Advances in Preventive Maintenance Are Refining the Manufacturing Supply Chain in 2025
Maintenance is key to a well-functioning supply chain. Vehicles must remain in top condition to streamline shipments, and factory machinery needs regular upkeep to avoid costly downtime. As demands have risen, technology has responded, and manufacturers now have more tools than ever to advance their preventive maintenance strategies.
The need for innovative care and repair technologies grows as uptime and reliability become larger concerns. Recognizing which solutions offer the greatest potential for a facility is the first step to optimizing machinery throughout the supply chain in 2025.
1. IoT Tracking
The Internet of Things (IoT) is one of the most disruptive of these innovations. As of 2023, 62% of global manufacturers had already integrated IoT systems into their workflows, and their potential for maintenance is a critical reason.
IoT sensors provide wirelessly accessible real-time data on equipment health factors. Manufacturers can use this information to monitor machines’ operating conditions without pausing production or traveling to a specific location. Using sensors instead of visual inspections also means some issues may become evident before they are noticeable to human operators.
This technology is not a complete maintenance solution. However, it lays the groundwork for larger changes. Repairs are only effective when organizations know they are necessary, and IoT provides the insight to recognize those situations earlier and more accurately.
2. Predictive Maintenance
Predictive maintenance (PdM) takes IoT tracking to the next level. This increasingly popular practice uses IoT data to train artificial intelligence (AI) models to predict when a machine will need repair based on current data and past trends.
By automating inspections and predicting breakdowns, PdM addresses the primary concerns of schedule-based preventive maintenance and run-to-failure methods. It prevents costly, time-consuming breakdowns by noticing the need for repair while issues are still small. Simultaneously, it minimizes planned downtime by removing the need for manual inspections.
As a result, PdM is more cost-effective than conventional approaches. Studies suggest it can reduce fixed asset downtime by up to 15% and increase vehicle uptime by up to 25 percent. Maintenance costs in both categories fall by as much as 10 percent.
3. Asset Management Software
Even with IoT and PdM, managing upkeep workflows across an entire supply chain can be challenging. Cloud-based asset management platforms make it easier by providing a single point to view, share and react to all relevant data.
Up to 90% of engine failures are preventable, but fleets can only avoid them when they know which vehicles need repair at which times. Fixed assets on factory floors fall into the same situation, especially when applying varying maintenance strategies to different equipment. Cloud management software provides the needed visibility to overcome these obstacles.
IoT sensors can upload real-time data directly to the cloud. Technicians can report the repairs they perform on the same platform. Having all this information in one place enables faster, more informed responses across the supply chain.
4. Augmented Reality
Some manufacturers have begun experimenting with augmented reality (AR) in preventive maintenance workflows. Through specialized glasses or camera feeds, AR superimposes digital visualizations over users’ view of the real world. While it is most popular as an entertainment technology, it can streamline many repair tasks.
AR glasses can show technicians step-by-step instructions to avoid mistakes without needing to stop and open a physical manual. Alternatively, AR can highlight objects of interest or pull up machine blueprints.
While these improvements may seem small, they lead to significant savings. Some employees have been able to complete maintenance tasks 46.8% faster by using AR glasses. These solutions may also streamline training for new hires, accelerating the hiring of a larger maintenance team.
5. 3D Printing
Additive manufacturing — more commonly known as 3D printing — is another niche but impactful advance in preventive maintenance. 3D printing has grown as a method to streamline prototyping and low-volume production, but it can also save time and money on machine upkeep.
When manufacturers or their supply chain partners do not have needed replacement parts on hand, they can print new ones. Doing so removes downtime from waiting on a shipment and prevents related costs. Facilities can even print multiples of frequently replaced components to further streamline maintenance.
As 3D printing has developed, its potential for producing industrial-grade parts has risen. The ability to print in metal and even carbon fiber has made it possible to print entire vehicles, so creating a single component is well within the realm of possibilities.
6. AI-Driven Optimizations
Another maintenance trend manufacturers should pay attention to is the growing use of AI for long-term improvements. As companies gather more data across their factories and supply chains through IoT solutions, they can provide AI with greater sources to generate reliable predictions about future performance.
AI can analyze repair trends to highlight areas where preventive maintenance workflows can improve. Some machine learning models can even simulate various fixes to determine which steps will yield the best results. This way, manufacturers can avoid costly trial and error when optimizing operations.
AI-driven process improvements have already helped some businesses increase output by 15% and reduce emergency response times by 90 percent. Because AI improves as it encounters more real-world data, these figures will likely keep growing with further implementation.
Choosing the Right Maintenance Technology
All of these advances in maintenance technology can produce significant time and cost savings throughout manufacturing supply chains. However, investing in all of them simultaneously is not usually advisable. As helpful as new technologies can be, they also introduce high upfront expenses and can take time to integrate successfully. Consequently, organizations must determine which are most valuable to their specific operations.
IoT tracking is a safe first step, as it enables more disruptive approaches like PdM or AI analytics down the line. Even so, manufacturers must ensure they have the knowledge and technical means to secure IoT devices and support their network traffic before installing them.
It is often most useful to apply different methods to different machines. For all its advantages, PdM sometimes produces false positive rates of up to 10%, counteracting the potential savings. As such, PdM is best for high-value equipment with predictable breakdown patterns, while other assets may benefit more from condition-based IoT monitoring.
Manufacturers can identify the optimal way forward by highlighting which machines or processes showcase the greatest need for maintenance improvements. These case-specific issues can reveal which changes will be the most relevant. Investing in such areas first is key to maintaining profitability through digital transformation.
Preventive Maintenance Is Evolving in 2025
An efficient manufacturing supply chain needs a thorough preventive maintenance plan for all critical assets. These technologies provide the means necessary to create such a strategy.
As more businesses recognize the potential of these innovations, today’s cutting-edge solutions will slowly become the norm. Amid that shift, investing in maintenance advances early is key to keeping up with this evolving industry.
Comments (0)
This post does not have any comments. Be the first to leave a comment below.
Featured Product
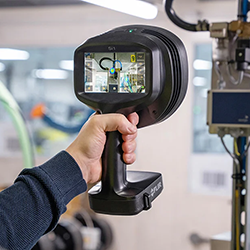