As most facilities managers can attest to, the electricity used to produce compressed air can be one of the most expensive energy costs in your facility.
Tame Your Energy Hog with Accurate Compressed Air Measurement
Scott Rouse | Sierra Instruments, Inc.
How do you tame the compressed air energy hog in your facility? As most facilities managers can attest to, the electricity used to produce compressed air can be one of the most expensive energy costs in your facility. Questions arise such as: How can I verify my compressed air capacity? How do I balance distribution and allocation in my factory? Why am I losing pressure in my lines? The key is to have accurate compressed air flow measurement devices to gather data on your usage and create a usage profile.
In the past, facilities have used insertion turbine meters for compressed air measurement, but turbine meters don’t work well with low compressed air flows. Alternatively, insertion pitot tubes are an option, but they don’t measure direct mass flow. Both technologies are prone to clogging. Thermal mass flow metershave become the most reliable and stable devices to give you accurate compressed air measurements to conduct your audit.
Glen Coblentz, VP Sales North America for Sierra, gives some in-the-field tips to figuring out what is happening with the compressed air in your facility in his new Flow Tip Video, “Tame Your Energy Hog: Compressed Air.”
3 Tips For Understanding Your Compressed Air Usage
1. Direct thermal mass flow meter measurements are more accurate than traditional insertion turbine meters or pitot tubes.
In most facilities, compressed air usage typically varies widely throughout the day, from very heavy at times of peak manufacturing to small flows (perhaps due to leakage) when most production is on standby. With more accurate compressed air flow measurement, companies are putting a price tag on compressed air and making educated choices that lead to cost savings. In the past, most companies used volumetric, or non-compensated, flow meters, which can present challenges in compressed air measurement. For example, even a small change in operating temperature can result in these instruments showing a 5 to 10 percent reduction in accuracy.
Thermal mass flow meters, however, are ideal for compressed air audits because direct mass flow measurement is immune to changes in operating temperature and pressure. Thermal flow meters also have a very wide turndown (100:1) to handle peak and low flow fluctuations. They also have little to no pressure drop, which saves money since the facility has already paid to have the air compressed. One facility reported a $7,500 to $44,000 annual savings through improved compressed air system management and/or replacing their compressors with more energy efficient units—a substantial cost-cutting investment with relatively short-term payback.
2. Measure both your mass flow & pressure for a complete understanding of your compressed air usage.
To really understand what’s going on with the compressed air in your facility, you need to measure both the mass flow of your compressed air and at what pressure it’s running. If you don’t have both of these measurements, you could be venting compressed air out of your roof or have a major leak. Thermal mass flow meter devices with volume, temperature, and pressure sensors (VTP) built in will give you the mass flow rate and the pressure at the point of measurement. Knowing both the mass flow and pressure can help you answer key questions, such as: Do I have leaks in my compressor system? Is my compressor running at capacity? Is the downstream demand too great? This valuable information could even allow you to turn off a compressor that is over-producing, saving thousands on energy bills.
3. All is not well if your pressure is dropping but the mass flow across the pipe is not changing.
If your mass flow is stays constant, but your pressure is dropping, this lets you know that your compressors can’t keep up with your downstream demand. In this case, you need to verify your compressor capacity and the compressed air allocation. The other problem with this scenario is that if your mass flow stays the same and your pressure drops, your velocity in the pipe will increase exponentially. This can cause major damage to downstream valves, as well as cause a lot of noise and discomfort to your employee. So tame that energy hog with smart, accurate, mass flow pressure measurements.
Compressed Air Management with QuadraTherm
As part of Sierra’s Big-3™ suite of Flow Energy Management products for all gas, liquid, and steam flow applications, the QuadraTherm 640i/780i thermal flow meters have been specifically designed for precise flow energy management in compressed air and natural gas applications. QuadraTherm offers:
- Direct mass flow measurement of gases, eliminating the need for temperature or pressure compensation
- Wide 100:1 turndown
- Accuracy of +/- 0.5 percent reading; high flows 60,000 sfpm (0-305 smps); 100:1 turndown
- Multivariable Mass flow rate, temperature & pressure
- Advanced four-sensor “dry sense” technology minimizes drift and enables field validation
- Insertion version with hot tap capability for easy installation on large pipes
- Software applications for easy set-up, in-situ calibration, dial-a-pipe, and gas mixing
- Digital communications suite
The content & opinions in this article are the author’s and do not necessarily represent the views of ManufacturingTomorrow
Comments (0)
This post does not have any comments. Be the first to leave a comment below.
Featured Product
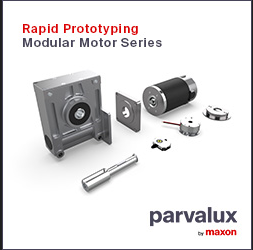