Energy Efficiency in Manufacturing and Data Management
Energy consumption is growing exponentially, while energy creation is increasing only incrementally. This imbalance requires innovative solutions. At Delta, we tackle this challenge from both sides-enhancing energy creation while optimizing energy consumption.
Practical Steps for Measuring and Reducing Your Business' Carbon Footprint
In this guide, we walk you through some basic concepts and provide a step-by-step guide for how best to decarbonize your operations quickly and on a tight budget.
Examining the Integration of Hydrogen Fuel Cell Tech in the Manufacturing Supply Chain
Many, if not all, manufacturers today recognize the need to revamp supply chains. Improving sustainability, increasing efficiency and lowering operational costs are key elements of this change, and hydrogen fuel cells can help in each area.
Implementing AI for Energy Efficiency in Manufacturing
AI for energy efficiency gains requires dedication, but the effort yields an optimized, self-sufficient machine. Early AI adopters using it to progress corporate social responsibility and lower building emissions garner favor among client bases for their initiative.
How Robotics and Energy Management Systems Can Collaborate to Achieve Zero-Energy Manufacturing
As industries increasingly focus on sustainability, the intersection of robotics and EMS has become crucial. This collaboration enhances manufacturing efficiency while playing a pivotal role in reducing energy consumption and minimizing environmental impact.
The Benefits of Predictive Maintenance Capabilities in Energy Management Systems for Industrial Facilities
Future trends in predictive maintenance focus on leveraging AI and machine learning to improve system accuracy and efficiency, and integrating IIoT for enhanced connectivity and data exchange in smart factories.
The Role of Energy Management Systems in Smart Factories
Energy management systems include Internet of Things (IoT) sensors, smart transformers, connected HVAC equipment and cloud computing platforms to control it all. While implementing this technology can be daunting, it plays several key roles in smart factory operations.
Heat pump with heat exchanger instead of electric heatings Saving 169 MWh of electricity per year
To exploit the existing potential in the cleaning of engine components, a premium car manufacturer replaced the electric water heating system in its Austrian works with a heat pump. This has resulted in electricity savings of approx. 70 percent per year in this process step.
Coping With Rising Energy Prices - Can Manufacturers Remain Profitable Against Energy Uncertainty?
There is currently no end in sight for increasing energy costs. Nevertheless, it's an opportunity for manufacturers to reevaluate their current supply chains and internal processes, and embrace more energy efficient production through Industry 4.0.
Variable speed drives: the dark side
According to ABB, the power and automation company, the addition of a VSD can reduce energy consumption by as much as 60 per cent. This means that, if a 90-kW motor in continuous operation is combined with a VSD, financial savings can amass to over £9,000 per year.
Creating Energy Resilience in Your Manufacturing Facility
Achieving energy resilience at a manufacturing facility or elsewhere is a two-part process. First, it requires ensuring you have a reliable power supply. Next, an energy-resilient company must have thorough plans for how to respond if a power failure occurs.
Developing Solar Heat for Use in Manufacturing Facilities
Modern solar heat systems incorporate new technology, like smart sensors and other items to improve efficiency. They have found a home in a wide range of industrial facilities - and could help the manufacturing industry reduce emissions created by heating.
What Is a Load Bank and Why Do Manufacturers Need Them?
A load bank can be an important asset in a variety of industries. Load banks are stationary or portable tools that mimic the expected electrical load on a power source in a commercial or industrial setting.
The Right Choice 40 Years Ago. The Right Choice for the Next 40 Years
By working with Leslie Controls, a customer protected their original investment and was able to work through the plant re-certification process cost-effectively
ABB uses AI to revolutionize energy management
ABB and Verdigris Technologies have developed machine-learning algorithms to predict unplanned peaks in power consumption - and identify strategies to prevent them
Records 1 to 15 of 16
Featured Product
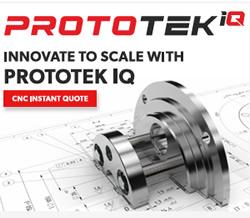
Prototek IQ - Digital Manufacturing Services
Prototek IQ is our new instant quoting platform that simplifies your manufacturing process. With just a few clicks, you can get accurate quotes for 3D printing and CNC machining, which are currently two different platforms. Our easy-to-use interface helps you make smart choices. Use Prototek IQ to improve efficiency and streamline speed to market. We invite customers with experience in large projects, 3D printing, and CNC machining, as well as those with repeat orders, to try our instant quoting platform. You can choose our engineer-assisted quote option if you have unique needs, such as high quantities, specific quality standards, fast delivery, or special finishes.