Additive Manufacturing (AM) has the potential to rewrite the economics of production. It offers the ability to create more complex geometries and structures than is possible with traditional methods, enables greater efficiencies and performance.
Lack of Automation is Holding Additive Back
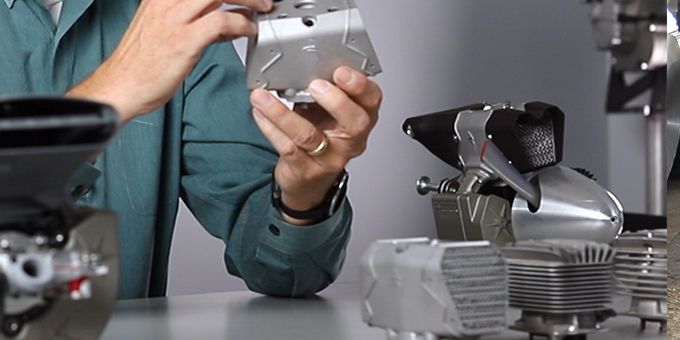
Anthony Graves, Head of Software Product and Strategy, Digital Manufacturing, HP | Dyndrite
So why hasn’t AM really delivered on its potential?
It’s not a question about whether these advances are possible. NASA has re-engineered a fuel injector and was able to reduce the number of parts in an assembly from 115 subcomponents to just two. A manufacturer of laboratory equipment was able to reduce the time to manufacture wax turbine molds by almost 90%, from 170 hours down to only 18, by using additive manufacturing. (Deloitte.) These are proven advancements with measurable economic impact. But as impressive as these gains are, they are too infrequent in production scenarios. While additive manufacturing is used regularly to produce concept models and functional prototypes, and gaining traction for low volume parts production, use within high volume production environments, where the financial impact would be significant, is growing much more slowly.
As a finished product design winds its way through the manual 3D printing build preparation process of positioning, nesting, creating support structures and slicing before finally being transferred to the printer, these costly devices often sit idle, underutilized, and waiting for input. Time Lost equals Potential Lost. It equals Money Lost. And if new or different parts need to be added to the build, the hours-long process begins again. Manual steps add time and they create opportunities for variance. Neither is acceptable at Cobra MOTO, where the pandemic’s focus on outdoor, individualized sports, has spurred record growth in mini motocross bikes. Its 3D printers need to be fully engaged and utilized, and their parts uniform and reliable.
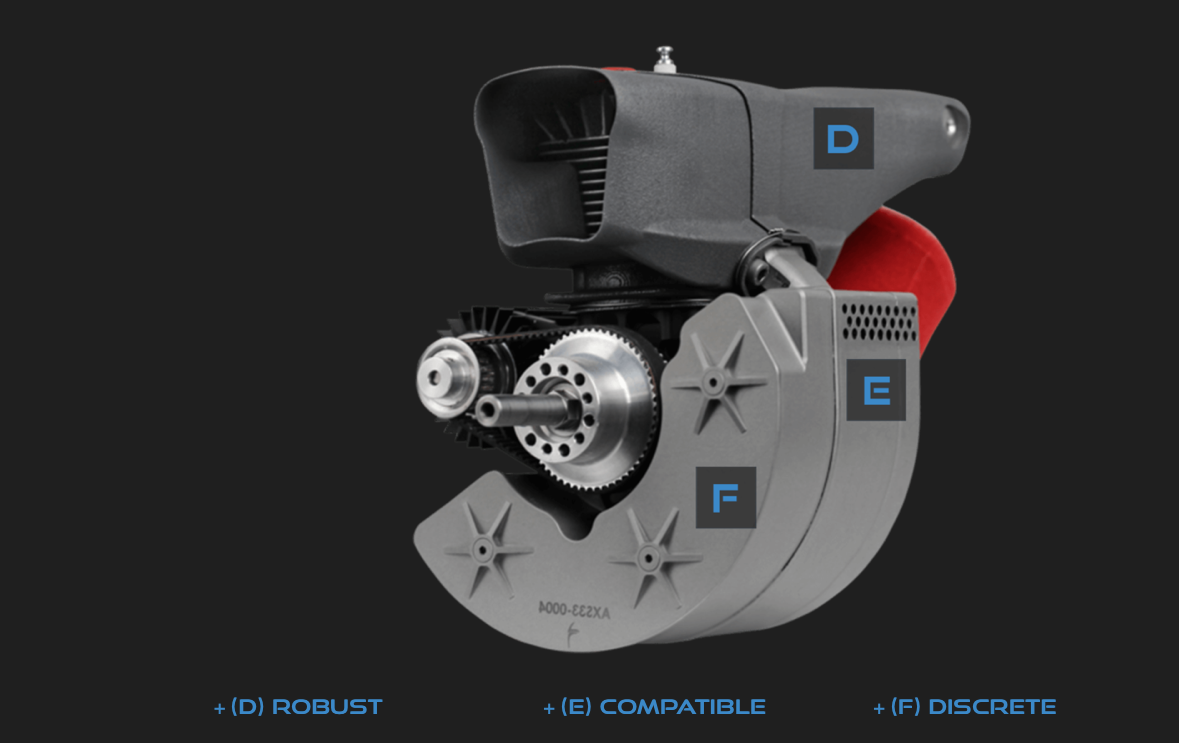
Engine parts and casings are benefiting from additive manufacturing at Cobra MOTO
“The demands on our teams are intense and highly complex,” said Sean Hilbert, President, Cobra MOTO. “Our ability to deliver safe, top notch products relies on optimizing our systems for both productivity and reliability. We believe the new HP Universal Build Manager Powered by Dyndrite will meet our needs, help us push limits and set the standard across our entire additive manufacturing processes.”
Cobra is not alone. For AM to succeed in production, it must be able to achieve a manageable, repeatable cost structure even as product or process complexity increases. Automation is critical. In fact, it has been described by industry leaders as one of the single biggest evolutions in 3D printing. Only by adopting automated, repeatable processes for additive production will manufacturers be able address problems with inconsistent part builds, minimize printer downtime and increase reliability and finally deliver the promise of this manufacturing process.
All of this, and more, was discussed during the Dyndrite Developer Conference 2021, in a keynote session featuring Anthony Graves, HP, and Sean Hilbert, President, Cobra MOTO. HP Universal Build Manager Powered by Dyndrite will also be demonstrated at ASME’s AM Tech Forum on June 17 2021.
The content & opinions in this article are the author’s and do not necessarily represent the views of ManufacturingTomorrow
Comments (0)
This post does not have any comments. Be the first to leave a comment below.
Featured Product
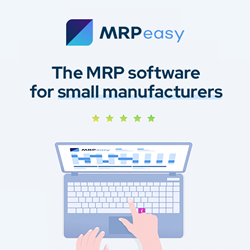