The Future of Automotive: 3D Printing for On-Demand Manufacturing
3D printing is reshaping automotive manufacturing through on-demand production, customization, and sustainability. With support from automotive consulting, manufacturers can streamline processes, reduce costs, and strategically adopt additive technologies to stay competitive and future-ready.
The automotive industry is going through a transformation, with demands surging toward innovations and inventions. Today, the giant auto manufacturers are eyeing 3D printing as a means to enhance their vehicles and create groundbreaking advancements. Work is underway to reshape mobility, including the world of autonomous vehicles and electric vehicles. The on-demand production will ease, allowing the automobile sector to witness extraordinary designs. It promises to chicken out the traditional supply chain systems while accelerating manufacturing cycles, offering robust inroads through 3D printing technology. Moreover, it has opened the floodgates for extensive customization, catering to the diverse needs of buyers.
How Automotive Experts Enable Strategic Adoption of 3D Printing?
The capacity and potential offered by 3D printing technology are immense. However, its adoption can become successful with the help of accurate strategies from experts, and automotive consulting companies play an important role here:
- Execute workflow and training integration across production teams and design teams
- Identify the ROI and feasibility of 3D printing for various applications
- Ensure there's seamless compliance with safety and regulatory standards for printed components
- Choose the correct materials and technologies based on the requirement
- Design and craft digital transformation, aligning with the automotive manufacturers' goals
With the growth of the market, vehicle manufacturers will gain significant advantages by partnering with the right automotive consultants, who can offer them a competitive edge in additive manufacturing.
Key Applications of 3D Printing in Automotive
— Prototyping and Design Validation: The prototyping phase and design testing can be accelerated through 3D printing, enabling rapid iteration and quick manufacturing of vehicles.
— Tooling and Fixtures: On-demand production of custom tools and fixtures can be created. For example, BMW utilized 3D printing to produce bionic robot grippers that were lightweight, offered improved precision, and ensured lower energy consumption during the manufacturing process.
— Spare Components: The production of lightweight, durable parts can be ensured by 3D printing. For instance, the giant automobile manufacturer BMW manufactures over 300,000 parts using this technology every year. That also includes components for its electric vehicle models.
Advantages of 3D Printing in the Automotive Sector
— A Smarter Alternative: The traditional methods of vehicle manufacturing are labor-intensive and require a significant amount of expertise, manpower, and investment in building infrastructure. Also, it is not sustainable for the environment and requires dies, molds, and tooling equipment. On the other hand, 3D printing eliminates the need for tooling, thereby reducing upfront costs. Moreover, it utilizes materials that are necessary to create different parts, minimizing waste production without the need for excessive material.
— Faster Time to Market: Vehicle development is a time-consuming and complex process that overtakes development cycles. However, 3D printing can accelerate the process. It can reduce the loop of design-test-modify from weeks to days. Additionally, it can mitigate the delays that occur in traditional supply chains, enabling on-demand production and facilitating speedy delivery and service. The ability to achieve a quick time to market or turnaround can be a significant advantage in a competitive scenario that can define success.
— Hyper-Customization: In today's world, automobile sales heavily depend on personalized experiences that extend beyond mere reliability. 3D printing enables manufacturers to customize vehicles on a large scale, offering personalized dashboards, bespoke body parts, and tailored interior trims tailored to customer preferences. It helps inculcate customer satisfaction and opens a new revenue stream in the aftermarket and personalization service market.
Sustainability and Waste Reduction
Carbon emission reduction is no longer a choice but imperative for every industry to contribute to that, and 3D printing helps in sustainability and reducing waste in many ways:
— Enables the production of lightweight parts for enhanced fuel efficiency
— Supports closed-loop manufacturing and recyclable materials
— Minimizes material waste during production
— Allows local production, reducing emissions due to shipping
Thus, 3D printing aids the automotive industry in shifting toward circular economic goals and carbon-neutral principles. Interestingly, some companies are using bio-based or recycled materials in 3D printing to further minimize their environmental impact.
Industry Case Studies: Real-World Implementations
1. General Motors- The company uses binder jetting technology to create large-scale automotive parts, including underbody structures for luxury and premium vehicles. This methodology enables material efficiency and improved production capacities with precise accuracy.
2. Standard Motor Products- The company has deployed 3D printing to cater to the custom requirements of tooling and fixtures for clients. Notably, it has reduced costs by up to 90% while minimizing lead times by over 70%. The manufacturing process has become more efficient and streamlined, enhancing overall productivity.
Challenges Posing Issues
Any innovation and its application are not without challenges, and so does the execution of 3D printing in the automotive sector come with its own set of hazards that must be overcome. Here are some of the obstacles posed by the technology
1. Quality Assurance: Meeting the parameters and standards for the durability and quality of printed parts, equivalent to or better than those of the machine, is a challenging task that may require intensive testing protocols.
2. Material Limitations: Suitable 3D printing substitutes are lacking for certain high-performance materials, creating challenges for automobile manufacturers.
3. Skill Gaps: The lack of skilled engineering teams can cause delays in manufacturing. Therefore, spending on training is necessary for design-for-additive-manufacturing (DfAM) principles.
4. Production Speed: High-volume component production on a mass scale may still require a traditional manufacturing approach for optimal outcomes until the technology evolves to a more advanced level.
Future Trends in Automotive 3D Printing
— Integration with IoT and AI: Real-time monitoring will take place seamlessly with the integration of artificial intelligence and the Internet of Things (IoT). Additionally, it will also enhance predictive maintenance, further bolstering manufacturing efficiency.
— Advancements in Material Science: The application of 3D printing is expected to expand with industrial research into incorporating high-quality new and compatible materials on a large scale in automotive manufacturing. It will enable the production to deliver enhanced properties in parts.
Conclusion
The application of 3D printing in the automotive sector is not a new phenomenon; it is already here and requires strategic planning for accurate deployment among automobile manufacturers, aiding them with design and innovation. For manufacturers seeking to streamline the manufacturing process, automotive consultants can be beneficial, enabling them to control costs through various means, including expert guidance in the 3D printing market.
Additionally, in the competitive automotive industry landscape, sustainability and rapid change are crucial for staying relevant in the market.
However, there are hurdles too, such as regulatory, material, and engineering expertise in the domain, but these can be overcome with time by automakers.
Featured Product
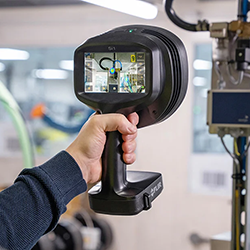