There are many innovative use-cases in manufacturing for mobile software. Some of the more prevalent examples will be discussed below.
The Applicability of Mobile Software Solutions in Manufacturing Facilities
Bryan Christiansen | Limble CMMS
Mobile technology is quickly spreading through manufacturing facilities, and it’s not hard to see why this is happening. The cost of mobile technology has rapidly decreased in the past five years. Many experienced technicians are retiring, and the loss of knowledge is not easily replaced.
At the same time, software solutions have become more available and accepted in manufacturing. Younger generations are used to mobile technology and expect it in the work environment. Naturally, technology has begun to replace the years of experience on the manufacturing floor.
There are many innovative use-cases in manufacturing for mobile software. Some of the more prevalent examples will be discussed below.
Procedures
An area of quick return is through digitization of standard operating procedures. If someone wants to repair something at home today, one of their first steps is likely YouTube - they can typically find a video detailing the process. Apply this concept to the production environment. It is a much richer experience for an operator to see a video of the process immediately before he starts it.
This concept can be taken further by fully integrating the procedure into a task-based list using a software such as Workflow. Integrated workflow software can link operator actions with PLCs or other business systems, improving efficiency and reducing errors.
Augmented Reality Training
One of the most powerful uses of mobile tech is through Augmented Reality (AR). This allows the user to view information out on the manufacturing floor through a mobile device. The possibilities are great, but the discussion will begin with training.
Manufacturing is struggling with developing and retaining expertise on the production floor. As mentioned in the intro, many experienced operators and maintenance technicians are retiring, and they cannot be easily replaced.
New employees can be brought up to speed quickly using AR. They can be trained out on the line, seeing the equipment and interacting through the mobile device without having to shut it down. This is a much more valuable real-world experience than the traditional classroom.
Mobile CMMS
The modern manufacturing facility can make utilize a mobile CMMS for truly powerful control of its maintenance. There are numerous reasons to use a computerized maintenance management system, and the advent of mobile CMMS provides even more benefit to a business.
With mobile devices, the business gains from better CMMS data and better access to data. Before a maintenance technician starts a work order, he can easily access all of the past work orders on a specific piece of equipment.
Technicians can log and make comments right at the machine, rather than trying to remember all the details at the end of the shift. Pictures can be taken easily and filed directly into the CMMS report.
This process can be augmented further with the use of barcodes or QR codes on equipment. Rather than searching for the proper motor in a database of hundreds, the equipment tag can be scanned. In this way, the proper CMMS information is always linked to the correct equipment. The maintenance team can quickly and accurately find all work orders associated with the equipment they are working with.
Dashboarding
A mobile device can provide instant insights into a process or piece of equipment without having to walk back to the Human Machine Interface (HMI). This allows for quick feedback and walkdown of process areas.
Or, in some cases the HMI is not located in an area where the operator might normally be. A mobile device could display Key Process Indicators (KPIs) to an operator wherever they go.
Other important information could also be displayed on the mobile device. The cost of the materials being consumed or made, the amount of energy used, or the status of the manufacturing order could all be displayed to the operations team. This would give them the information they need to help maximize profitability of the facility.
Troubleshooting
Mobile devices can also be used for troubleshooting the process. With a mobile readout of process parameters, a person can get feedback anywhere, not just near an HMI. This can help with identifying the root cause of a manufacturing problem.
Along with displaying process information to a troubleshooter, software can also be used to guide them through a standard troubleshooting process. This is another area where experienced production members can be more easily replaced. Typically, this knowledge is only gained through experience of problems, but this experience can now be leveraged into a software solution.
Mobile devices can also be used to collaborate remotely in a troubleshooting event. Perhaps a vendor needs to be consulted, and this task can be completed using a video call. The team can even work together using an AR software from Scope AR, with one person guiding the other by drawing on the screen.
Summary
Mobile software solutions are becoming more common in modern manufacturing environments. The opportunity for improving production efficiency with mobile technology has never been greater. Examples are plentiful, and most are relatively easy to implement. They range from procedure management and information access all the way to process control.
At each implementation step, the intent is to improve the job of the worker through by creating the environment for a faster, more automated processes and eliminating points of human failure. Utilizing a wide spectrum of mobile software, manufacturing facilities are improving their bottom line and making the experience better for the modern production worker.
About Bryan Christiansen
Bryan Christiansen is the founder and CEO at Limble CMMS. Limble is a modern, easy to use mobile CMMS software that takes the stress and chaos out of maintenance by helping managers organize, automate, and streamline their maintenance operations.
The content & opinions in this article are the author’s and do not necessarily represent the views of ManufacturingTomorrow
Comments (0)
This post does not have any comments. Be the first to leave a comment below.
Featured Product
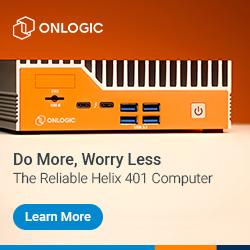