There's no question that additive manufacturing will continue growing in the coming years. Some experts expect the 3D printing industry to surpass $20 billion by next year, but what will that look like?
Trends for 3D Printing in Manufacturing
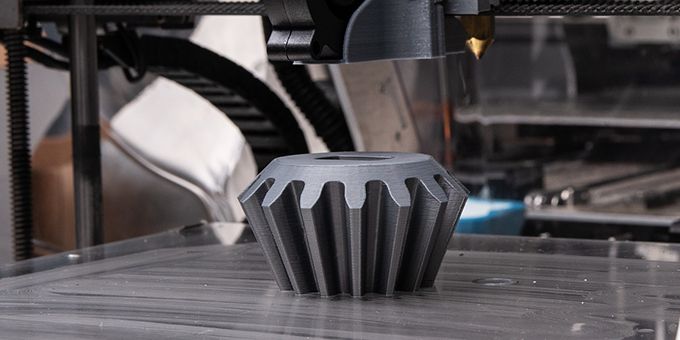
Article from | Martin Banks
3D printing, or additive manufacturing, is one of the most revolutionary technologies to come to the industry. While it has yet to surpass traditional manufacturing techniques, it's well on its way to becoming mainstream. More and more manufacturers are adopting this technology, especially as it keeps improving.
There's no question that additive manufacturing will continue growing in the coming years. Some experts expect the 3D printing industry to surpass $20 billion by next year, but what will that look like? Here are 10 trends that will grow in 3D printing in manufacturing in the near future:
1. On-Demand Spare Parts Production
One of the most promising applications for 3D printing in manufacturing is the production of spare parts. In a traditional setup, if a machine breaks, employees have to go to storage for a spare part or even order a new one. With 3D printing, they could fabricate the needed part in-house in a matter of minutes.
On top of saving time, this would save inventory space. Manufacturers would save money and be able to improve operational efficiency. These benefits are too significant for manufacturers to pass up, so more facilities will apply 3D printing here.
2. Eco-Friendly Filaments
Sustainability is becoming a more prevalent concern for businesses and consumers alike. In a 2019 survey, 47% of internet users said they've switched products because a company violated their values or beliefs. Eco-friendliness is becoming a necessity for manufacturers, so eco-friendly 3D printing filaments will rise.
Most 3D printing applications use plastics, but that may change in the coming years. Materials like plant-based filaments or those recycled from organic waste will become more popular. By shifting toward these materials, the additive manufacturing industry will become more sustainable and marketable.
3. Modeling Printed Parts on Virtual Machines
As useful as 3D printing is, it still isn't perfect. Some printed parts may not perform under pressure, and manufacturers often can't see these flaws until it's too late. As a result, more facilities will start using virtual models to test part designs before they print them.
With a virtual machine, manufacturers can model how a part of any material or design will perform. They can then print the best design with confidence, and since 3D printing is so fast, modeling won't make the process too long.
4. More 3D Printing in Prefabrication
Prefabrication has always been a popular application for 3D printing, and this trend will continue. Whenever a manufacturer starts making a new part or product, they can use 3D printing to create an early model. This reduces waste and saves time, allowing manufacturers to move from planning to application quicker and more affordably.
As more manufacturers prefabricate products with 3D printing, it could lead to them taking more risks. Since it wouldn't cost as much to model new creations, more companies may be willing to experiment with different designs.
5. 3D-Printed Circuit Boards
Additive manufacturing techniques and materials are becoming more advanced all the time. Recent developments have allowed people to print circuit boards, which will likely become a trend. As gadgets become a more significant part of life, demand for circuit boards is rising, so printing them is a natural next step.
3D printing provides everything a highly in-demand product needs. It's fast and affordable, and it doesn't use a lot of materials. Additive manufacturing could produce circuit boards of various shapes and sizes in bulk, fueling the Internet of Things (IoT) revolution.
6. Hybrid Manufacturing
Some manufacturers may not be ready to adopt 3D printing just yet. As a result, in the next few years, there will likely be a rise in hybrid manufacturing, which provides a middle ground. By using a combination of 3D printing and traditional manufacturing techniques, facilities can experience the benefits of both.
3D printing technology may not be at a level yet where it can replace subtractive manufacturing. A hybrid approach offers a sensible middle ground as the industry transitions.
7. Increased Customization
The digital age has allowed for increased personalization, and consumers are starting to demand it. To meet this demand, more manufacturers will likely turn to 3D printing to offer custom products. Additive manufacturing can create virtually any design on one machine and do so quickly, making it ideal for this application.
More than 50% of consumers show interest in personalized products, and 25% will pay more for customization. As made-to-order products become more in-demand, more manufacturers will adopt 3D printing.
8. Application-Specific Materials
Customers aren't the only group that will continue to demand more customization. Since 3D printing takes less time and space than traditional techniques, manufacturers could use it to work with application-specific materials. Instead of designing products and parts around their available resources, additive manufacturers will create materials that fit their desired end product.
3D printers are remarkably flexible when it comes to the range of materials they can work with. This flexibility allows manufacturers to experiment with application-specific materials, ultimately leading to better products.
9. Metal Printing
Traditional manufacturing involves a lot of metal, which has been a stumbling point for 3D printing in the past. Printing metal is possible, but many early metal printers and filaments were expensive. Costs are starting to fall now, which will likely lead to an increase in metal printing.
With more affordable prices, metal 3D printing could disrupt the industry. It would allow manufacturers to experience both the speed and versatility of 3D printing with the strength and resilience of metal. More adoption will also lead to increased funding for development, leading to even more affordable metal printers.
10. In-Situ Monitoring
As people look to make 3D printers more reliable, in-situ monitoring will become more common. This process involves using sensors to detect qualities of a product or part as manufacturers print it. With this technology, additive manufacturers could see and address any flaws as they print.
In-situ monitoring will lead to fewer errors, eliminating time spent on fixing them. As a result, additive manufacturing will become a more viable option for more processes.
Additive Manufacturing Is on the Rise
As this technology continues becoming cheaper and more advanced, 3D printing plays an increasingly significant role in manufacturing. These trends are just a taste of how additive manufacturing might develop over the next few years. The future may be uncertain, but all signs point to 3D printing rising among manufacturers.
The content & opinions in this article are the author’s and do not necessarily represent the views of ManufacturingTomorrow
Comments (0)
This post does not have any comments. Be the first to leave a comment below.
Featured Product
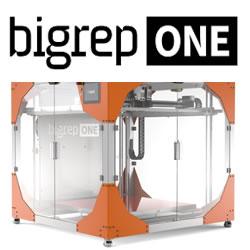