As there are more and more success stories associated with the use of AM as a production technology, scrutiny on the process is becoming increasingly forensic in nature.
Optimising Performance and Manufacturability for Additive Manufacturing
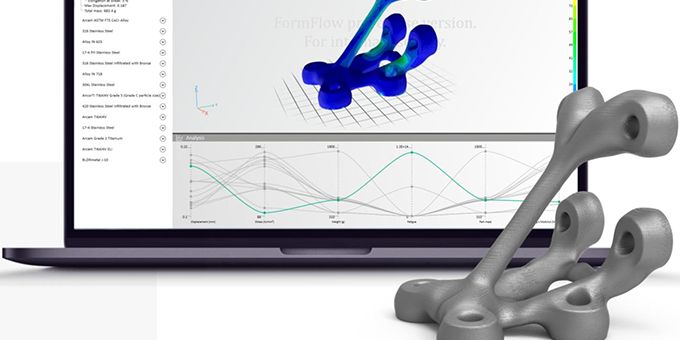
Alexander Pluke, CEO | Additive Flow
Today, the conversation concerning additive manufacturing (AM) is moving on apace. As there are more and more success stories associated with the use of AM as a production technology, scrutiny on the process is becoming increasingly forensic in nature, and there is an understandable focus on the areas that the technology must improve to allow it to compete on more equal terms with conventional manufacturing techniques. Back when this technology set was in its infancy — and when AM was more usually referred to as rapid prototyping — there was much less emphasis on the finer aspects of the processes. Today, the discussion is much wider, with significant consideration being given to the optimization of the processes, as well as on the overall design to production cycle.
As this decade progresses, the drive towards the use of AM as a replacement for conventional manufacturing technologies for key applications is set to continue, and will primarily be focussed on new and existing applications where the use of AM brings a significant ROI across the value chain by reducing the overall time and cost of manufacturing. As a general rule of thumb, for AM to be used as an efficient production technology for any given application it needs to demonstrate — as a minimum — a 10-fold improvement in cost and/or time savings to offset the cost and risk associated with converting from a traditional manufacturing process chain.
There are applications in the public domain today that demonstrate this sort of ROI and value, There are suggestions that there are more in R&D, yet to be revealed publicly and there are infinitely more that have not been thought of yet. Because as good as AM is as a solution within its niche (and it is still a niche within the global context of manufacturing) there are still barriers to adoption that are stalling uptake and growth of AM.
A key barrier to adoption is the disconnect within the necessary workflow for AM. Just consider for a moment, the digital tools required for the physical output from an AM process. AM is widely considered a digital manufacturing tool, rightly so. It’s also often cited as an essential component of Industry 4.0. Aside from popular buzzwords, what are we actually trying to achieve here? This is the crux of the conversation, in my opinion. Any given AM system is just one component within a complex digital workflow that involves the creation (design), optimization, manipulation and simulation of data. Subsequent to these disciplines, the data must then be converted into a machine-readable form by way of the “slicers or build processors” before achieving the physical goal — the required part(s). Even at the first stage, the creation of the design data, there are myriad options of traditional parametric design software solutions, as well as new generative design options that facilitate form and functionality optimisation. Similarly, for design optimisation and digital part simulation there are many other options. the data required for a successful AM part will pass through many different stages on its journey. This journey is currently complex and requires serious know-how to navigate successfully through the various, often discrete, digital tools .
It is important to clarify a juxtaposition on complexity here.
AM enables complexity specifically in terms of part geometry and the physical building of complex shapes that are not possible with traditional manufacturing methods. Indeed this is a positive USP of AM compared with traditional manufacturing methods. However, the digital workflow required to facilitate AM applications throws up levels of complexity that can prohibit adoption, and this is a real challenge and it requires a new approach.
The “good” complexity has led to advanced and enhanced levels of creativity and innovation for AM applications, where unprecedented levels of design freedom have resulted in new design methodologies for geometrically complex products. As mentioned there is now a plethora of examples of generative design software modules that can produce lattice structures and topologically optimised structures for optimal performance and light-weighting benefits.
It is within this narrow scope that the general discussion around optimisation for AM applications often lies. I believe it must be extended to realise the latent potential of AM.
A BROADER VIEW OF OPTIMIZATION
It is fair to say today that when the AM community talks about optimisation, they are generally referring to design optimisation. Topology optimisation, for example, seeks to achieve the best possible design for a structure by changing material distribution within the design space in order to achieve required functionality and maximize performance. Similarly, the proliferation in the (generative or otherwise) design of lattice structures, the production of which is singularly enabled by AM, has the potential to deliver applications with new functionality including high levels of energy absorption and stiffness, while at the same time offering light-weighting advantages and reduced material consumption. These are both positive benefits of new design thinking that are driving new and/or improved applications of AM. It goes without saying that optimisation remains imperative as a digital design discipline, but what I am saying is that it needs to be moved on, with a more holistic approach and more connected digital tools that can apply a multi parameter approach simultaneously.
In this way, a more holistic approach requires intelligent and multi-functional digital tools that can optimise the design geometry, material placement and AM process parameters in a single environment — in essence allowing designers and engineers to optimise their entire digital workflow and remove the unwanted complexities from it. This capability will unlock the next level of performance from AM and industrial 3D printing technologies. The rationale behind this is the foundation of Additive Flow and the development of our modular and multi-functional software designed to streamline the digital process chain, remove complexity, and add real value to AM applications.
A MULTI-FUNCTIONAL APPROACH
Adopting a multi-functional and holistic approach, we have developed a flexible set of digital tools that can simultaneously consider material properties, geometry and material placement, hardware systems, and build parameters. This increases multi-property performance and optimises the outcomes for AM applications, applicable across material systems (metal/polymer/ceramic) and combinations for compatible multi-material applications, within the boundaries of material science where defined materials and material properties can be combined through the manufacturing process. We have achieved this with a multi-physics, multi-property topology optimisation approach.
WHY?
To address common challenges experienced within the Design for Additive Manufacturing (DfAM) workflow and pre-production preparation, FormFlow is a broader type of optimisation software that incorporates multiple unique functionalities enabled by specific physics-driven comparisons of the design, material, AM process parameters, and production output against key performance indicators (KPIs) as defined by specific application priorities.
Alcoa airplane bearing bracket challenge. Fixed geometry process parameter topology optimisation.
These capabilities offer considerable time- and cost-efficiencies to the entire digital workflow and go well beyond the typical capabilities of discrete generative design, topology optimisation, and design simulation software tools, while incorporating all of these capabilities.
Put simply, FormFlow puts the right material, with the right properties, in the right place; optimises part geometry and material properties simultaneously; subsequently allows users to simultaneously view productivity, cost, and performance of different materials, multiple materials, and different geometry optimisations; and quickly and efficiently produces optimised production files according to multiple user-defined parameters.
Moreover, FormFlow is AM-process agnostic with specialist solvers that account for the unique properties in AM materials and can be tailored to work with single- and/or multi-material designs.
I believe we are the first company to commercially offer these simultaneous capabilities to maximise performance and manufacturability for additive manufacturing.
OVERCOMING ISSUES INHERENT IN AM
Additive Flow’s FormFlow solution addresses some inherent characteristics within AM processes that can be easy to overlook. For example, AM processes in general exhibit variations in physical properties along the build axis (anisotropy), where the 3D printed part behaves differently depending on the direction of force applied to it. This usually means that 3D printed parts behave differently to forces applied perpendicular to the build direction.
If these are ignored, or the standard isotropic solvers on the market are used, optimisation results will invariably be wrong, and in such a way key safety factors may be missed and/or true optimisation opportunities lost. This anisotropy plays an even greater role within composite structures, where fibre orientation delivers enhanced engineering properties in particular directions. The solvers within FormFlow ensure that the opportunities for anisotropic optimisation can be realised for every application.
AM also allows for the adjustment of parameters throughout the printing process, or the application of different parameters to different regions of a part. This has the potential to unlock productivity, cost, and performance improvements when compared with traditional manufacturing processes.
However, the complexity of manually deciding which regions should have which property sets can be time-consuming and complex. FormFlow addresses this through the use of multi-property optimisation algorithms, the software having the capability to address different parameter sets within an optimisation while enabling skilled engineers to apply their parameter knowledge seamlessly across a split mesh.
SUMMARY
Additive Flow is working on a project consultancy basis with myriad companies from OEMs to SMEs and AM ecosystem players. This is enabled by the modular architecture of our software,and can be deployed across customised workflows with all of its multi-functionality, or it can be applied specifically to unlock particular bottlenecks in any given workflow.
As well as bringing modular and scalable multi- functional digital solutions to the market that can be customised to specific applications, at the heart of Additive Flow is sustainability in modern day product development and manufacturing environments. The company was founded on the principle of disrupting AM for an improved world by focusing on reducing manufacturing impact on the environment; enabling sustainable designs and sustainable use of materials; driving improved recycling; all while supporting safer workplaces.
The content & opinions in this article are the author’s and do not necessarily represent the views of ManufacturingTomorrow
Comments (0)
This post does not have any comments. Be the first to leave a comment below.
Featured Product
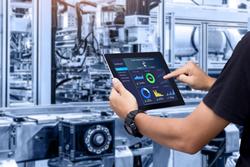