Small Town America's Newest Product: Advanced Manufacturing
76 Percent of U.S. Workers Do Not Fear Automation, According to Randstad US
If Foxconn builds a manufacturing plant in Wisconsin, it won't be what many expect
Robots May Help Defuse Demographic Time Bomb in Japan, Germany
Robotics, AI and 3D printing could close UK's productivity gap
Why Germany Still Has So Many Middle-Class Manufacturing Jobs
More production, more jobs? CMU pitches businesses on robotics in manufacturing
GE Launches Brilliant Skills Curriculum to Train Workers for Digital Industrial Future
GE Launches Brilliant Skills Curriculum to Train Workers for Digital Industrial Future
A3 to Kick Off Automate 2017 with White Paper on Jobs in the Automation Age
Staying Rich Without Manufacturing Will Be Hard
Mnuchin on robots taking US jobs: 'It's not even on our radar screen ... 50-100 more years' away
Japan worker shortage has only one winner so far: robots
Hot Jobs Study Reports Manufacturing a Top Industry
MakerBot is laying off a third of its staff, narrowing focus under Stratasys
Records 61 to 75 of 95
First | Previous | Next | Last
Featured Product
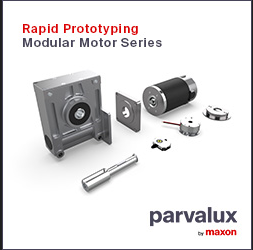