In this article, we'll discuss the main similarities and differences between two of the most established processes in 3D printing - stereolithography (SLA) and selective laser sintering (SLS).
3D Printing Technology Comparison: SLA vs SLS
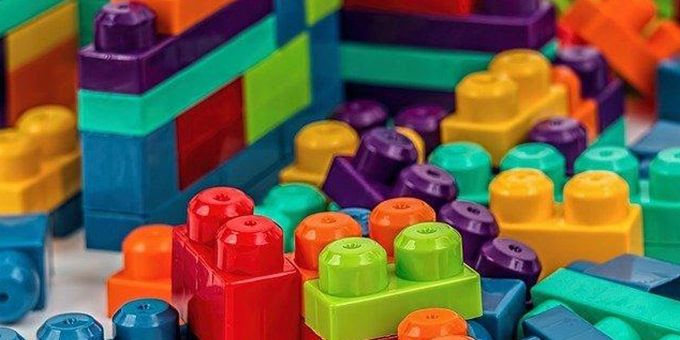
Article from | d3d Printing
3D printing technologies have made product design, testing, and manufacturing faster, less expensive, and less wasteful. Over the past few years, it has transformed industries ranging from automotive to medical. It also has opened up so many opportunities for business, especially to entrepreneurs and small businesses. Of course, the question then is, which 3D printing technology should you choose for your application?
By ZMorph3D
In this article, we'll discuss the main similarities and differences between two of the most established processes in 3D printing - stereolithography (SLA) and selective laser sintering (SLS).
What is SLA?
Stereolithography or SLA was the first 3D printing method ever. Invented in the 80s, this technology utilizes a laser beam to cure liquid resin, making it solid. This process is called photopolymerization. When printing, the laser draws a 2D section of the object on a thin layer of liquid resin. Then, the printer applies a new layer on top and the laser draws the next section of the object. This step is repeated until you get a complete 3D object. Once that happens, the object is soaked in liquid resin to "clean" it, removing any support structures that were created.
There are two ways that the laser of an SLA 3D printer can be moved. One is through the use of mirrors which is the most efficient and cost-effective method. The other method is by using a gantry to move the laser.
There are several advantages when using SLA. It can print objects more accurately and with clearer details. It produces a smoother finish. In addition, it offers versatility. This is because there are various photopolymer resin formulations available that come with a wide range of thermal, optical, and mechanical properties. For this reason, this 3D printing process is often used in a lot of industries such as product design, engineering, jewelry, and education. SLA is best used when creating molds, patterns, and functional parts.
What is SLS?
SLS is short for selective laser sintering. This 3D printing process is the most commonly used additive manufacturing technology for industrial applications. Similar to SLA, this method utilizes a laser that sinters, melts, or fuses particles of powder together to form an object. The power of the laser will differ between SLS printers which will determine the type of materials that can be printed.
The process starts with a thin layer of powder placed on top of a building surface. The laser beam then draws a 2D section of the object, sintering the particulates together. Another layer of powder is then applied on top of the first one before the laser does its job again. This process is repeated until you get a complete 3D object. The last step is to uncover the object that has become buried under the unsintered powder.
SLS printing is ideal for industrial applications because it can use a variety of materials, not just plastics. It can print with metals and ceramics as well. In addition, the unsintered material surrounding the object being printed can act as a support structure, eliminating the need to print those parts which means that you are able to print complex geometric structures and interlocking objects.
Comparing SLA and SLS 3D printing
There are certain similarities between these two processes as well as major differences. One thing you should note is that both methods can be used for custom 3D printing. Your choice will depend on the object you're printing, the material, the size of the printer, and the cost.
Material
Material selection is one of the main differences between SLA and SLS printing. As we've mentioned, the former utilizes polymers and resins. SLS can also use some polymers such as nylon and polystyrene. However, it can also use ceramics and metals such as steel and titanium.
Another difference in material is the form. SLA printing uses liquid resin which is toxic and messy. It can also be time-consuming to clean off a completed object during post-processing. SLS printing, on the other hand, uses powder which is much easier to deal with. However, breathing in particulates, particularly of some metals such as nickel, can be harmful to your health. You'll need to take into account the ventilation in your work area depending on the material you use.
Size
SLA printers are typically smaller which allows you to use them as a desktop machine. SLS printers, on the other hand, are quite large and considered "benchtop" machines. Aside from being larger, these printers also require quite a bit of power. That being said, SLS printers can print much faster. It can also build much larger models.
Cost
SLA printers are much more affordable. You can easily get one for less than $500. SLS printers, on the other hand, can cost you a minimum of $5000. However, the resins can be relatively expensive while some materials for SLS printing such as Nylon can be inexpensive.
Final Product
SLA-printed products can produce highly detailed parts with a smooth finish. However, depending on the resin formulation used, these parts are often strong but brittle, not entirely suitable for mechanical purposes. SLS-printed products, on the other hand, are strong and flexible, more suitable for mechanical purposes. It also allows for the creation of highly complex structures. However, the finished product tends to have a rougher finish.
About Louisa
Louisa is a content marketing professional and editor creating her successful career past 2 years at D3D Printing. She is a goal-oriented, creative individual with a unique voice in writing, editing, and optimizing content for various projects. She's a devoted mom and an excellent piano player.
The content & opinions in this article are the author’s and do not necessarily represent the views of ManufacturingTomorrow
Comments (0)
This post does not have any comments. Be the first to leave a comment below.
Featured Product
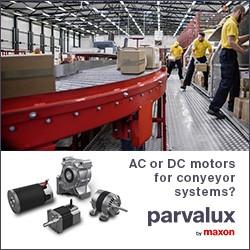