Overcoming challenges to drive sustainable manufacturing for a low-carbon future
Working towards a more sustainable, low-carbon future in the manufacturing sector by addressing the often-overlooked issue of hydrogen wear.
By Leyla Alieva, CEO and Co-founder of NEOL Copper Technologies
Manufacturing is the backbone of modern economies, driving innovation, economic growth, and technological advancements across the globe. In the UK alone, manufacturing contributes £224 billion annually to the economy and accounts for 9% of total GDP1. Beyond its economic importance, however, the manufacturing sector also plays a critical role in addressing some of the world's most pressing environmental challenges, particularly those related to sustainability and climate change. As industries across the globe strive to reduce their carbon footprints, cleaner energy solutions have gained prominence, and one of the most promising among them is low-carbon hydrogen.
Hydrogen is emerging as a pivotal element in the shift towards greener manufacturing practices. According to projections, global hydrogen production is expected to reach 60 million tons by 20302. This growth is largely driven by its potential to transform industrial processes, significantly reducing carbon emissions and providing a cleaner alternative to traditional fossil fuels. Low -carbon hydrogen's ability to provide clean energy without emitting greenhouse gases during use makes it a key player in the journey towards a sustainable future.
Addressing hydrogen wear
The widespread adoption of hydrogen in manufacturing is not without its challenges. One of the most critical issues is the impact of hydrogen on the machinery and engines used in industrial processes. Hydrogen can cause significant wear and tear on equipment, leading to material degradation over time. This degradation, often referred to as ‘hydrogen wear', reduces the efficiency and lifespan of machinery, resulting in increased waste and resource consumption. If left unaddressed this could limit the environmental benefits that hydrogen offers by negating some of the carbon reduction gains through the need for frequent replacements and repairs.
Managing hydrogen wear is essential if manufacturers are to fully leverage the potential of hydrogen as a clean energy source and contribute meaningfully to global efforts to reduce carbon emissions. One of the most effective ways to do so is through the implementation of advanced materials and technical lubricants that can withstand hydrogen's corrosive effects. By investing in these innovations, manufacturers can enhance the durability and performance of their equipment, leading to a range of benefits that support both economic efficiency and environmental sustainability.
Using more resilient materials and environmentally friendly lubricants can significantly extend the lifespan of machinery, reducing the need for frequent replacements. This not only cuts down on manufacturing waste but also conserves the resources required to produce new equipment.
Additionally, fewer breakdowns and repairs translate to less downtime and lower maintenance costs, making hydrogen-powered operations more economically viable for businesses. Ultimately, this approach reduces overall resource consumption and helps minimise the carbon footprint of industrial operations, contributing to a more sustainable manufacturing sector.
The future of hydrogen
As the world shifts towards cleaner energy sources like hydrogen, it is crucial that the manufacturing sector takes proactive steps to manage the challenges that come with this transition. By promoting technological advancements that address hydrogen wear and supporting sustainable manufacturing practices, the industry can make substantial progress towards toward a low-carbon future. This not only benefits the environment but also strengthens the long-term sustainability and efficiency of global manufacturing.
Featured Product
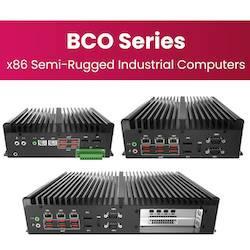
RCO Series x86 Super-Rugged Industrial Computers
Premio's RCO Series redefines rugged edge computing by offering comprehensive solutions optimized to meet the demands requirements of Industry 4.0 edge AI applications. With super-rugged durability, real-time performance capabilities with x86 Intel processors, extensive IoT connectivity, and scalable EDGEBoost technologies, this series of industrial computers are engineered to excel in diverse high-specification deployment challenges. From AGV/AMR deployments to smart manufacturing, the RCO Series is fully optimized to deliver 24/7 operational reliability and real-time AI performance.