With the constant growth in demand for manufactured goods and environmental protections under coordinated assault, there’s never been a more important time for manufacturers to take their part in air pollution seriously.
How to Prevent Industrial Air Pollution in Manufacturing
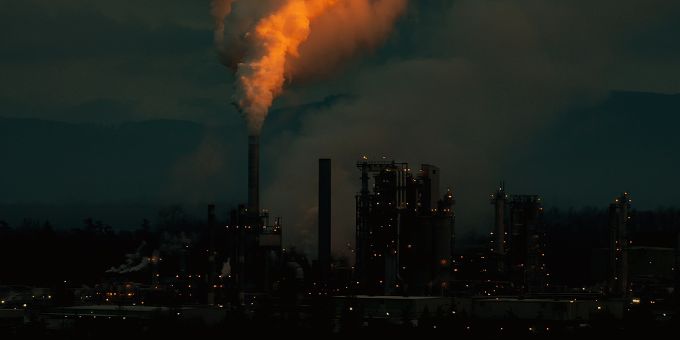
Scott Huntington | Off The Throttle
With the constant growth in demand for manufactured goods and environmental protections under coordinated assault, there’s never been a more important time for manufacturers to take their part in air pollution seriously.
Industrial manufacturing, along with the construction industry, were the two largest polluters in 2018, both contributing to the second-largest year-over-year increase in air contaminants in two decades.
Some of the most common airborne pollutants generated by manufacturing and other industrial sectors include volatile organic compounds (VOCs), hazardous air pollutants (HAPs) and solid particulate matter (PM). Experts link these and hundreds of other contaminants to severe health problems in humans and wildlife, environmental degradation and contaminated air and water supplies.
Manufacturers must keep our air clean and healthy. The following provides a look at some of the most effective ways to minimize and prevent industrial air pollution emanating from factories.
1. Make the Switch to Clean Energy Sources
Facilities that use coal or natural gas to generate electricity contribute to water and air pollution all over the world. Scientists also link these resources to breathing problems, heart attacks, neurological damage, cancers and other grave and chronic health problems. Paper and concrete manufacturing plants are some of the heaviest users of fossil fuels in manufacturing, but they are far from alone.
Whereas pollutants from coal are responsible for a $74.6billion annual impact on public health in the U.S., clean energy generated from solar and wind contribute no air pollution whatsoever. Biomass and geothermal systems are an acceptable middle-ground — they create some air pollutants, but in vastly lower levels than natural gas — and especially coal-fired plants.
Natural gas is, however, another imperfect but net-positive choice for manufacturers looking for an alternative to more destructive fossil fuels. Natural gas outputs negligible sulfur- and mercury-based pollution.
Additionally, according to the Union of Concerned Scientists, for every 10,000 homes — or the equivalent manufacturing facilities — powered with natural gas, global society stands to eliminate 1,900 tons of nitrogen oxide, 3,900 tons of nitrogen oxide and 5,200 tons of particulates per year that would otherwise enter the air and surrounding environment.
2. Use Technology to Destroy Pollutants at the Source
For cases where it’s not feasible to switch to clean energy immediately, some manufacturers turn to a variety of technologies to destroy air pollution at the source before it enters the earth’s atmosphere. These abatement technologies nullify the most destructive air pollutants, like those mentioned above, and reduce the ecological footprint of manufacturing sites.
Several mechanisms are available that provide this functionality, but not all of them are effective for every pollutant. Some of the relevant technologies include:
-
Catalytic oxidizers: These machines use intense temperatures and chemical catalysts to render air pollutants down into their constituent compounds, which may then be harmlessly released.
-
Regenerative thermal oxidizers (RTOs): With RTOs, factories repurpose industrial waste heat to destroy pollutants within networks of heat exchangers.
-
Rotary concentrators: Like the name suggests, rotary concentrators rotate at high speed to separate air pollution into a hydrophobic media, where an oxidizer destroys it.
Carbon dioxide is perhaps the best-known air pollutant and contributor to climate change, but there are others — including cadmium, mercury, sulfur dioxide and hydrogen sulfide.
Wet scrubbers are another air pollution mitigation technology to consider, and they deliver the benefit of tackling both gaseous waste, like these, as well as particulate matter before it can enter the atmosphere or the surrounding environment.
3. Choose Non-Toxic Materials to Manufacture Goods
Far too many companies rely on supply chains riddled with raw materials that have the potential to become toxic once released into the air and water. Milling and grinding processes, like those that drive paint and coating operations, release ground-level ozone, VOCs, particulates and heavy metals into the atmosphere, where they impact the health of humans and wildlife.
The Environmental Protection Agency recommends that manufacturers identify raw materials and additives containing chromium, mercury and lead, and replace them with non-hazardous biocide alternatives. Doing so maintains these products’ desirable bacteria-eliminating properties without the risk to health and air quality posed by heavy metals.
Styrene is another material to watch for and eliminate from the supply chain. Atomized styrene can enter the air while fiberglass and plastics are being manufactured or sprayed in place. Instead of risking kidney disease, chronic fatigue and other health problems, manufacturers can substitute low-styrene gels and resins or use materials that rely on ultraviolet curing instead of traditional methods.
Naturally, there will be times when there aren’t any convenient material substitutions to be made. Silica dust, which comes from quartz, is a common and extremely harmful particulate pollutant generated by the manufacture and installation of masonry products, soils, concrete and other construction products.
Training workers to handle essential materials like these, and providing them with adequate protective equipment and exposure plans is essential under OSHA standards as well as common sense.
4. Deploy More Effective Enterprise Planning Techniques
Imbalances between supply and demand have a more direct impact on air pollution than you might expect. When factories are powered up and cranking out products for which there’s little demand, they are contributing to air pollution unnecessarily.
The act of manufacturing products that aren’t needed contributes to air pollution from one end of the product’s life cycle to the other. In the United States, solid waste in landfills is the third-largest contributor to methane emissions. Municipal waste also increases levels of VOCs and other pollutants in the air.
What this means is that manufacturers across the world must find ways to more finely tune the balance between supply and demand and keep unneeded factory activities to a minimum and unwanted products out of the supply chain and distribution networks.
Deloitte points to predictive analytics and machine learning as a way to find this balance. These technologies keep manufacturers, distributors, retailers and customers on the same page with respect to demand for products. They also predict and optimize the best approach to manufacturing activities, production schedules and a host of other supply chain activities so that only essential operations are underway at any given time.
Clean Air Is Good for the Environment and Good for Business
It’s extremely difficult to ignore the importance of eliminating industrial waste, including air pollution. The World Economic Forum says it plainly enough — clean air is good for business. The previously mentioned impact on healthcare costs translates into missed shifts and poor productivity. The world could lose 3.8 billion workdays per year by 2060 if trends continue.
Given all of this, there’s plenty of reason for manufacturers to take air pollution more seriously. Now we know a few ways to do so.
The content & opinions in this article are the author’s and do not necessarily represent the views of ManufacturingTomorrow
Comments (0)
This post does not have any comments. Be the first to leave a comment below.
Featured Product
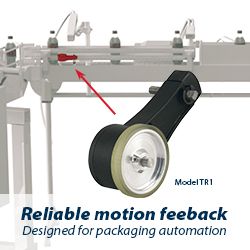