized modular ERP system with an MES ensures real-time visibility and eliminates manual data crunching. If you don’t have that, it’s time to audit your tech stack.
2. Your Tech Can’t Keep Up with Growth
As your business scales, your tech stack needs to scale with it. But not all software is built for expansion. Some have hidden volume restrictions, overage fees, or rigid contract terms that become roadblocks when you need to grow.
Here’s the reality:
🚨 If adding users, processing more orders, or expanding production comes with extra fees or limitations—you’re being held back.
Your ERP and MES should adapt to your needs, not force you into costly upgrades just to keep up. An audit will help you identify which tools are ready for long-term growth and which ones are ticking time bombs.
3. Your Team is Wrestling with Software Instead of Doing Their Jobs
A complex, clunky tech stack doesn’t just slow down operations—it drains productivity.
- How much time does your team waste on manual data entry because systems don’t sync?
- Are employees jumping between multiple platforms just to complete basic tasks?
- Is software training a nightmare because the tools are too complicated?
If your tech isn’t helping your team work smarter, then it’s hurting your bottom line. A tech audit will help streamline your tools, so your employees can focus on high-value work instead of fighting with outdated systems.
4. You’re Not Sure If Your Data Is Even Accurate
Bad data isn’t just an inconvenience—it’s a liability. If you can’t fully trust your automated reports, CRM data, or financial metrics, how can you confidently make business decisions? It is essential that stakeholders know what data they have, where it resides and who is best placed to use it. This requires effectively auditing your data as well as your software, hardware and cloud estates.
Some red flags that your data integrity is at risk:
❌ You still rely on manual data pulls to verify accuracy
❌ Automated reports frequently have errors or discrepancies
❌ Departments operate on conflicting data sets, creating confusion
A properly integrated tech stack ensures that data flows seamlessly across all systems—eliminating manual errors and giving you accurate, real-time insights. If that’s not happening, it’s time for an audit.
5. It’s Been Over a Year Since Your Last Audit
Here’s the simplest rule:
If it’s been more than 12 months since your last tech stack audit, it’s overdue.
Technology moves fast. What worked last year might be outdated today. Without regular audits, you risk:
- Running on inefficient systems that cost more than they save
- Missing out on automation & AI advancements that could be game-changers
- Accumulating unused software costs that bleed your budget
How an Expert Tech Team Can Guide Your Audit
If you’re dealing with data silos, clunky integrations, frustrated employees, wasted software costs, or slow decision-making—an audit of your tech stack can identify where inefficiencies lie.
Conducting a tech stack audit isn’t just about identifying problems—it’s about finding the right path forward. That’s where an experienced tech and development team makes all the difference. At HiFlow Solutions, our team specializes in manufacturing tech optimization, helping you determine whether to streamline, consolidate, or expand your tech stack. We take a deep dive into your ERP, MES, automation tools, software systems and integrations, assessing performance, scalability, and cost-effectiveness. Our experts don’t just diagnose inefficiencies—we provide a strategic roadmap to eliminate bottlenecks, improve data flow, and ensure your systems are built for long-term growth.
A modular ERP + MES system designed for seamless integration, AI-powered automation, and scalability is the key to a high-performance packaging operation. If you’re ready to get more from your technology without the guesswork, HiFlow Solutions is here to help.
Comments (0)
This post does not have any comments. Be the first to leave a comment below.
Featured Product
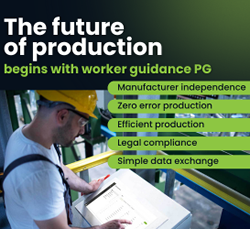