As businesses strive to stay ahead in this era of smart factories, the convergence of IoT, AI, digital twin, advanced HMI, and robust cybersecurity measures has become indispensable. At the heart of all of this is the seamless interplay between IoT and software engineering.
Unleashing the potential of smart factories: The critical role of IoT and software engineering

Dr Mariusz Stolarski, Global Head of Technology | Mobica
Dr Mariusz Stolarski, Global Head of Technology at Mobica, discusses how IoT and software engineering is powering the next generation of smart factories.
The digitalisation of industrial manufacturing is redefining how factories operate and compete, thanks to the integration of connected technologies.
As businesses strive to stay ahead in this era of smart factories, the convergence of IoT, AI, digital twin, advanced HMI, and robust cybersecurity measures has become indispensable. At the heart of all of this is the seamless interplay between IoT and software engineering.
But in powering the next generation of smart factories, what are the roles of each of these advanced technologies and how are they reshaping the manufacturing industry?
Modern technologies driving industry transformation
The Internet of Things (IoT) has emerged as the backbone of smart factories, enabling machines, devices and systems to communicate and collaborate.
By connecting equipment through the cloud, IoT facilitates the continuous flow of data, allowing manufacturers to monitor, analyse and optimise production processes. This connectivity not only enhances operational efficiency but also supports predictive maintenance, reducing downtime and extending the lifespan of machinery.
Artificial intelligence (AI) is revolutionising manufacturing by introducing automation, enhancing decision-making processes and enabling predictive analytics. AI-driven systems can autonomously control manufacturing operations, adapt to changing conditions and even anticipate issues before they arise. This level of intelligence promotes self-aware machines that contribute to a more agile and responsive production environment, ultimately leading to higher-quality products and reduced operational costs. It can also greatly optimise resource utilisation and minimise environmental impact.
Digital twin technology enables manufacturers to create virtual replicas of physical assets, systems or processes. These digital models enable precise simulations, prototyping and predictive analysis, which are crucial for optimising production and ensuring equipment reliability. By integrating “software-designed everything” (SDx) and smart maintenance strategies, digital twin technology empowers manufacturers to achieve greater precision and efficiency, while minimising risks and costs associated with physical prototypes.
The evolution of human-machine interfaces (HMI) is enhancing how operators interact with factory systems. Virtual reality (VR), augmented reality (AR) and extended reality (XR) technologies enable immersive experiences that improve training, maintenance and remote support. Additionally, gesture and voice control systems are streamlining operations by allowing for hands-free and intuitive control of machinery. These advancements in HMI are not only increasing productivity but also improving safety and worker satisfaction.
The many ways software engineering is transforming manufacturing
Having all this technology is all well and good – but as smart and powerful as it is, essentially it needs to be, “told what to do”. That’s why behind every smart factory lies the critical work of software engineers who are redefining the capabilities of manufacturing systems. Here’s how:
Modernising legacy systems is a cornerstone of smart manufacturing – and the results can be surprisingly good. Software engineers are extending the functionality and lifespan of existing systems by adding new features and improving performance. This includes enhancing security measures to protect against cyber threats, adapting to new regulations and standards, and ensuring older equipment can seamlessly integrate with new technologies.
Enablement of the connectivity that underpins IoT networks is vital, and requires careful software engineering to achieve.
Over the air (OTA) updates are vital for keeping systems up to date with the latest features and security patches. Much as the OTA brings indisputable value, it still introduces security challenges and needs to be carefully designed and implemented.
Engineering experts can support the business in evaluating the level of the software updates that should be remotely available. For example, should we always allow system-level updates, with interference up to the bootloader layers? In most cases, the application-level updates can still be sufficient.
IoT connectivity is also assuring proper M2M communication, the discovery of new devices within the IoT network, and satisfying the UNS (Universal Naming System) concept.
Additionally, automation solutions developed by software engineers allow for real-time decision making and autonomous operations, which are critical for maintaining the efficiency and responsiveness of smart factories.
Customisation and integration are vital because every manufacturing environment and every business is unique. This means IoT solutions must be tailored to meet specific operational and compliance requirements. Software engineers are at the forefront of customising and integrating IoT systems to ensure they align with industry standards and local regulatory frameworks. This ensures manufacturers can fully leverage the benefits of IoT without compromising on safety or compliance.
The importance of cybersecurity cannot be overstated as factories become more connected. Software engineers are developing robust security frameworks that protect against cyber threats and ensure the integrity of data and operations. From software good coding practices, encryption protocols to intrusion detection systems, these measures are critical for safeguarding the digital infrastructure of smart factories.
Rigorous feasibility testing and prototyping is essential before any new technology is implemented. Software engineers are instrumental in this process, creating simulations and models that validate the performance, reliability and feasibility of new systems. This step is crucial for minimising risks and ensuring the transition to a smart factory is smooth and successful.
When extending the legacy systems, especially, but in software development in general, it is more than good practice to professionally implement test automation (CI/CD) which allows to eliminate the regressions and control the software debt.
What does the future hold for smart factories?
Given the magnitude of the transition, it’s taken a long time to get to where we are today. And we’re still not there yet. For a variety of reasons – maybe concerns about up-front costs or staff re-training, some businesses are still playing catch up. But the future of smart factories is brimming with possibilities, driven by the continuous evolution of IoT, AI and software engineering.
As these technologies advance, we can expect to see even greater levels of automation, self-optimisation and predictive capabilities within manufacturing environments. And as the technologies become more affordable, we should see those yet to start, or who are in the early stages, of their digitalisation journey catch up.
Beyond that, smart factories of the future may require minimal human intervention, with AI and IoT systems working in concert to deliver unparalleled efficiency and quality.
Furthermore, the integration of next-generation HMI and digital twin technologies will continue to push the boundaries of what is possible, creating manufacturing processes that are more agile, adaptable and resilient.
The technology and possibilities have already advanced in the last decade far quicker than we could have imagined – so who knows where we will be in another 10 years.
Deep understanding
In the rapidly evolving world of manufacturing, staying ahead requires more than just adopting new technologies – it demands a deep understanding of how to integrate and leverage these innovations effectively. At Mobica, we are at the forefront of this transformation, offering unparalleled expertise in IoT and software engineering. Our solutions are designed to help manufacturers not only keep pace with the change but lead the way in creating the smart factories of tomorrow.
Visit mobica.com to discover how Mobica can help your manufacturing business work smarter.
The content & opinions in this article are the author’s and do not necessarily represent the views of ManufacturingTomorrow
Comments (0)
This post does not have any comments. Be the first to leave a comment below.
Featured Product
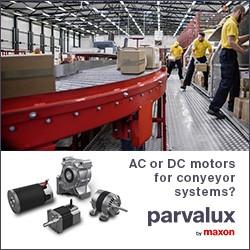