The ADDere system is a wire fed DED (direct energy deposition) additive manufacturing solution. The solution is designed to provide near net shape structures using hot wire and laser power.
The ADDere System by Midwest Engineered Systems
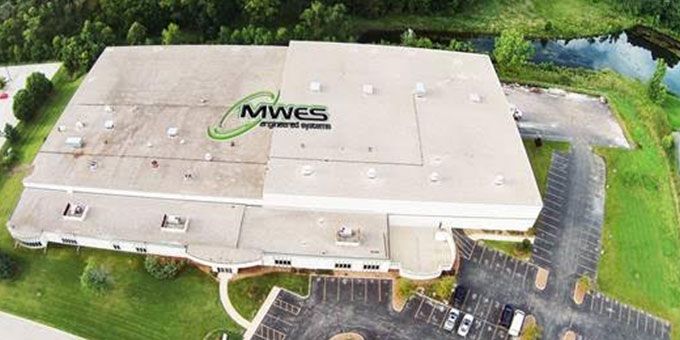
Scott Woida | Midwest Engineered Systems
Tell us about MWES
Midwest Engineering Systems Inc. provides custom machines, integrated systems, automation/robotic solutions, and production lines to manufactures globally. Our engineering staff has technical expertise, a diverse knowledge base, and has built thousands of integrated automation systems over the last 20+ years. Not only does MWES provide new equipment, but also process development, training, support, service, maintenance, and retrofits for all factories’ automated manufacturing equipment.
Can you tell us about ADDere and how it is involved in additive manufacturing?
The ADDere system is a wire fed DED (direct energy deposition) additive manufacturing solution. The solution is designed to provide near net shape structures using hot wire and laser power. The ADDere system can produce deposition rates from fractional to in excess of 40 lbs/hour. ADDere is a fully integrated additive manufacturing solution ready for the production environment. The ADDere system is a full production solution much like a machine tool is to the subtractive market.
What makes the ADDere system special is our use of sensing technology during the additive process. The ADDere system continually monitors dimensional and environmental data during the additive process. The system uses a closed loop feedback system to trim and maintain system parameters such as laser power, wire speed, deposition distance and many others parameters to maintain consistent and quality deposition during the entire additive process. The system also allows the user to configure the specific feedback and closed loop characteristic to their specific process requirements, allowing the user to create a proprietary process unique to their material requirements.
Being a division of Midwest Engineered Systems, how does this differ you from a competitor who is also involved in additive manufacturing?
Being a division of one of the leading systems integration companies has certainly been a benefit to the development of the ADDere system. Having experts in mechanical system design, control system design, robotics, lasers and welding process has certainly accelerated the rate at which we are able to bring a product like ADDere to the market.
In laymans terms, how would you describe the benefits of additive manufacturing?
The ability to produce small quantities of relatively complicated parts quickly is one of the main and most obvious benefits to additive manufacturing. The industry is just beginning to discover how transformative the technology will be for the future of manufacturing. The technology is allowing engineers to think differently during the design process allowing them to combine mechanical components that would be impossible to manufacture using traditional manufacturing methods. It also allows engineers to design without penalty, meaning that engineers are able to try many iterations of component design and quickly get tangible results.
What are some of the challenges you faced when first tackling this new endeavor?
The challenges that come with an R&D effort to develop something like ADDere is significant. There are many different technologies that have to be brought together for a system like ADDere to work. Hardware and software need to be tightly integrated and the process needs to be completely understood for the control loops to perform the correct functions.
What do you see 5 years down the road for additive manufacturing?
Additive manufacturing will continue to evolve in the coming years. Obvious things like the AM machines becoming more affordable and engineers gaining a better understanding of how to design for the additive process. We also see the trend of designing for additive manufacturing and buying contract printing time on a machine rather than owning your own. This is similar to how the Uber model works for the transportation industry.
About Scott Woida
Scott Woida graduated with a Bachelor’s degree in Electrical Engineering from the Milwaukee School of Engineering (MSOE) in 1987. In 1991, Scott founded Midwest Engineered Systems. It was his goal to design and build automation systems for local manufacturers. As his business and staff began to grow, Scott diversified Midwest Engineered System’s capabilities into other markets ncluding, custom machine design, drives systems/converting, and robotic automation.
The content & opinions in this article are the author’s and do not necessarily represent the views of ManufacturingTomorrow
Comments (0)
This post does not have any comments. Be the first to leave a comment below.
Featured Product
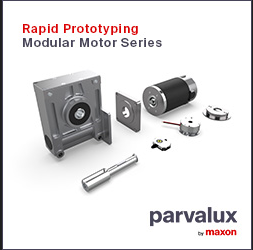