These days almost all industrial automation engineers fall victim to three toolset options to build their applications
Why an Open “Plug-and-Play” Platform is The Answer for Industrial Automation
Dipesh Mukerji | KingStar
What is the number one thing that industrial automation engineers want at work?
It’s simple: the freedom and flexibility to choose the best tools without reservation.
That autonomy, however, is rarely achieved, not just in industrial automation but practically any industry these days. Oh sure, plenty of tooling vendors say they provide flexibility in areas like motion control or machine vision, but there is almost always a catch or loophole. These days almost all industrial automation engineers fall victim to three toolset options to build their applications:
- Proprietary solutions, with vendor lock-in
- Point solutions, buying best-of-breed for every desired component, which can get expensive
- Hardware solutions, that are obscenely expensive
There are pros and cons to each of these options, but none is honestly desired by the engineer; it’s more like “pick-your-poison.” Why? Engineers want top quality solutions, but don’t have the wherewithal to develop the necessary integrations in a timely fashion. That’s where best-of-breed gets expensive; not just in the technology itself, but in hooking all of the pieces together. So organizations go with Plan B, a single vendor solution that is not best of breed, but saves the integration headaches.
Motion control, machine vision and other industrial automation engineers want to be free to use any component in the market that they choose without hesitation or reservation, from PC-based operating systems, to hard real-time determinism, to industry standard fieldbuses, to motion control and machine vision APIs and algorithms, down to the PLC. An open platform makes this possible.
The beauty of the open platform is that the platform replaces the integration effort all together: the best-of-breed components simply plug into the platform and not directly to each other. In doing so, the platform handles the integration and thus delivers the quality and performance that far exceeds that of the single solution vendor, because every component is optimized.
For example: the benefit of a single vendor solution is that because every component comes from the same vendor, every component – PLC, motion, network cables, network protocols – is pre-integrated and works together. The customer benefits because they do not need to do any integration, which translates to big savings. However, the customer also can suffer because some components are best-of-breed and others are not. Maybe the PLC is outstanding but the network sucks – very slow performance, no scalability, and the drives do not have fine resolution. Worse, the customer has no ability to change the network to EtherCAT or another faster standard. This limitation is often overlooked.
KINGSTAR addresses this problem with an end-to-end, open and standards-based software platform that allows engineers to pick components of their choosing for motion control and machine vision from the ground up. Built on the foundation of hard real-time deterministic 64-bit operating system (RTOS), IntervalZero’s RTX64, all components chosen by a motion control engineer can either be KINGSTAR’s pre-integrated and pre-tested solutions or ones of their own choosing.
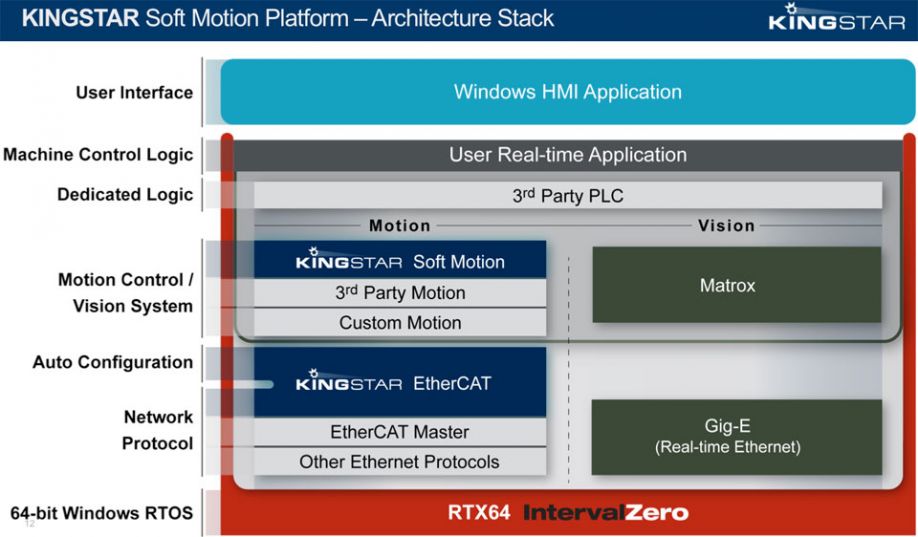
Let’s say you want to leverage the increasingly popular EtherCAT fieldbus as your industry standard. You have the freedom and flexibility to choose either KINGSTAR’s basic CANopen over EtherCAT, or you can choose an EtherCAT master of your choice like Acontis, Koenig or ESD. Let’s say you want to leverage your own customized soft motion control algorithms and APIs. No problem; you can integrate your own customized solution into EtherCAT or leverage KINGSTAR’s own robust set of Soft Motion Control algorithms.
It doesn’t stop there. What if you wanted to add machine vision-directed motion control? Well, then options like KINGSTAR or Matrox’s Imaging Library are completely available to you. Finally, if you want to complete the full set by leveraging your favorite PLC for HMI, then go right ahead and choose PLCs like ISaGRAF or PHOENIX CONTACT as your application management system.
In other words, the customer gets to have their cake and eat it too: They get the benefit of pre-integration (they do not have to Integrate) and all their components are state of the art.
Though there are other software solutions in the market that profess to be such a platform, this is in fact a veneer. Other vendors will offer you such components as custom- or vendor-offered soft motion and PLCs, but the brass tacks come down to having to use their own specific proprietary scripting language that does not give direct access to a general purpose RTOS, but only to their specific RTOS via predetermined and controlled access points. With KINGSTAR, you have a truly transparent open platform that lets you use languages that you already know, like C, C++ and .NET, in order to access ALL platform components and create motion control and machine vision applications.
The strength of a platform is that it can integrate the best-of-breed components for the highest quality and performance. The more components there are in the platform, the stronger the platform is. KINGSTAR is already strong in this regard, and in the future, more and more components can and will be added to this open platform for availability, such as Kinematics (for CNC and Robotics) and Simulation.
About KingStar
The KINGSTAR Soft Motion Platform is a software-only solution that outperforms hardware and other competing software solutions with precision performance at half the cost. KINGSTAR is an open and standards-based, integrated platform that enables motion and vision control engineers to design, develop, and integrate motion and vision control applications with KINGSTAR’s Soft Motion library and software PLC. It is built on the foundation of EtherCATand a real-time 64-bit Windows operating system, and is a complete platform for functional integration.
The content & opinions in this article are the author’s and do not necessarily represent the views of ManufacturingTomorrow
Comments (0)
This post does not have any comments. Be the first to leave a comment below.
Featured Product
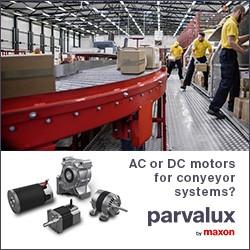