When obsolete components break, it can be hard to find like-for-like replacements. Managing obsolescence is therefore critical since the breakage or malfunction of obsolete components exposes the business to risk of costly downtime.
Tackling Obsolescence With Additive Manufacturing - 3D Printed Spare Parts Is Revolutionizing Manufacturing
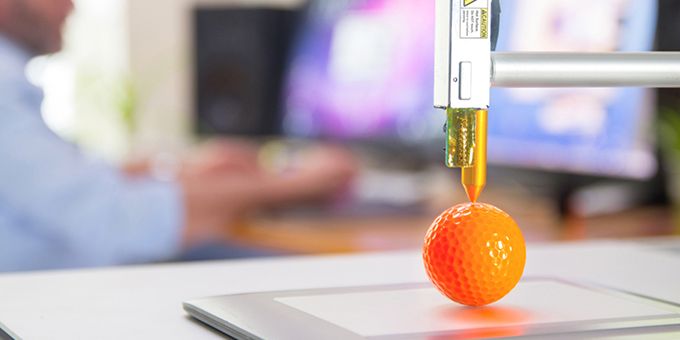
Claudia Jarrett, Country Manager | EU Automation Inc.
Obsolescence is an unavoidable part of any manufacturing environment. However, it’s concerning that nearly 70 per cent of companies admit they do not know when vital equipment requires replacing, or when they do, they scramble to find replacements. Here, Claudia Jarrett, country manager at automation parts supplier EU Automation, explains why the latest developments in additive manufacturing could provide a useful answer to the obsolescence problem.
The thesis by Pratik Pringle identifies a concerning problem, but one that has a solution. Additive manufacturing is a transformative approach to industrial production that enables the creation of components using a variety of 3D-printing techniques.
Before delving into issues surrounding obsolescence, let’s firstly define what we mean by 3D printing. The process starts with a component material, initially in the form of powder, which is melted with a laser layer-upon-layer to obtain the desired shape. Fundamentally, it’s about adding material instead of removing it like in traditional subtractive manufacturing.
The range of materials that can be used is almost endless — from innovative plastics and metal alloys, to concrete, wax, resins and even human tissue. One of the newest advances in additive manufacturing is the possibility, recently explored by Sandvik Coromant, to print with diamond powder, shaping the hardest material on Earth into any desired geometry.
And, due to additive manufacturing possibility to print intricate and hollow shapes with no scrap, only the necessary amount of material is added to the process. This has made it a popular technique in fields that require the production of highly specialist components in a small production run, such as aerospace or the biomedical sector, and has led to exploring how AM could help manage the obsolescence of manufacturing components.
The problem with obsolescence
Our society is characterized by rapid technological developments in the use of big data, automation and computing. These technologies have had a positive impact on manufacturing, allowing plant managers to maximize productivity, reduce waste and create a safer working environment for their employees.
On the other hand, technological components, both hardware and software, tend to have a shorter lifespan. As newer versions of the same components are marketed, the original equipment manufacturer (OEM) might stop producing the version purchased by the manufacturer, making it obsolete.
When obsolete components break, it can be hard to find like-for-like replacements. Managing obsolescence is therefore critical since the breakage or malfunction of obsolete components exposes the business to risk of costly downtime, or even to the possibility of having to upgrade an entire system.
Revolutionary
Material engineers are currently researching the potential of additive manufacturing to manage some aspects of obsolescence. The core idea is that if a component is no longer available from the OEM, it could be simply 3D-printed.
For example, the US Airforce has launched research into 3D printing replacement parts for old planes using the Figure 4 3D Printing Platform designed by 3D Systems. The US Airforce will examine how Figure 4 3D Printing Platform can reproduce components for aircrafts that are no longer in production.
This comes as the US Airforce often requires out-of-production parts due to manufacturing obsolescence, poor documentation and costs-to-create. And, as replacement parts can be built much faster and in smaller batches through additive manufacturing, no minimum order quantity will be required. In turn, reducing the time of aircrafts spend on the ground, and the need for warehousing space.
The question of electronics
As promising as this sounds for the aerospace industry, there are still questions that need to be answered before AM can become a standard way of coping with components obsolescence in other industries.
First of all, it is unclear to what extent AM could help manage the obsolescence of electronic components. This sector is one of those that most suffers the consequences of the increasingly short lifespan of components, due to the speed at which new products and solutions are launched on the market.
We could potentially 3D print any mechanical component, but it’s much harder, though theoretically not impossible, to 3D print something like a circuit board or cables and wires. Even when possible, manufacturers should consider the cost and complexity of 3D printing spare components.
Having onsite additive manufacturing capability may require an initial investment of more than £500k and a dedicated design engineering team. While these investments can make sense in an R&D environment, they might be counterproductive to produce spare parts that you might only occasionally need.
In cases like this, it is much faster and cheaper to rely on an automation parts supplier that specializes in obsolete components. Although obsolescence is an unavoidable part of any manufacturing environment, suppliers like EU Automation ensure manufacturers do not need to be scrambling around finding replacements.
3D printed spare parts could be the answer to replacing obsolete parts, but won’t completely replace the need for a strong parts supply network across the United States.
The content & opinions in this article are the author’s and do not necessarily represent the views of ManufacturingTomorrow
Comments (0)
This post does not have any comments. Be the first to leave a comment below.
Featured Product
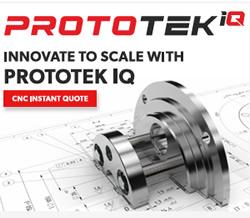