Laser Components Group Expands with In-House Pbs and PbSe Detector Production
This latest company addition demonstrates its commitment to providing customers with the choice of selecting the best detector for their particular application.
LASER COMPONENTS Group (LCG), headquartered in Olching, Germany, has announced the significant expansion of its research, development, and production capabilities with the addition of the PbS and PbSe infrared detector product lines. The new facility is a welcome addition to the existing LASER COMPONENTS Detector Group (LCDG) site located in Tempe, Arizona. The 3-5 micron wavelength response of these Lead Salt detectors will complement the existing infrared components portfolio that includes the InGaAs PIN Photodiodes and Pyroelectric Detectors already manufactured by the LASER COMPONENTS Group.
This latest company addition demonstrates its commitment to providing customers with the choice of selecting the best detector for their particular application. In a statement about the LCG continued investment and focus in infrared technologies, Group General Manager Patrick Paul explains, "Since its founding in 1982, Laser Components has specialized in IR components. Its collective know-how is extensive. Customers now profit from our in-house production facilities worldwide. As we offer IR detectors that implement different technologies, it is possible for our customers to always find their ideal solution. Gas measurement, for example, can be carried out using InGaAs, PbS/ PbSe and Pyroelectric Detectors. Depending on what exactly needs to be measured, one technology is more ideal than the other. The advantage of individualized assistance can be offered by very few other manufacturers; we not only offer this help but also manufacture custom products."
Full scale Lead Salt device production has begun after careful and rigorous prototype testing verified high quality performance. Every indication points to LCDG becoming the technology leader in detector manufacturing. Inventive fabrication techniques developed by LCDG at the Arizona State University Center for Solid State Electronics Research Laboratory and in-house automation have brought LCDG to the production of PbS and PbSe detectors that feature high sensitivity. Dragan Grubisic, LCDG General Manager, said, "We can truly say that we will advance the state of the art."
The products will be introduced to the market at Photonics West 2015 in San Francisco, CA USA.
Featured Product
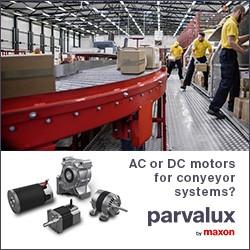