Every operation has different goals and resources, so what lean looks like will vary. Still, there are some general concepts you can follow to create a lean assembly line.
How to Go Lean With Your Assembly Line Layout

Emily Folk | Conservation Folks
The modern manufacturing industry is a highly competitive environment. If you want to stay ahead of your competitors, you'll have to maximize your profits wherever you can. One of the most effective ways you can do this is by creating a lean assembly line.
Popularized by Toyota, lean manufacturing seeks to optimize production by eliminating waste. It's the concept of cutting out everything you don't need to run the most efficient operation possible. While the idea is straightforward, putting into practice can seem like a challenge at first.
Every operation has different goals and resources, so what lean looks like will vary. Still, there are some general concepts you can follow to create a lean assembly line.
Eliminating Waste
The first step in pursuing a lean operation is taking inventory of what you do. Some experts estimate that 60% of production activities are wasteful, contributing nothing to the customer. That doesn't mean you have to aim for a 60% reduction in your assembly line but look for waste.
According to Toyota, there are three main categories of waste:
-
Muda, which is any process that doesn't add value for the customer.
-
Mura, which means unevenness, like fluctuating workflows.
-
Muri, which refers to doing too much work at once, resulting in overburdened staff or equipment.
Look for these three areas of waste in your operation. Is there anywhere in your assembly line where work isn't consistent? Do you take time to do anything that doesn't matter to consumers? If so, then you can adjust or remove these processes.
Precision helps eliminate a lot of waste. Taking time to ensure products are defect-free often saves time that you would otherwise spend addressing defects. Similarly, ensuring that you order and produce according to demand reduces waste due to surpluses and deficits.
Maximizing Productivity
A lean assembly line produces as much with as little as possible without sacrificing quality. One of the keys to achieving this is ensuring that everything and everyone meets its full potential. Assess your assembly line to see if there's anything that could be doing more.
Some manufacturers can produce different parts on the same line, which saves space and reduces downtime. This kind of flexibility is central to lean manufacturing. If one process can work on various projects, you can adjust to maintain consistent production levels.
Remember that your best resources are your employees. Make sure you have an understanding of your workers' unique talents. Try to position everyone in a role that suits them best, which will increase both productivity and morale.
Mistakes to Avoid
While you're implementing a lean production strategy, you should be aware of some common pitfalls. Perhaps the easiest mistake to make is reorganizing your wokrlfow once and then leaving it alone. If you want to get the most out of your assembly line, you should embrace continuous improvement.
Regularly reevaluate your operation. There will always be some area where you can improve, so going lean is an ongoing process. Make sure you keep track of your performance metrics so you can see what works and what doesn't.
Other factors to keep in mind are safety and product quality. While you're trying to increase efficiency, make sure you don't sacrifice either of these. No amount of productivity is worth an injury or a sub-par product.
Finally, keep in mind that you may not be able to change everything at once. Plan all of your changes ahead of time, but implement them slowly. If you try to do too much at once, you can't spot any mistakes as easily.
Optimize Your Assembly Line
Organizing a lean assembly line isn't an easy undertaking, but it can be a profitable one. By eliminating waste and embracing ongoing improvement, you can revitalize your production line. Start slow, plan carefully and pay attention, and you can make your production lean without worry.
The content & opinions in this article are the author’s and do not necessarily represent the views of ManufacturingTomorrow
Comments (0)
This post does not have any comments. Be the first to leave a comment below.
Featured Product
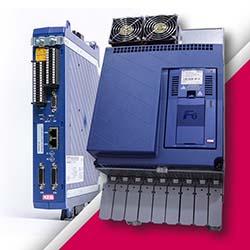